Беседовала Наталья Демшина
«Полюс» является лидером среди производителей золота в России и входит в пятерку ведущих золотодобывающих компаний в мире, с самой низкой себестоимостью. Производственные активы компании расположены в Сибири и на Дальнем Востоке.
«Полюс Вернинское» входит в состав «Полюса» и является одним из самых молодых предприятий компании. На Вернинском ГОКе успешно реализовано множество проектов по автоматизации и совершенствованию технологических процессов. Именно поэтому Вернинская золотоизвлекательная фабрика демонстрирует коэффициент извлечения золота из руды 90 % — самый высокий среди предприятий «Полюса».
О том, какие современные технологии применяются на производстве, и реализованных технических решениях в интервью нашему изданию рассказал главный технолог «Полюс Вернинского» Андрей Алейников.
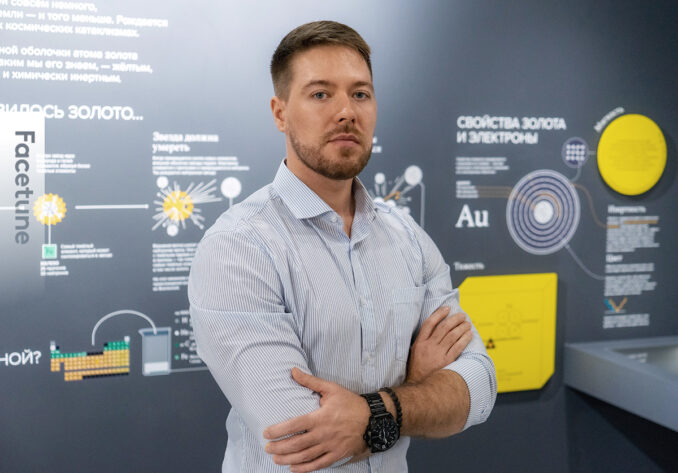
— Андрей Александрович, как вы оказались в команде «Полюса»?
— Практически сразу после окончания Сибирского федерального университета по специальности «Инженер-металлург» устроился на Вернинскую ЗИФ аппаратчиком-гидрометаллургом. После первой вахты возвращался домой уже инженером-технологом ЗИФ. На тот момент фабрика работала второй год, именно здесь я получил производственный опыт. Меня интересовала вся производственная схема, причем не только этой фабрики, но других ЗИФ «Полюса». Еще через год я стал начальником отдела. Моя роль заключалась в руководстве командой, занимающейся совершенствованием технологии и повышением уровня автоматизации в процессе добычи золота. Наша основная задача — снизить затраты. Спустя четыре года я стал главным технологом компании.
С этого момента кругозор и уровень ответственности начал стремительно расширяться. Помимо привычного развития производства большую часть времени занимался долгосрочными стратегическими вопросами. В «Полюс Вернинском» работаю уже 10 лет. И сейчас заинтересован в выполнении задач далеко за рамками своей компетенции: осваиваю горное дело.
За это время у нас сформировалась сильная команда специалистов, которые берутся за решение самых амбициозных задач.
— Что отличает «Полюс Вернинское» от других золотодобывающих компаний?
— Для меня «Полюс Вернинское» является флагманом по добыче рудного золота в Бодайбинском районе и всей Иркутской области, а Вернинский ГОК по праву считается одним из самых технически совершенных предприятий золотодобывающей отрасли России. Кроме того, это компания с самым высоким извлечением золота в Иркутской области и одним из самых высоких в России среди предприятий с открытой добычей.
Особенности технических решений «Полюса Вернинское»
— Расскажите о реализованных технических решениях. В чем их особенности?
— Начиналось все в 2015 году с решения текущих проблем на технологических участках. Несмотря на то что ЗИФ относительно молодая, пришлось локально дооснащать отдельные участки приборами контроля и автоматизации. Были участки, где автоматизации не было совсем. Например, на участке, где золото получают из активированного угля (участок десорбции). Я считаю, если нет автоматизации, то процесс неконтролируем, сложно отследить, что происходит, и выявить причины отклонений. А если на участке меняется персонал, то проблемы неизбежны. Поэтому с коллегами-автоматчиками разработали специальное программное обеспечение, которое увязывало более 50 единиц оборудования и приборов. Со временем программное обеспечение появилось на всех технологических участках.
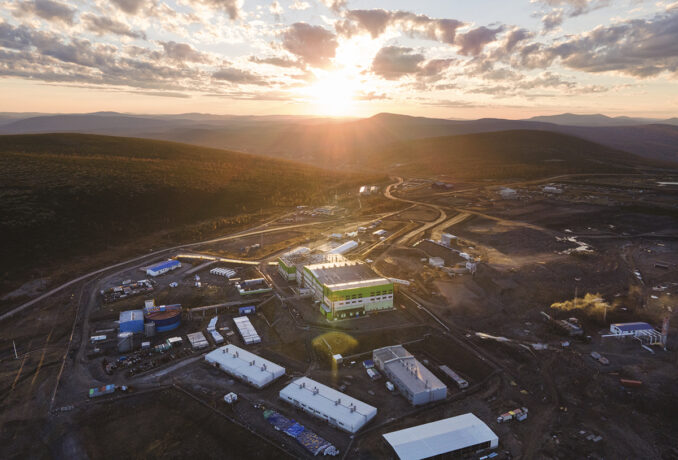
В 2020 году с командой сфокусировались на новых и более сложных технологиях. Например, для повышения эффективности измельчения увязали работу приборов MillSlicer и RockSense.
RockSense — это специальная камера, которая отслеживает крупность руды, подаваемой в ММПС.
MillSlicer — это датчики вибродиагностики мельниц. Прибор дает полную картину происходящего в мельнице (загруженность мельницы, повреждение футеровки, угол падения шаров и т. д.).
Показатели этих приборов в совокупности с грамотным подходом к автоматизации позволили в дальнейшем управлять крупностью питания, добиваясь более стабильного измельчения на первой стадии.
Далее по технологии улучшения коснулись участка флотации. Были установлены специальные камеры контроля состояния пены (технология FrothSense). Программное обеспечение решили разработать самостоятельно. Нельзя сказать, что это было легко — процесс очень зависит от большого количества факторов, которые необходимо было учесть и связать в единую логику управления. Но результат превзошел все ожидания.
После осознания достигнутых результатов хотелось повысить уровень автоматизации на всей фабрике, чтобы это работало как единое целое, сделать то, что в России еще никто не делал. Триггером проекта стало увеличение мощности ЗИФ: в 2021 году в эксплуатацию был запущен дополнительный цех измельчения. Количество оборудования как фабрики, так и ДСК значительно увеличилось. Появилась идея, которая на тот момент казалась безумной: сделать возможным запуск всей ЗИФ с одной кнопки, как технологии start/stop в автомобилях. Поэтому начали увязывать все ранее реализованные улучшения между собой, дооснащать приборами КИП, системами блокировок. Разумеется, к результату пришли не сразу — для реализации такого рода проекта уровень оснащения ЗИФ должен быть максимальным. На разработку программного обеспечения и получение желаемого результата ушло 3 месяца. В итоге время запуска фабрики сократилось в 2 раза. Мы начали не только внедрять новые технологии и практики на производстве, но и создавать их.
В 2021 году шагнули в сторону верхнеуровневой автоматизации, создав Систему усовершенствованного управления технологическими процессами (СУУТП). Это комплексное решение прогнозируемого управления технологическим процессом и его быстрым вводом на заданный режим. Внедрение СУУТП позволило нам оптимизировать процессы и контролировать их более эффективно. В 2023 году мы также разработали и запустили собственную программу по движению сорбента в цикле сорбции, полностью автоматизировав этот процесс и исключив человеческий фактор.
За последние семь лет работы компании ее производительность увеличилась более чем на 70 %.
— Как внешнеполитическая обстановка повлияла на производственную деятельность, каким образом решались проблемы санкционных ограничений?
— 2022-й был для нас годом большого количества промышленных испытаний. Если говорить о реагентах, то порядка 20 % номенклатуры попали под санкционные ограничения. Однако уже спустя 3 месяца после ввода ограничений мы совместно с Исследовательским центром «Полюса» в Красноярске подобрали аналоги. Сегодня полностью перешли на реагенты, произведенные в России.
Что касается изнашиваемых материалов и запасных частей, то практически все они не поставляются в Россию. Проблему решали вместе с другими бизнес-единицами компании, обменивались опытом. На сегодняшний день большая часть проблем решена — рынок горно-обогатительного оборудования развивается на глазах. Помимо аналогов запчастей появляются полные российские аналоги зарубежного оборудования. Сейчас работа направлена на поиск более качественных материалов внутри России. В этом вижу преимущества: сокращаются и сроки поставки, и операционные затраты за счет развития конкуренции на рынке.
— Сейчас фабрика автоматизирована почти на 100 %. Каким еще участкам нужна модернизация? Что еще на ней можно совершенствовать?
— Если говорить об основных производственных процессах, то все они проводятся в автоматическом режиме. Текущие улучшения имеют локальный характер и сосредоточены на эффективном управлении технологией, повышении качества процессов за счет оптимизации циклов или перераспределения материальных потоков. В этой части высокий уровень автоматизации позволяет легко менять какие-либо параметры, искать способы по улучшению технологии.
Есть отдельные ручные операции, которые требуют человеческого внимания и которые еще подвергаются автоматизации (например, транспортировка проб путем организации пневмопочты, замена сорбента в угольных колоннах и т. д.). Но при этом обслуживать и проводить ремонт оборудования все равно должен опытный работник.
— Все ли процессы, на ваш взгляд, можно будет доверить роботам и искусственному интеллекту?
— Рано или поздно, думаю, это произойдет — это лишь вопрос времени. Одним из векторов развития «Полюса» является цифровая трансформация. В рамках функциональной стратегии производственного блока одной из инициатив является внедрение интеллектуальных цифровых советчиков. Отчасти это и представляет собой искусственный интеллект в производстве, который непрерывно собирает, структурирует и обрабатывает данные с технологического оборудования.
— Какими личными качествами и навыками должен обладать горняк, металлург?
— На мой взгляд, самое основное — это интерес к постоянному развитию. Компания очень динамично развивается, меняется производство, подходы. Необходимо видеть способы улучшения производства и увеличения производственных показателей.
Второе — это оперативность. Успешный производственник — это тот, кто умеет быстро реагировать, очень оперативно решать проблемы с помощью имеющихся ресурсов. Порой такие решения не самые стандартные. Цена таких решений очень высока, когда речь идет об аварийной остановке.
Третье — дальновидность и стратегическое видение, гибкость и умение просчитывать ситуацию на несколько шагов вперед.
Четвертое — коммуникативные навыки. Очень часто необходимо заинтересовать и привлечь к решению проблемы смежные службы.
Что касается навыков, есть прекрасная книга Ицхака Адизеса о том, каким набором функций и в каком соотношении должен обладать хороший специалист. В производстве точно так же: металлург или технолог должен быть силен во всех четырех ролях (производитель, администратор, предприниматель и интегратор), одно без другого будет иметь малую эффективность.
Развитие и мотивация в компании Вернинского ГОКа
— У вас богатый опыт. Поделитесь, как компания развивает и мотивирует своих специалистов?
— «Полюс» крайне заинтересован в развитии своих сотрудников. За 10 лет работы в компании я стал участником множества различных программ, семинаров, тренингов, позволяющих наработать нужные для руководителя качества, побывал в зарубежных командировках, изучая передовой опыт.
Каждый год компания старается привнести что-то новое с точки зрения развития специалистов. В этом году фокус сместился на обмен опытом внутри «Полюса». Открыт проект «Ротация» — один руководитель временно замещает другого руководителя, стоящего выше по структуре, но в другой бизнес-единице.
Также в этом году проводятся модули по направлениям «Горные работы», «Обогащение» и «Управление производственными активами». Цель программы — поиск и развитие кадрового резерва рудных бизнес-единиц компании. Встречи проводятся на каждом из активов, где коллеги делятся друг с другом опытом, проблемами и достижениями.
Моя мотивация заключается в успешной реализации проектов и достижении поставленных целей. Наблюдать за результатами работы или видеть, как проект, который начинался лишь как идея, становится реальностью, — это особое удовольствие. Хочу отдельно отметить, что в «Полюс Вернинском» помогают правильно расставить приоритеты, вдохновляют на успех и новые достижения управляющий директор Игорь Цукуров и главный операционный директор Николай Ковалев.
Я глубоко убежден, что развитию нет предела. Успех возможен только в команде. Как руководитель я прилагаю максимум усилий для развития своей команды, повышения компетенций сотрудников. Стараюсь делиться опытом и показывать, к чему нужно стремиться. Наблюдать за прогрессом и результатами своих «учеников» — это еще одна большая награда для меня.