Канат Алдабаев, фото Геннадия Дробца
Второй год в компании «Богатырь Комир» успешно функционирует Автоматизированная система диспетчерского управления открытыми горными работами. За это время АСДУ на практике доказала свою эффективность.
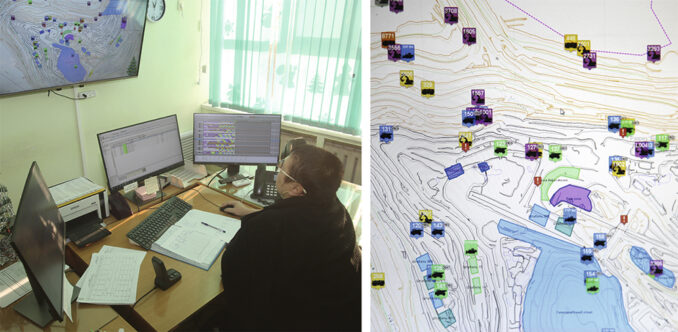
Программа представляет собой автоматизированную систему сбора, централизованного хранения и обработки данных о технологическом процессе. Комплекс включает в себя датчики и бортовое оборудование, соединенное через GPS и интернет-связь с единой информационно-аналитической системой управления, для передачи данных, которые отображаются на экранах у начальников участков, горного диспетчера, диспетчера УТТ, начальника производственной службы, руководителей компании и других пользователей системы АСДУ.
Уже в самом начале подготовки проекта АСДУ Дирекцией по развитию производственной системы была поставлена задача перед разработчиками представить расширенную версию программы, показывающую все этапы производственного цикла: планирование, контроль, анализ с возможностью внесения корректировок с учетом местных горно-геологических особенностей, а также технологии формирования качества угля на штабелях. Принимались в расчет и масштабы территории двух разрезов — «Богатырь» и «Северный», огромное количество задействованной техники: бульдозеров, самосвалов, экскаваторов, разветвленная сеть технологических дорог.
Фактор времени
Логика действия программы АСДУ выстроена таким образом, что для планирования объема горной массы, которую предстоит извлечь и перевезти за смену, требуется знать, как отработает горнотранспортное оборудование. Исходя из этого, программой предусмотрено планирование времени работы горной техники и оборудования с учетом всех возможных остановок. Например, в случае с экскаватором — простои, которые вызваны перегоном машины, работой тракторно-бульдозерной техники при планировке забоев и т. д. У самосвалов это часы технического обслуживания, текущие и аварийные ремонты. В автоматическом режиме вносятся в программу простои, связанные с перерывом на обед, приемкой-сдачей смены.
Обработав внесенные сведения, система выдает планируемое время работы на каждую единицу техники. И уже, располагая нормативом времени, АСДУ рассчитывает объем горной массы, которую экскаватор должен загрузить, а самосвал перевезти за смену.
Каждому — по возможностям
Следующим этапом работы АСДУ является распределение объёмов горной массы между вышедшей на линию техникой. Программа автоматически просчитывает ожидаемую производительность каждой горной машины, а также расстояние от конкретного экскаватора, задействованного на погрузке, до места разгрузки самосвалов, что важно, так как позволяет определить время и количество рейсов, запланированных на смену.
Следует отметить, при расчете горной массы для каждого экскаватора на смену берутся за основу среднестатистические данные — медианные значения (как более точные и корректные): к примеру, 100 последних погрузок, выполненных этим экскаватором. Аналогично рассчитывается количество и время рейсов самосвалов по определенному маршруту.
На основе собранных данных производится расчет наряда, где указана сменная норма производительности отдельного экскаватора, расстояние откатки и время рейса самосвала.
Важно, что АСДУ позволила исключить неоправданные простои экскаваторов и самосвалов. Достигнуть этого удалось за счет того, что в систему были включены плановые значения времени ожидания. Благодаря такому планированию удается определить и устранить причины простоев в каждом конкретном случае.
За работу!
Сформированный системой сменный наряд направляется в виде сообщения на борт самосвала, в нем подробно указывается, на каком маршруте предстоит работать данной машине в начале смены. На экране работамера, установленного в кабине самосвала, отображается, под погрузку какого конкретного экскаватора он должен направиться. В течение смены ситуация может поменяться, и произойдет перераспределение машин на другие маршруты.
Текущая ситуация на разрезе в режиме реального времени контролируется горным диспетчером, который координирует и по необходимости корректирует процессы, наблюдая на экране временные дорожки экскаватора и самосвала, количество погрузок и рейсов. Он видит скорость самосвалов, уклоны дорог, напряженность потоков и другие факторы, влияющие на технологический процесс. Ранее же вся эта информация передавалась по радиосвязи и вносилась специалистами вручную, имелись погрешности в данных.
Кроме того, с помощью данных, отображающихся в окне экрана, диспетчер влияет на формирование качества угля. Ориентируясь на сведения системы, фиксирующей количество и зольность угля, формируемого в штабелях, он направляет сообщение на борт самосвала о том, по какому маршруту и под погрузку какого экскаватора машине следует направиться.
Установленные на каждом экскаваторе и самосвале датчики (трекер на движение, датчик на тахометре, фиксирующий, заведен двигатель или нет, датчики на подвесках и шинах, и др.) позволяют контролировать весь производственный цикл в режиме реального времени. Они дают возможность фиксировать факт погрузки и разгрузки, обеспечивая тем самым достоверность собранных сведений.
В систему заложена такая логика: сопоставляя данные с датчиков, она автоматически сообщает о наступлении того или иного события. Например, самосвал стоит на месте и сработал датчик давления — значит, он произвел разгрузку, а если же машина находится в зоне экскаватора и у нее изменилось давление в подвесках — началась погрузка.
Достоинством АСДУ является то, что она дает объективную и прозрачную оценку труда каждого работника, задействованного в автотехнологии. Заступающему на смену машинисту экскаватора и водителю самосвала выдается прокси-карта, которая позволяет идентифицировать их в системе, для того чтобы отслеживать производительность труда каждого. Таким образом, благодаря внедрению АСДУ производительность труда стала одним из главных критериев при оценке действий и вклада сотрудника в результаты работы наряду с другими факторами — техническим состоянием и работой оборудования, погодными условиями.
Машина времени
Данные АСДУ позволяют в режиме реального времени контролировать ключевые производственные показатели — план, факт, ожидания выполнения на текущий момент при определенном темпе работы, а также вносить коррективы в течение смены.
Анализ причин невыполнения плановых показателей, особенно если они приобретают системный характер, от смены к смене, на основе формируемых системой отчетов выполняет производственная служба, предлагая затем решения для устранения этих причин.
Сервер АСДУ, хранящий все поступающие сведения, образно можно сравнить с машиной времени, позволяющей перемотать пленку записи назад — на дни, недели и даже месяцы для проверки и установления хронологии и обстоятельств того или иного события.
Использовать на максимум
Базовый принцип АСДУ: «Если есть оборудование, оно должно работать». Следуя этой логике, главным элементом при формировании системой отчета стало время. При этом под работой понимается период, когда горнотранспортное оборудование фактически задействовано на погрузке и перевозке горной массы, без учета простоев. В свою очередь простои поделены на технологические и организационные.
Расчет всего рабочего времени производится с учетом двух величин — коэффициента технической готовности и коэффициента использования оборудования, что позволило установить четкие границы ответственности подразделений, а в конечном итоге свести до минимума необязательные простои. Такой подход увеличил коэффициент использования горнотранспортной техники, в частности повысил эффективность самосвалов и принес экономию на три самосвала в годовом исчислении.
В целом система АСДУ дает полную и объективную картину состояния горного производства и открывает пути решения проблем.