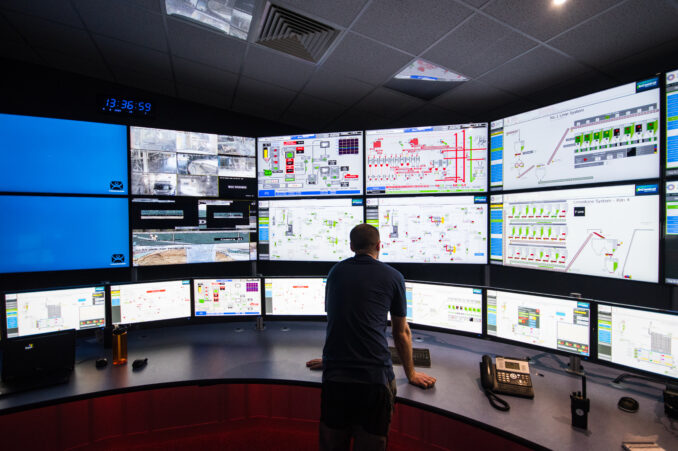
Как компания Singleton Birch создала единый центр управления, увеличила работоспособность оборудования на 20% и сократила операционные издержки на 13%
Бизнес должен уметь адаптироваться под происходящие изменения. Ведь на плаву остаются только те компании, которые обладают достаточной гибкостью.
Идеальным примером готовности к изменениям является компания Singleton Birch, которая занимается кальцинированием известняка. После образования в 1815 г. компания пережила множество индустриальных эпох и продолжает преуспевать. Отчасти это обусловлено уникальной структурой компании. Управление компанией осуществляет попечительский совет, состоящий из нескольких благотворительных обществ вместе с потомками первоначальных владельцев. Компания нацелена на реинвестирование капитала в свою организацию, чтобы поддерживать инициативы по непрерывному совершенствованию и модернизации. Благодаря такому гибкому подходу компания, расположенная в графстве Линкольншир в Великобритании, способна поставлять свои продукты и услуги более чем 300 заказчикам в энергетике, коммунальном хозяйстве и металлургии.
Управление
Центральным компонентом сложной системы снабжения являются функции управления. Они отвечают за контроль всех этапов, начиная от добычи карбоната кальция (известняка), до доставки продукции и утилизации отходов на удаленных объектах заказчика. Изначально управление осуществлялось из восьми отдельных центров управления, расположенных рядом с производственными площадками, в каждом из которых работал собственный эксплуатационный и технический персонал. В них было установлено около 40 устаревших ПЛК и 25 SCADA-систем, поддержка которых осуществлялась с отдельных удаленных серверов.
При таком подходе компания сталкивалась с некоторыми ограничениями. Управление производственной деятельностью было разобщено, а работа на отдельных ее участках, таких как карьеры, печи и производственные установки, была практически не скоординирована. Из-за этого возникали проблемы с распределением ресурсов, а также угрозы безопасности из-за недостаточного обмена информацией между объектами. Такой подход был также очень затратным, поскольку существовала необходимость одновременно эксплуатировать несколько разных объектов со своим персоналом. Кроме того, существовал риск простоев оборудования из-за недостаточного резервирования информационной инфраструктуры компании. Простой одного из центров управления мог представлять большую проблему, поскольку он мог бездействовать в течение нескольких часов, а возможно и дней, на все время проведения ремонтных работ.
В 2015 году компания начала процесс консолидации и интеграции своей управленческой деятельности, которая требовала серьезных усовершенствований. Целью данной инициативы была замена нескольких разрозненных объектов на единый центр управления, обладающий возможностью полного контроля всей производственной деятельности компании. В сотрудничестве с системным интегратором InControl Systems совет увидел в проекте хорошую возможность для экономии и конкурентное преимущество. Вслед за пилотным проектом 2017 года совет согласовал разработку интегрированного центра управления, работающего при поддержке нового локального центра обработки и хранения данных.
Концепция проекта также была согласована с обширной организационной кампанией по изменению культуры компании и интеграции ее производственных цепочек. Она означала отказ от использования универсального персонала, управляющего разными частями компании, в пользу полностью интегрированного управления производственной деятельностью профильными специалистами. Новый центр управления должен был стать современным технологичным объектом, ответственность которого простирается от распределения и оптимизации ресурсов до обеспечения безопасности и логистики. Перед центром стояли две основные цели: снижение затрат и повышение добавленной стоимости.Чтобы воплотить концепцию в реальность, InControl Systems помогли подобрать компании, предоставляющие передовые технологии, в том числе Rockwell Automation, PTC и InVMA.
Трансформация из центра
Установка началась в мае 2019 года, и на создание центра управления потребовалось восемь недель. В ходе работ было установлено более 40 больших экранов, резервированные серверы и вспомогательные приложения, подключенные к ПЛК через шлюзы логической схемы управления по сети Ethernet. Эти экраны обеспечивают операторам возможность отслеживать параметры производственной деятельности под одной учетной записью и требуют минимального технического обслуживания.
Для поддержки новых возможностей центра управления компания Singleton Birch создала связанный с ним центр обработки и хранения данных для усиления резервирования и улучшения качества данных. В этом центре установлено два клиент-сервера Rockwell Automation FactoryTalk View SE с неограниченным резервированием, один для добычи, а второй для обогащения, что помогает в значительной степени сократить простои. Также была реализована резервированная конфигурация ThinManager для облегчения управления таким большим количеством экранов и упрощения их технического обслуживания. И наконец, было установлено ПО FactoryTalk AssetCentre, которое обеспечивает проведение полного аудита и упрощает отслеживание изменений, вносимых в программное обеспечение.
В состав центра обработки и хранения данных также были включены решения PTC ThingWorx и Kepware, которые позволяют операторам объединять данные из множества источников, включая системы управления, системы контроля расхода электроэнергии, корпоративные системы и системы планирования. Это дало операторам полный доступ к информации о запасах и производственным данным, чтобы они могли точнее прогнозировать производство и отгрузки.
К августу 2019 года новая система уже была полностью работоспособна. Быстрому осуществлению проекта способствовала гибкость и масштабируемость платформы ThingWorx. С помощью новоприобретенных возможностей операторы получили более четкое представление о производительности оборудования, его обслуживании и доступ к финансовой информации. Интегрированная система сблизила операторов и инженеров в том смысле, что дала возможность согласовывать техническое обслуживание с потребностями производства. Система также функционально отделила операторов системы управления от руководителей на местах. Операторы системы управления должны были выступать в роли «глаз и ушей» руководителей, анализируя данные и предоставляя рекомендации сотрудникам на местах.
Интегрированная работа
С тех пор как центр управления был введен в эксплуатацию, новые возможности стали важной частью производственной деятельности Singleton Birch. На техническом уровне деятельность центра была хорошо согласована со стратегическими замыслами совета. Среди основных преимуществ можно выделить следующие:
- Повышение работоспособности оборудования
Работоспособность оборудования увеличилась более чем на 20 % благодаря росту производительности систем и значительному снижению количества и степени воздействия системных сбоев.
- Снижение потребления электроэнергии
Система выполняет учет расхода электроэнергии на базовых уровнях электроснабжения, благодаря чему у операторов появляется детальное понимание обстановки и возможность лучше управлять процессом производства и расходом электроэнергии по всему предприятию.
- Снижение расходов и повышение гибкости
Операционные расходы сократились примерно на 13 % с учетом конкурентоспособной цены решения и снижения количества оперативного персонала.
- Повышение безопасности
Руководители теперь располагаются на удалении от непосредственного места проведения работ, а это означает, что они способны раньше обнаруживать проблемы и пользоваться помощью инженеров для превентивного технического обслуживания.
- Улучшение управления и интеграции
Создание единого центра управления способствовало достижению основной цели проекта, которая заключалась в улучшении контроля и возможности принимать решения для всего предприятия в целом.
- Продажи и выручка
Новая система позволила Singleton Birch улучшить управление различными аспектами системы снабжения при помощи усовершенствованной логистики. Такой подход помог дифференцировать бизнес-модель компании и значительно повысить ее конкурентоспособность.
- Культурные улучшения
Персонал, занятый в управлении производственной деятельностью, принимал участие в проекте с самого начала. Теперь они работают в более удобной среде и на более качественном оборудовании. Также они оценили новый подход к принятию эффективных решений, позволяющий в режиме реального времени реагировать на возникающие ситуации.
Перспективы на двести лет вперед
Проект создания интегрированного центра управления помог компании не только эффективнее и экономичнее управлять предприятием, но и создать культурные преимущества, которые, как она ожидает, преобразуются в большую вовлеченность персонала и его карьерный рост. Такое преобразование стало возможным благодаря поддержке ее партнеров, в том числе Rockwell Automation. Придерживаясь своих корней и вместе с тем демонстрируя решимость в проведении преобразований, компания Singleton Birch получила возможность управлять своим будущим.