Наталья Карпова
Хромовый концентрат — основной компонент для производства феррохрома, который необходим для производства нержавеющей стали. Хром придает стали твердость, прочность, вязкость и коррозийную стойкость. В Казахстане хромовый концентрат в основном производится в Актюбинской области. Здесь, на Донском горно-обогатительном комбинате (Донской ГОК), филиале АО «ТНК «Казхром», входящем в состав Eurasian Resources Group (ERG), добывают и перерабатывают руду с самым высоким в мире содержанием хрома, ежегодно получая 4,4 млн т товарной продукции. Особенность обогатительного производства на Донском ГОКе — экологическая безопасность применяемого метода обогащения, низкие себестоимость и энергозатратность.
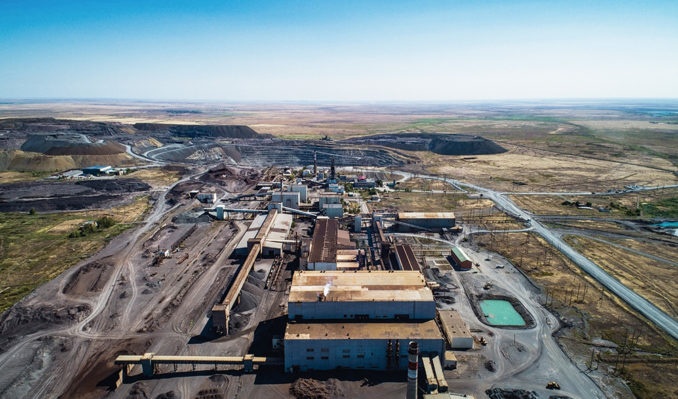
Экскурс в историю
Дробильно-обогатительная фабрика № 1 (ДОФ-1) свою историю ведет с 1945 года, когда в работу запустили первую фабрику дробления и сортировки. Тогда возникла потребность в дроблении и сортировке по крупности богатой хромовой руды. Руда дробилась и классифицировалась на три класса, самый крупный класс в те годы «обогащали» вручную, женщины руками отбирали из руды пустую породу с движущейся конвейерной ленты.
Действующий участок дробления и погрузки ДОФ-1 эксплуатируется с 1964 года. С увеличением объемов добычи содержание оксида хрома в руде стало снижаться, появилась необходимость в обогащении руды, было принято решение о строительстве первой обогатительной фабрики Донского ГОКа, в 1973 году ее сдали в эксплуатацию. С вводом фабрики было начато освоение новой в стране технологии обогащения хромовых руд, и в 1974 году начался выпуск хромового концентрата из добываемых руд и переработка бедных руд, накопленных на временных складах.
В 1977 году ДОФ-1 стала самой крупной в мире по обогащению хромовой руды, с производством концентрата свыше 200 тыс. т. И с этим показателем обогнала все зарубежные фабрики, включая ЮАР.
Строить фабрику № 2 (ДОФ-2) начали в 1980 году, спустя несколько лет запустили карьерную цепочку для дробления богатой руды из карьера «40 лет КазССР». И в первый же год продробили 903,9 тыс. т богатой руды и 14,9 тыс. т бедной. Введенная годовая мощность фабрики по дроблению составила 3,4 млн т. В 2005 году объем по сырому дроблению составил 4,66 млн т руды. Постепенно вводились другие переделы — отделение для переработки кусковой бедной руды класса 10–160 мм, годовая производительность по концентрату составила 800 тыс. т, два отделения по переработке бедной руды класса 0–10 мм годовой производительностью 2 млн т.
В декабре 2004 года дробильно-обогатительная фабрика № 2 Донского ГОКа, произведя 821 тыс. т кускового концентрата в корпусе тяжелосредного обогащения, превысила мировое достижение среди аналогичных предприятий.
Большой шаг в плане освоения новых технологий как по технологической схеме, так и по автоматизации процессов — ввод в эксплуатацию на ДОФ-2 первых в СНГ участков по производству хромовых окатышей. В основе — технология финской компании «Оутотек». Годовая мощность каждого участка по производству окатышей составила 700 тыс. т. Производство такого количества окатышей заменяет добычу из шахт 1,9 млн т сырой руды, из которой можно получить такое же количество кусковой продукции, особенно востребованной ферросплавщиками. В 2009 году сдано в эксплуатацию отделение обогащения мелких и тонких классов № 2. Таким образом, в состав ДОФ-2 вошли шесть участков: участок дробления, отделение обогащения в тяжелых средах, два отделения обогащения мелких классов, два участка по производству окатышей, на основании этого фабрика была переименована в фабрику обогащения и окомкования руды (ФООР).
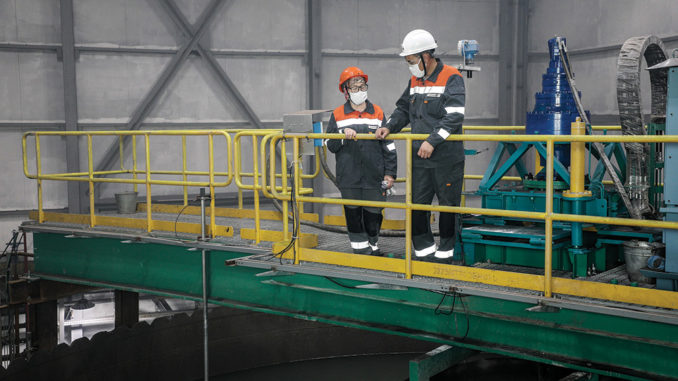
Об обогатительных процессах на фабриках, продукции и специфике работы расскажет главный обогатитель АО «ТНК «Казхром» Марина Имекешова:
— Будучи главным обогатителем, я отвечаю за разработку мероприятий по совершенствованию технологии обогащения хромовых руд, выполнение планов производства, соблюдение технологической и производственной дисциплины на обогатительных фабриках, разработку и внедрение организационно-технических мероприятий, направленных на повышение производительности труда, снижение себестоимости, принимаю участие в разработке долгосрочных стратегических планов развития и др. В моей зоне ответственности как металлургический передел, где мы обогащаем шлаки и получаем металлоконцентрат, так и обогатительный передел «Казмарганца», ДГОКа и дочернее предприятие ТОО «Акжар-Хром», где перерабатываются отходы обогатительного производства. Технологические схемы обогащения классические, метод — гравитационный. На сегодня на дробильно-обогатительной фабрике № 1 ДГОКа идет реконструкция одного из отделений, второй цех работает на полную мощность. Добываемая в Хромтау руда легкообогатимая, с высоким содержанием оксида хрома. Если говорить о богатой руде, то содержание оксида хрома — 47–50 %. В концентратах — не менее 48 %.
На фабриках производится восемь марок дробленой руды и семь марок концентратов, а также брикеты и окатыши. В рудоуправлении «Казмарганец» производятся марганцевые концентраты двух марок: 40–150 и 10–40 мм. Эти концентраты необходимы для производства ферромарганца. Потребитель марганцевого концентрата — Аксуский завод ферросплавов. Содержание марганца в концентратах высокое — не менее 40 %.
Марганцевая и хромовая руды поставляются производителям ферросплавов, а также на предприятия химической промышленности. Перевозка хромовой и марганцевой продукции осуществляется железнодорожным транспортом.
— В чем отличие процессов обогащения ДГОКа?
— Основное отличие в том, что по операционным затратам у гравитационного метода обогащения самая низкая себестоимость при достаточно высокой эффективности обогащения и показателю извлечения металла в товарную продукцию не менее 85 %. Гравитационный метод обладает не только низкими операционными, но и низкими трудозатратами. Важное преимущество — метод экологически безвредный. Можно назвать его самым безопасным способом обогащения. Также процесс имеет низкие энергозатраты.
— В каком направлении развивается производство, обладая такими преимуществами?
— В компании уделяют очень много внимания модернизации и вопросам переработки отходов, которые есть в любом производстве. В частности, речь идет о модернизации технологической схемы в плане повышения извлечения полезного компонента. Фокусируемся на извлечении тонких классов и добиваемся результатов. Приведу пример: на ТОО «Акжар-Хром» перерабатываем лежалые шламовые хвосты, чтобы повысить извлечение хрома, дополнительно используем концентрационные столы (со шламовой декой), в прошлом году впервые протестировали технологию обезвоживания тонкого концентрата в технотубах (перфорированных емкостях). До этого момента в действующей технологии выполнить процесс обезвоживания тонкого концентрата не представлялось возможным.
Хотелось бы отметить, что все технологические линии производства автоматизированы. Автоматизированная система управления производством позволяет операторам регулировать процессы дистанционно. В 2008 году и на ферросплавных заводах, и на Донском ГОКе внедрена информационная система управления производством (ИСУП). В данной системе отражена вся информация по технологическим процессам Донского ГОКа: состояние оборудования, простои, технологические показатели, видны данные по маркшейдерским замерам для оперативного учета. Данные передаются в автоматическом режиме.
Еще один аспект развития экологически важен — мы стремимся к обеспечению внутреннего водооборота фабрик, чтобы каждый участок работал на внутреннем водообороте. В нашей климатической зоне есть необходимость экономичного использования водных ресурсов. В 2020 году введен в эксплуатацию участок оборотного водоснабжения для обогащения в тяжелых средах.
— На ДГОКе есть отдел технического контроля, технологическая лаборатория, контролирующие показатели. Что зависит от работы этих подразделений на фабриках?
— Это очень важное звено. От отдела технического контроля напрямую зависит качество выпускаемой товарной продукции. За химической лабораторией — анализ, технологическая лаборатория выполняет научные и прогнозные исследования и контроль технологических процессов, а лаборатория охраны окружающей среды выполняет контроль и мониторинг выбросов по отходящим газам, воде и воздуху на границах санитарно-защитных зон подразделений предприятия.
На Донском ГОКе внедряется система «Баланс металла». Эта система позволит вести точный учет движения и баланса металла в производственном цикле, куда входит и добыча, производство и отгрузка продукции. Проект «Баланс металла» (БМ) включает два направления: внедрение автоматизированной системы БМ и техперевооружение балансовых точек. Данный проект охватывает как Донской ГОК, так и два ферросплавных завода (Актюбинский и Аксуский заводы ферросплавов) АО «ТНК «Казхром».
Полное внедрение и реализация проекта запланированы на 2022 год.
— Расскажите о дальнейшей стратегии по части обогащения и методов переработки.
— Первое — это внедрение новых методов обогащения для хромового сырья, исследовательская работа в этом направлении ведется уже не один год, и мы на пороге больших открытий в этом направлении.
Второе — переработка техногенных минеральных образований. Хвосты обогащения класса 10–160 мм, в которых содержание оксида хрома составляет 3 %, являются отвальными отходами и используются для заполнения выработанного пространства карьеров. С 2021 года планируется запуск проекта по дообогащению хвостов класса 0–10 мм производительностью 123 тыс. т концентрата в год. С целью комплексного использования сырья и повышения извлечения ценного компонента в 2021 году запланирована реализация проекта по переработке ранее заскладированных шламовых хвостов, проект «Шламы-2», производительностью 1,7 млн т по переработке и производству 290 тыс. т концентрата в год.
Третье — окускование хромовой мелочи.
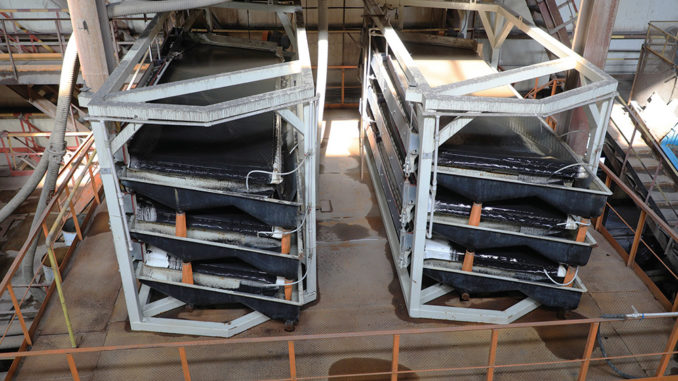