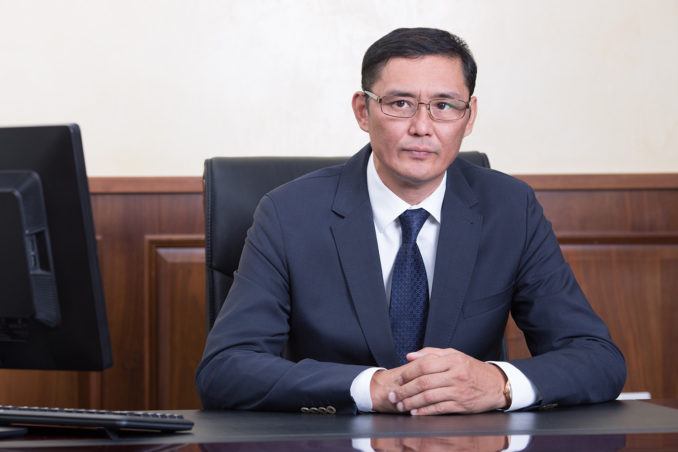
Ардагер Куандыкович Аринов, главный обогатитель Горно-обогатительного комплекса ТОО «Корпорация Казахмыс»
Технологии обогащения сульфидных руд, применяемые на Жезказганских обогатительных фабриках корпорации «Казахмыс», позволяют достигать высокого выхода конечного продукта. Компания постоянно внедряет новые разработки, проводит масштабные исследования в области переработки отходов обогащения.
Беседовала Светлана Демент
«Мы заботимся о рациональном использовании природных ресурсов и постоянно работаем над восполнением минерально-сырьевой базы Жезказганского региона», — говорит главный обогатитель Горно-обогатительного комплекса ТОО «Корпорация Казахмыс» Аринов Ардагер Куандыкович.
— Ардагер Куандыкович, история Жезказганских обогатительных фабрик начинается в далеком 1947 году. Как строилось и развивалось предприятие на протяжении последних 73 лет?
— Вопрос о строительстве Жезказганской обогатительной фабрики возник как историческая необходимость, поскольку вся руда, добываемая в Жезказгане, отправлялась на Урал. По решению руководства Главмеди и Наркомата в 1947 году была заложена Жезказганская обогатительная фабрика № 1.
В проектировании принимали участие Ленмеханобр, Московское проектно-конструкторское управление треста «Центрэлектромонтаж» и Промстрой. Генеральным проектировщиком всего комбината был Гипроцветмет. Корректировка проекта и чертежей была закончена в 1950 году, в последующие три года велись строительно-монтажные работы. Производительность фабрики была определена в 5,2 млн т руды в год. Из них 4 млн — медных сульфидных руд и 1,2 млн — медно-свинцовых руд.
В декабре 1953 года строительство первой очереди фабрики было закончено, и 22 декабря она приняла первые вагоны руды, запустила под разгрузку первую секцию главного корпуса № 1.
— Кто сегодня руководит технологическим процессом на предприятии?
—Главный инженер Жезказганских обогатительных фабрик № 1, 2, 3 — Мырзабеков Алмаз Кабашевич. За время работы он принимал участие в большинстве работ, проводимых совместно различными институтами и предприятиями. Например, внедрение новых типов флотомашин РИФ-25, МФКПМ-25, Усольмаш,
ТК-20-2, МЕК-25; в совершенствовании схем измельчения в Главном корпусе № 1 и Главном корпусе № 2; в модернизации гидроциклонов диаметром 750 мм; внедрение схемы переработки окисленных руд и других работ исследовательского и текущего характера.
— Какая схема обогащения руды применяется на Жезказганских фабриках?
— Жезказганские обогатительные фабрики № 1, 2 (ЖОФ № 1 и № 2) объединяют два обогатительных производства с законченным циклом обогащения и совместной переработкой получаемых концентратов на Жезказаганском медеплавильном заводе (ЖМЗ).
На ЖОФ № 1, 2 перерабатывают медные сульфидные руды подземной и открытой добычи, медные смешанные и окисленные руды открытой (карьерной) добычи, шлаки и корки металлургического производства ЖМЗ.
Медные руды Жезказганского месторождения по запасам являются основными. С 2008 года на ЖОФ № 1, 2 начата переработка медной руды подземной добычи рудника Жомарт.
Товарная продукция Жезказганских обогатительных фабрик № 1, 2 – медный концентрат, который перерабатывается на Жезказганском медеплавильном заводе.
Жезказганские обогатительные фабрики № 1, 2 выпускают медный концентрат в соответствии со стандартом СТ 2330-2013 «Концентрат медный. Технические условия».
— Каковы особенности технологической цепочки переработки сульфидных руд?
— Технологическая схема фабрики включает несколько этапов. Первый — прием в зданиях вагоноопрокида руды, поступающей с рудников в железнодорожных вагонах. Второй — стадиальное дробление руды (крупное, среднее и мелкое) в корпусах дробления. Используются конусные дробилки: разрушение руды происходит за счет раздавливания кусков между подвижным и неподвижным конусами.
Третий этап — измельчение руды в барабанных мельницах с получением пульпы и последующим направлением ее на флотацию. Мелющей средой в таких мельницах являются стальные стержни и чугунные или стальные шары разного диаметра.
Четвертая стадия — флотация. Тонко измельченные частицы медных минералов закрепляются на поверхности пузырьков воздуха в водной среде с добавлением специальных химических реагентов. Всплывшие пузырьки с медными минералами образуют пену, которая направляется на следующие стадии флотации, пока не превратится в готовый медный концентрат. Не прикрепившиеся к пузырькам и утонувшие частицы пустой породы называются хвостами обогащения. После флотации хвосты обогащения по трубопроводам направляются на хвостохранилище.
Пятый этап переработки — сгущение и фильтрация медного концентрата. На этой стадии снижается содержание влаги в полученном при флотации концентрате.
— В чем заключается отличие технологии переработки сульфидных руд по сравнению с другими аналогичными производствами?
— Главная особенность — наличие схемы раздельной схемы флотации песков и шламов, что обусловлено генетическим и минеральным составом руды Жезказганского месторождения.
Второе отличие — внедряемая в настоящий момент схема обогащения окисленных и смешанных руд на секциях № 5–6 Главного корпуса № 1. Она включает в себя сульфидную и окисленную флотацию, что позволяет перерабатывать руды карьерной добычи с получением высоких технологических показателей. Разработчик — компания ТОО «КазГидроМедь».
Фактические показатели работы ЖОФ № 1, 2 приведены в таблице 1.
— Какие условия применяются на фабриках при отборе и подготовке проб?
— Отбор и подготовка пробы производится в соответствии с ГОСТ 13170-80 «Руды и концентраты цветных металлов. Метод определения содержания влаги», ГОСТ 14180-80 «Руды и концентраты цветных металлов. Методы отбора для химического анализа и определения влаги».
Отобранные пробы проходят определенные стадии подготовки проб к рентгеноспектральному анализу (таблица 2).
Для предотвращения влияния на качество материала одних проб на другие после обработки проб каждого рудоспуска в процессе дробления оборудование должно быть очищено щеткой или сжатым воздухом.
Проба руды для определения массовой доли влаги массой 1 кг высыпается на противень и помещается в предварительно нагретый до температуры 105–110 °С сушильный шкаф на два часа, с этикеткой с надписью наименования пробы, времени отбора и веса поддона. По истечении двух часов высушивания противень с пробой вынимается из сушильного шкафа, взвешивается, перемешивается, и продолжается высушивание до постоянной, если разность результатов двух последующих взвешиваний не превышает 0,05 % от массы анализируемой пробы. Если при последующем взвешивании произойдет увеличение навески более чем на 0,05 %, то за окончательный результат принимают массу, предшествующую увеличению.
Массовая доля влаги в процентах вычисляется по формуле:
M1 – М2
W = М1 — М3 Ч 100 %,
где М1 — масса противня с навеской до высушивания, г;
М2 — масса противня с навеской после высушивания, г;
М3 — масса высушенного противня, г.
В журнале регистрации влаги делается запись: дата, время отбора пробы, вес навески с противнем, время первого взвешивания, время и результаты последующих взвешиваний до постоянной массы.
— Какое оборудование используется в лаборатории технологических исследований Жезказганских ОФ?
— Спектр оборудования достаточно широк. Это дробилка щековая лабораторная ДЩЛ 150Ч80 — небольшой компактный механизм, предназначенный для среднего дробления кусков руды и других пород максимальной крупности 80 мм в лабораторных и полевых условиях.
Рабочим органом щековой дробилки являются подвижная и неподвижная щеки. Качание подвижной щеки осуществляется при помощи эксцентрикового вала и нижней опоры шатуна. Процесс дробления материала происходит в дробилке периодически по принципу раздавливания и истирания. Дробилка монтируется на металлической или деревянной раме или на массивном деревянном столе с закреплением на них болтами.
Также применяется лабораторная флотационная машина 135 Д-Фл марки «Механобр» с объемом камеры 3 л для флотационных испытаний. Ее используют для флотации руды 1,0–1,5 кг.
Флотационная машина обеспечивает подобие процесса флотомашин, протекающего в промышленных машинах, и единообразие в проведении опытов. Имеется возможность поступления большого количества воздуха и созданы условия подобия потоков пульпы в камере.
Флотомашина состоит из следующих узлов: блока импеллера, камеры, подставки, пеногона, электродвигателя, затвора, дросселирующего крана, воронки, защитного кожуха. Машина устанавливается на отдельной подставке или столе, на котором должны быть отверстия для закрепления машины болтами, а также квадратное отверстие для воронки. Должен быть подступ ко всем узлам флотомашины. К месту установки подводится трехфазный переменный ток напряжением 220/300 В.
В лаборатории установлен истиратель вибрационный ИДА-175, предназначенный для механического измельчения навесок руд и других сухих материалов перед их химическим анализом, также для иных целей при необходимости получения измельченного продукта.
Измельчитель вибрационный состоит из основания, корпуса, подвески, которая при помощи резиновых амортизаторов (не менее пяти штук) подвешивается на цапфах корпуса. В средней части подвески находится инерционный вибратор. Вал вибратора имеет две шарико-подшипниковых опоры и приводится во вращение электродвигателем через клинноременную передачу. В средней части вала укреплен дебаланс, который при вращении вызывает появление инерционных сил, сообщающих подвеске измельчителя вибрационное движение по круговой траектории.
В гнезда подвески устанавливаются четыре стакана, внутри которых находятся ролики. Стаканы закрываются крышками при помощи прихватов с гайками. Ролики под действием вибрационного движения подвески обкатываются по внутренним поверхностям стаканов и производят измельчение загруженного в стаканы материала путем его раздавливания и истирания.
Обезвоживание пульповых проб осуществляется с помощью обезвоживателя ОП-3 (лабораторного фильтр-пресса). Он состоит из стакана, на основание которого накладывается фильтрующий элемент (бумага фильтровальная), прижимающей крышки, рукоятки. Для подачи сжатого воздуха предназначен штуцер, установленный сбоку. Фильтр-пресс работает в повторно-кратковременном режиме.
Для рассева проб зернистого материала сухим способом применяется анализатор ситовой СЛВ 200-11 (ротап). Аппарат состоит из чугунного корпуса, внутри которого расположен приводной механизм, чугунной плиты, на которой смонтированы стойки и весь подвижный механизм с набором сит. На подвижной площадке установлен поддон, набор сит, крышка и тарелка с резиновой прокладкой, удерживаемые откидной скобой. Подвижная площадка вместе с набором сит крепится на штоках двумя болтами. Набор сит совершает колебательное движение вместе с шатунами. Аппарат снабжен кулачковым механизмом, обеспечивающим очистку сит от трудных зерен путем ритмичных ударов молотка по набору сит.
Также в лаборатории работают лабораторные шаровые мельницы объемом 7 л и 1 л, которые измельчают руду, концентраты и промпродукты в водной среде. Для измельчения руды применяется шаровая мельница объемом 7 л. Навеска руды в этом случае берется 1,0–1,5 кг.
Для измельчения концентратов и промпродуктов используется шаровая мельница объемом 1 л с навеской 100–250 г.
Дробящая среда – шары диаметром 20 мм для руд крупностью 25–18 мм в количестве 6 кг на 1 кг руды; для доизмельчения промпродуктов и концентратов — шары диаметром 10 мм для продуктов крупностью 10–12 мм в количестве 2 кг.
Количество воды в мельнице по объему должно быть равно объему руды. Для Жезказганской сульфидной руды объем воды для навески 1 кг равен 0,5 л. В мельницу сначала загружают шары, наливают воду и только потом загружают руду и реагенты. Мельницы смонтированы на отдельных подставках и имеют оборотное устройство для наклона при разгрузке.
Рассев проб зернистого материала выполняется на лабораторном грохоте. Он состоит из просеивающего короба, пружины, вала со шкивом, двигателя со шкивом, арматурной стойки (4 шт.), поддона.
Удаление влаги из технологических проб происходит в сушильном шкафу (печи для сушки проб). Печь оснащена электронагревательным элементом, работающим от сети 380 В. Температура печи для сушки технологических проб может поддерживаться в пределах 100–105 °С.
Процесс флотации, протекающий в современных промышленных флотомашинах, имитируется в лаборатории в лабораторных флотомашинах объемом 1,0 л (136 В-Фл) и 0,5 л (137 В-Фл). Они обеспечивают однообразие проведение опытов и точную повторимость каждого опыта.
Флотомашины состоят из следующих основных узлов: камеры, блока импеллера, пеногона, станины и привода пеногона. На станине смонтированы все узлы машины. Камера съемная, изготовлена из оргстекла, закрепляется на станине при помощи натяжного винта и рукоятки. В блоке импеллера объединены в один монтажный узел приводной вал с корпусом подшипников, импеллер, статор и воздухопровод.
Привод пеногона осуществляется от электродвигателя Д-222; на валу электродвигателя насажен шкив, посредством круглого резинового ремня передается вращательное движение на пеногон.
Пеногон имеет кривошип с шарнирно-закрепленной лопаткой. Установка пеногона по высоте может быть изменена при помощи рукоятки, фиксирующей положение кронштейна. К станине прикреплен столик, на котором устанавливается стакан для концентрата.
Флотомашины 136 В-Фл и 137 В-Фл не требуют крепления и устанавливаются на обычном столе. К месту установки подводится электрический ток с переменным напряжением 220/380 В.
Дробление проб руды от 10 до 3 мм производится на валковой лабораторной дробилке с временным сопротивлением до 1 500 кг/см3.
Рабочим органом валковой дробилки являются два валка размером 200Ч75 мм. Процесс дробления материала происходит в дробилке периодически по принципу раздавливания и истирания. Валки вращаются навстречу друг другу и приводятся в движение при помощи электроодвигателя 4,5 кВт, установленного для каждого из валков и соединяющегося с ними при помощи ремней и шкивов.
Дробилка монтируется на металлической раме с закреплением на ней болтами. Рабочие органы дробилки закрыты специальным кожухом, а ремни и шкивы сетчатым ограждением.
Вал с валком крепится в подшипниковом узле. Один валок является неподвижным и удерживается в стационарном положении при помощи прижимного устройства. Второй валок для регулирования щели может перемещаться по салазкам в станине. Специальным ключом вращаем втулку, она передвигает внутри себя болт и происходит перемещение валка.
Привод дробилки состоит из электродвигателя и плоскоременной передачи. Валки, вращаясь навстречу друг другу, захватывают дробильный материал, который поступает сверху из загрузочного бункера. Размеры кусков продукта дробления можно регулировать, изменяя ширину щели между валками.
— Внедрены ли на фабриках системы автоматического управления технологическим процессом? Какие результаты это дает?
— Системы автоматического управления технологическими процессами необходимы для контроля и управления технологическими параметрами оборудования. Внедрение данных систем позволяет более эффективно управлять производством и получать высококачественную продукцию. В последнее время на ЖОФ № 1, 2 были проведены следующие работы:
1) установка системы автоматического дозирования реагентов компании Watson Marlou насосов дозатора на 1–2-й секции Главного корпуса № 1 и на 8-й секции Главного корпуса № 2;
2) установка плотномера и расходомера на магистрали концентратных насосов Главного корпуса № 2;
3) установка автоматизированной системы «Руда — вода» на 2-й секции Главного корпуса № 2 (на мельнице МСЦ 3,2Ч4,5);
4) установка автоматизированной системы поддержания уровня пульпы в зумпфах 1–6-й секции Главного корпуса № 2;
5) установка автоматизированной системы поддержания уровня пульпы в зумпфах измельчения 9-й секции Главного корпуса № 2.
Поскольку ЖОФ № 1, 2 эксплуатируются давно, замена морально и физически устаревшего оборудования на предприятии носит постоянный характер. В последние годы была произведена замена следующего оборудования:
1) замена флотомашин «Механобр-7» на флотомашины МЕК-25 в цикле шламовой флотации ГК-1 ЖОФ № 1, 2, 3 по проекту «Модернизация шламовой флотации в ГК-1 ЖОФ № 1, 2, 3»;
2) внедрение флотомашин РИФ-25, МФКПМ-25, ТК-20 на 7-й секции ГК-2 ЖОФ № 1, 2, 3;
3) внедрение флотомашин «Усольмаш» в цикле песковой флотации ГК № 1, 2 ЖОФ № 1, 2, 3;
4) замена вагоноопрокида ВРС в КД-2;
5) установка РКС (рудоконтролирующей станции) на оборудованиях (тяжелых конвейерах в КД-1, КД-2 с целью определения содержания меди поступающей руды на ЖОФ.
— Какие природоохранные мероприятия проводятся на обогатительных фабриках?
— На ЖОФ № 1, 2 внедрены системы очистки отходящего воздуха из цехов от пыли и других загрязнений. Водоснабжение фабрик организовано путем применения оборотной воды, получаемой с хвостохранилища, что исключает потребность в воде из Кенгирского водохранилища. На старом хвостохранилище, эксплуатировавшемся до 2008 года, а ныне находящемся на консервации, применяются самые современные методы по исключению пыления высохших хвостов обогащения.