Адреас Фройнд, дипломированный инженер, старший менеджер по продажам;
Артур Хуберт, дипломированный инженер, управляющий директор;
Феликс Хайнике, инженер, доктор, старший технолог, Köppern Aufbereitungstechnik GmbH & Co. KG, Agricolastraße 24, 09599 Фрайберг, Германия, е-мail: contact@koeppern.com, tel. +49-3731-2018-0
Введение
Последние 40 лет отмечены стабильным развитием технологии переработки руды с помощью валковых прессов высокого давления (High Pressure Grinding Rolls — HPGR). Компания Köppern с более чем 120-летним опытом в переработке порошковых материалов посредством измельчения между двумя валками, а также в производстве и эксплуатации валковых прессов в технологии брикетирования и прессования также сделала весомый вклад в развитие.
АО «Стойленский ГОК» (СГОК), дочернее предприятие группы НЛМК, базирующейся в Липецке, Россия, также внесло свой вклад в обоснование целесообразности применения данной технологии. В мае 2016 года СГОК первым в России и странах СНГ успешно ввёл в эксплуатацию валковые прессы высокого давления для дробления железистых кварцитов. В течение следующих полутора лет было смонтировано и успешно запущено еще семь установок.
На СГОКе технология HPGR применяется в дополнение к традиционным конусным дробилкам, установленным перед шаровыми мельницами, что позволяет компании увеличить производительность фабрики на 12–15 % и, следовательно, производство железорудного концентрата на 2 млн т в год. Помимо этого, удалось значительно снизить потребление электроэнергии и мелющих тел для переработки руды.
До успешного внедрения технологии HPGR на СГОКе фабрика перерабатывала 31,5 млн т железной руды в год с получением 15,2 млн т железорудного концентрата с содержанием железа около 66,5 %. Это соответствовало приблизительно 18 % от общего объема производства железной руды в год в Российской Федерации. Основной задачей СГОКа является поставка железорудного концентрата и окатышей на Новолипецкий металлургический комбинат (НЛМК) для производства стали.
Для стабильного и полного удовлетворения потребностей НЛМК в железорудном концентрате в рамках «Стратегии-2017» на СГОКе поставлена цель увеличить ежегодное производство железной руды с 32 до 37 млн т. Для ее достижения на начальном этапе рассматривалось строительство пятой технологической секции в дополнение к уже имеющимся четырем. Однако из-за очень высоких инвестиционных затрат СГОК и его владелец отказались от этого варианта. Поэтому было принято решение дооборудовать имеющиеся секции валковыми прессами высокого давления, чтобы увеличить производительность существующих установок и достичь поставленных целей.
В данной статье описываются наиболее важные аспекты и преимущества технологии HPGR. Вместе с тем основное внимание уделяется успешной реализации проекта и последних совместных проектов, связанных с цифровизацией производства и оптимизацией гранулометрического состава материала с акцентом на оптимизацию износостойкости оборудования.
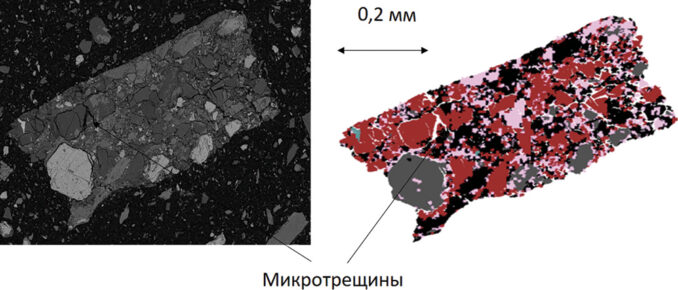
Эффективное измельчение с помощью HPGR и тестирование
Измельчение в HPGR известно как очень эффективное измельчение для множества материалов [Михаелис, 2005]. Основной причиной этого является то, что материал перерабатывается в высокоинтенсивной зоне измельчения за миллисекунды, уменьшая гранулометрический состав при формировании большого объема мелочи, и инициирует появление трещин по границе зерен минерала, как показано на рис. 1.
Данные одновременно возникающие эффекты обладают различным, но не значительным влиянием на показатели работы шаровых мельниц далее по переделу. Данный эффект может быть приблизительно определен по формуле Бонда как Wsp — удельная мощность мельницы, где Wi — рабочий индекс Бонда, а P80 и F80 соответственно суммарные проценты продукта и питания 80 % от массы [Бонд, 1952]:
(1).
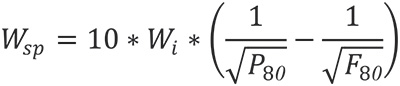
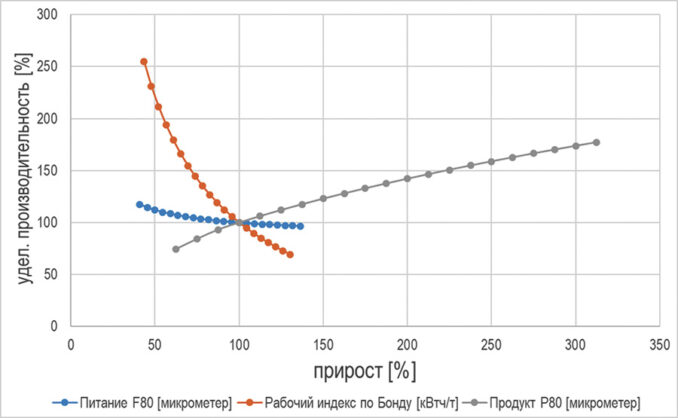
На рис. 2 показан эффект от применения HPGR, оказываемый на работу шаровой мельницы, с учетом технологических показателей шаровой мельницы по питанию шаровой мельницы (F80), продукту шаровой мельницы (P80) и рабочему индексу Бонда. Можно увидеть, что самые большие эффекты на работу шаровых мельниц достигаются за счет снижения рабочего индекса Бонда, что, в свою очередь, приводит к уменьшению фракции продукта мельницы P80. Изменение фракции питания шаровой мельницы F80 обладает меньшим влиянием [Хайнике, 2019].
Чтобы выяснить, как эти три эффекта оказывают влияние на работу шаровых мельниц СГОКа, в начале 2014 года в лаборатории Köppern в г. Фрайберге, Германия, были проведены испытания HPGR. Данные тесты были также необходимы, так как в России на тот момент не было практического опыта работы с HPGR и данных о влиянии данной технологии на последующие переделы.
Тесты выполнялись на полупромышленной установке HPGR Köppern (рис. 3). Выдержка результатов тестирования приведена в табл. 1.
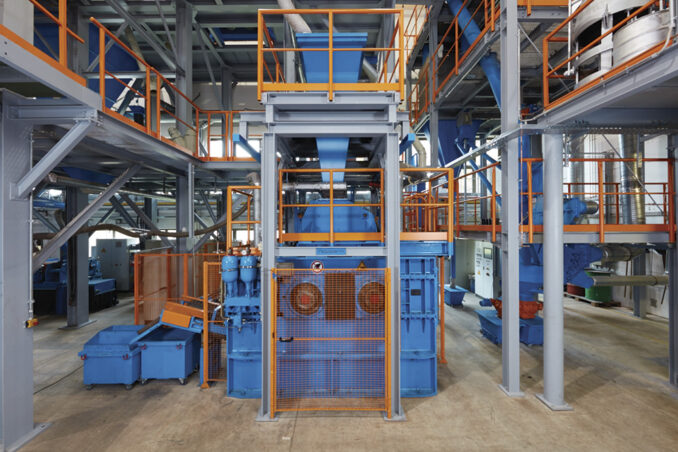

В ходе данных тестов все необходимые технологические параметры для проектирования промышленной установки HPGR были запротоколированы в дополнение к распределению гранулометрического состава. Стало очевидно, что замкнутый цикл вместе с грохотом является наиболее эффективным методом работы в части целевого уменьшения гранулометрического состава. Однако оказалось, что даже при работе в один проход целевая фракция продукта HPGR достигалась, при этом рабочий индекс Бонда может быть снижен приблизительно на 20 % [Povey, 2017]. Однако для дальнейших расчетов было принято уменьшение индекса Бонда только на 10 %. После завершения полномасштабного тестирования с положительными результатами началось планирование промышленного применения HPGR.
Внедрение технологии HPGR в существующий производственный процесс СГОКа
В связи с советским традиционным подходом к центральному планированию и проектированию крупномасштабных инвестиций в переработку сырьевых материалов многие горно-обогатительные комбинаты СНГ были построены одинаково в части компоновки и проектирования технологии. СГОК — один из таких. Руда добывается в карьере или шахте, проходит три или четыре стадии дробления и далее подается на первую стадию измельчения для дальнейшей переработки и обогащения железной руды для получения железорудного концентрата (рис. 4).
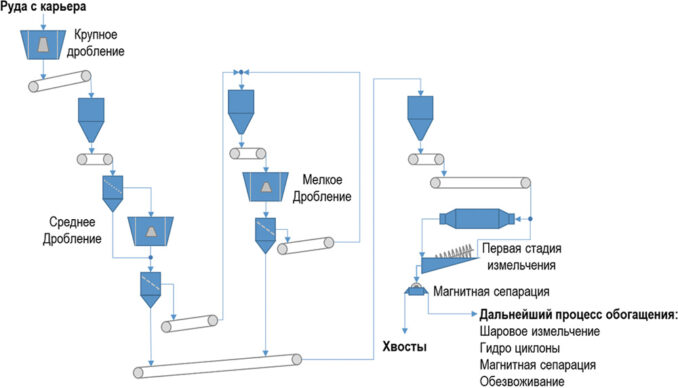
На основании результатов тестирования было принято решение установить HPGR между стадией мелкого дробления и первой стадией измельчения в шаровой мельнице с работой в один проход, хотя результаты четко показывали, что замкнутый цикл работы HPGR с грохотом дает более высокий потенциал в части технологического процесса. Данное решение было принято потому, что существующее и доступное место на фабрике было ограничено. Выбранный вариант также предоставлял возможность упрощения настройки и интеграции HPGR.
В ходе первой фазы проекта две установки с производительностью 4 500 т/ч каждая должны были быть смонтированы между стадией мелкого дробления и обогатительной фабрикой. Однако данный вариант был отброшен из-за риска забивки основного бункера (10 000 т) до первой стадии измельчения. Данный бункер просто не был спроектирован для более тонкого продукта HPGR. Модернизация разгрузки была бы технически необходима, но не обоснована с экономической точки зрения. По этой причине было принято решение, предусматривающее установку HPGR после данного бункера. Оно учитывало дальнейшее добавление в схему HPGR с меньшей производительностью, по 655 т/ч каждая, до каждой первой стадии измельчения. Это означало, что необходимо будет смонтировать восемь установок. Основное преимущество данного решения заключалось в том, что можно было использовать существующие корпуса для четырех из восьми установок. На рис. 5 показана схема размещения HPGR. Проект включает реверсивный ленточный конвейер, подающий материал на HPGR. В случае необходимости технического обслуживания HPGR данный конвейер может подавать материал напрямую в шаровые мельницы, и нет необходимости полностью останавливать технологическую линию.
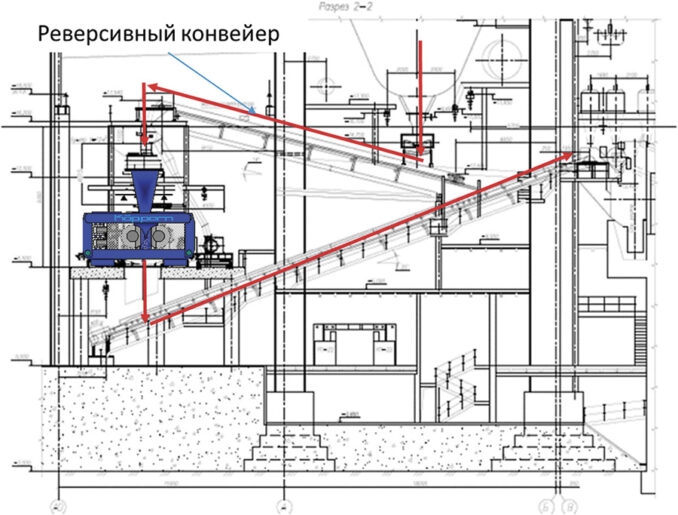
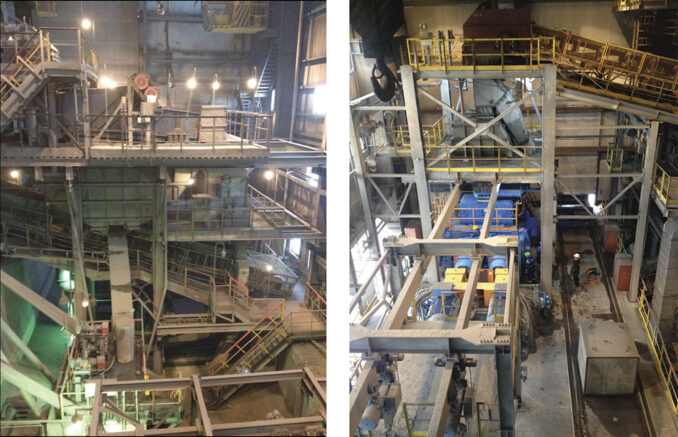
Реализация проекта
В рамках реализации проекта компания Köppern поставила HPGR типа 500/15-1000. Данные установки оснащены валками диаметром 1 500 мм и шириной 1 000 мм. Установленная мощность основных двигателей составляет 591 кВт каждая. Как было уже упомянуто выше, пропускная способность каждой установки составляет 655 т/ч. Как во многих других проектах, временные сроки реализации были очень сжатые. В табл. 2 показана обзорная информация по графику реализации. Благодаря очень тесному и профессиональному сотрудничеству между инженерами СГОКа и Köppern выполнение такого сжатого графика никогда не ставилось под вопрос.
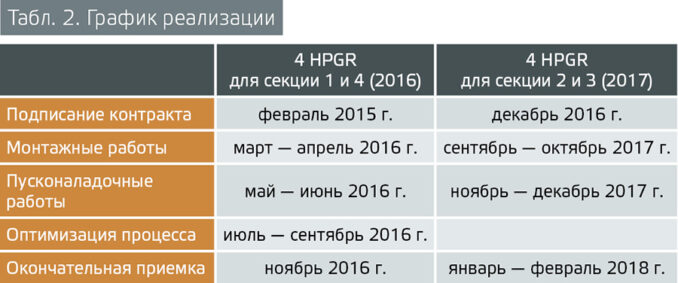
Пусконаладочные работы установок прошли без каких-либо серьезных проблем. В ходе трехмесячной оптимизации процесса первых четырех установок они были интегрированы в процесс СГОКа для обеспечения непрерывного производства. Через один месяц после успешной приемки первых четырех установок, в ноябре 2016 года, был заключен контракт на поставку вторых четырех установок.
После пусконаладочных работ всех восьми установок HPGR СГОК смог увеличить производительность фабрики на 12–15 %, достичь целей «Стратегии-2017» в части увеличения годовой производительности по руде до 37 млн т. Дополнительный положительный эффект от технологии HPGR — снижение удельного потребления электроэнергии на производство одной тонны железорудного концентрата — 1,5–2,2 кВт/ч.
Опыт работы
После успешного внедрения восьми HPGR для 4-й стадии дроб-ления на СГОКе в 2016 и 2018 годах эти машины стабильно работают и по настоящее время [Heinicke, 2019]. Ожидаемая эксплуатационная готовность машин стабильно достигает 98 %. Кроме того, они не требуют значительных усилий для проведения технического обслуживания. С целью достижения минимального износа для использования в конструкции машины выбирались только высококачественные материалы. Однако HPGR выполняет физический процесс измельчения, который всегда подразумевает износ контактных поверхностей. На рис. 8 показаны области, где железная руда оказывает наибольшее воздействие на детали машины. Основная задача при техническом обслуживании — замена изнашиваемых деталей по истечении их срока службы в соответствии с табл. 3.
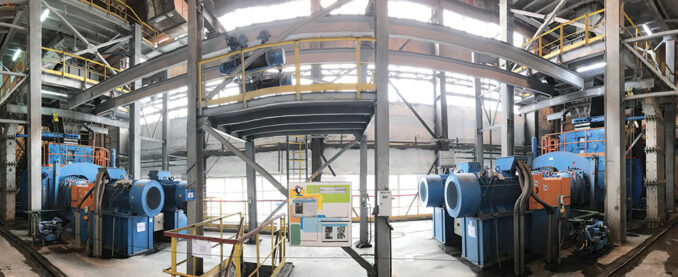
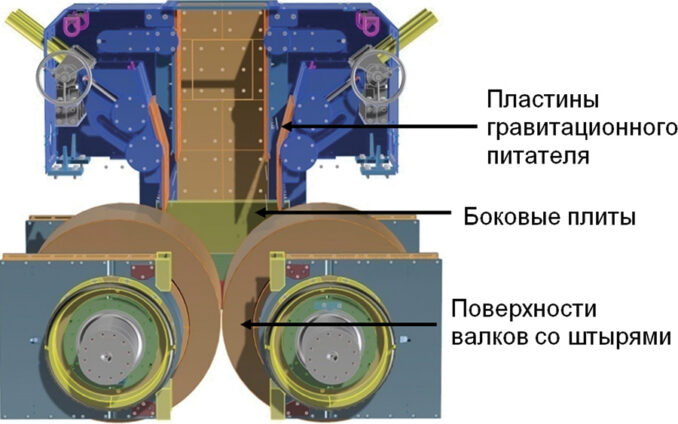
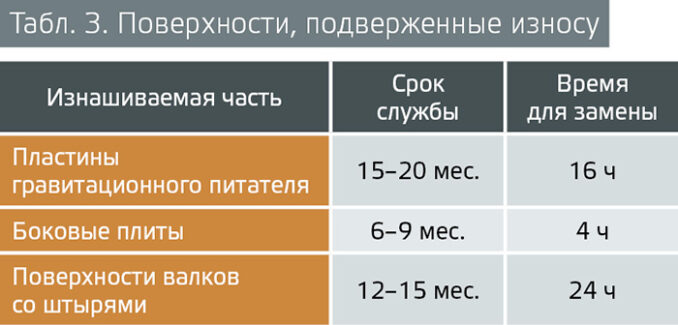
Замена изношенных поверхностей валков со штырями, включая производственные потери во время простоя, занимает наибольшую долю в эксплуатационных расходах. Поэтому важной задачей при оптимизации проекта является анализ и сокращение этой части затрат.
Цифровой анализ работы HPGR
Первым шагом в сторону оптимизации является установка цифровой системы измерения для создания детализированной модели рабочих характеристик HPGR. Такая современная система сбора данных машины обеспечивает получение важной информации с нескольких датчиков. На СГОК она контролирует зазор между валками пресса, давление в гидравлической системе, скорость вращения валков, а также силу тока, потребляемого двигателями, и температуру двигателей. Сигналы передаются с ПЛК машины в измерительную систему. Она также может собирать технологические данные контура измельчения, выполнять анализ эксклюзивных данных (периферийные вычисления) и обмениваться результатами с другими системами. С помощью предварительно обработанных данных создаются отчеты и графики, которые затем могут быть доступны через безо-пасную сеть Интернет. При этом используются высококлассный VPN, искусственное шифрование и защищенные модемы, чтобы поддерживать состояние информации в соответствии со стандартами безопасности данных СГОК. Таким образом, система представляет собой типичный компонент промышленного интернета вещей (IIoT), как показано на рис. 9.
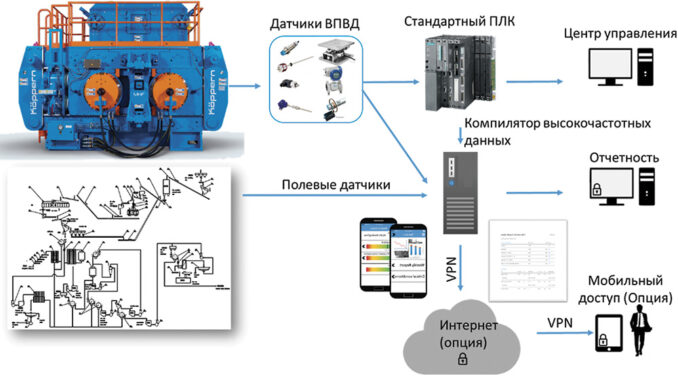
В качестве одного из примеров можно привести крутящий момент в приводном механизме, который можно анализировать для прогнозирования срока службы редукторов. На рис. 10 приведен пример некоторых данных, полученных в процессе выполнения измерений. Общие характеристики HPGR, установленных на СГОКе, являются очень плавными, с минимальным количеством отклонений в процессе измельчения. В целом машина характеризуется неизменной стабильностью работы.
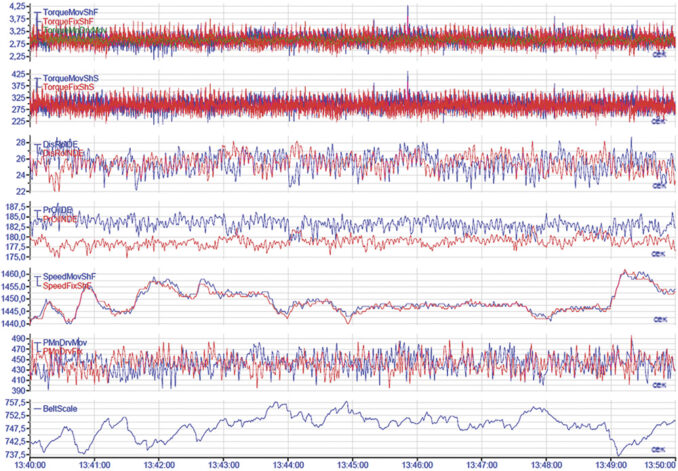
В начале работы отмечались нечасто возникающие скачки крутящего момента привода. Такие сигналы можно было комбинировать с другими сигналами, что позволяло выявлять ситуации, когда между валками HPGR попадали инородные металлы. Это было связано с настройкой металлодетектора и позволило улучшить его настроечные параметры таким образом, чтобы можно было свести к минимуму количество пропусканий инородного металла. Таким образом, исключается множество ситуаций, когда имеют место локальные повреждения штырей на поверхностях валков. Благодаря этому существенно увеличивается общий срок службы бандажей валков. Чтобы контролировать настройки металлодетектора, был включён режим сигнализации, позволяющий получать регулярные отчёты и анализировать состояние на еженедельной основе.
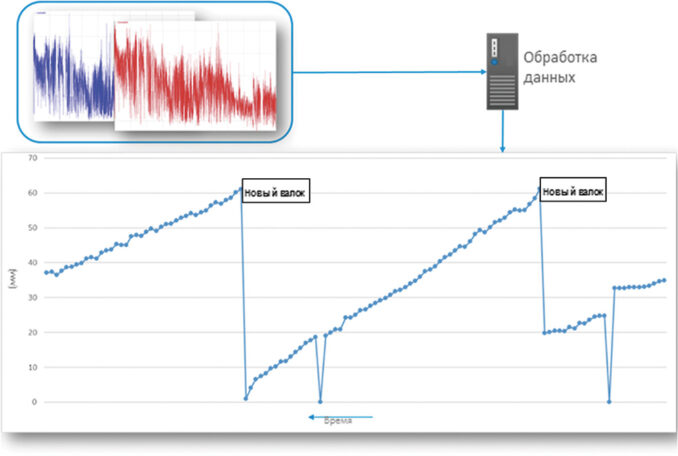
Другой пример — долгосрочный анализ измерения положения валков, как показано на рис. 11. По всей видимости, величина зазора уменьшалась с течением времени. Причем это не является следствием несбалансированных сигналов датчика. Различные свойства сырья также могут повлиять на процесс обработки сыпучей массы внутри HPGR и привести к уменьшению зазора, но в данном случае обрабатываемая руда была из одних и тех же участков карьера и имела одинаковое качество.
Рассчитать среднюю степень износа поверхностей валков позволяет специальный алгоритм фильтрации и анализа данных. Это возможно, поскольку длина штырей на поверхности валков HPGR со временем уменьшается. Об этом свидетельствуют сигналы датчиков положения плавающего валка HPGR с обеих сторон пресса.
При дополнительном учете коэффициента использования машины срок службы бандажей валков может быть спрогнозирован с разумной точностью. Это помогает заранее планировать техническое обслуживание валков, что, таким образом, является полезным вкладом в достижение общей цели перехода на профилактическое техобслуживание.
Заключение и перспективы
АО «Стойленский ГОК» (СГОК), предприятие группы компаний НЛМК, базирующейся в Липецке, Россия, успешно запустило валковые прессы высокого давления для измельчения железистых кварцитов впервые в России и странах СНГ. Технология HPGR применяется в дополнение к традиционному дроблению в конусных дробилках, в переделе до шаровых мельниц. В результате СГОК смог увеличить производительность фабрики на 12–15 %, увеличив производство железорудного концентрата на 2 млн т, до 16,6 млн т в год. Дополнительно были значительно снижены потребление электроэнергии и расход мелющих тел. За счет очень тесного и профессионального сотрудничества между инженерами СГОКа и Köppern проект был реализован вовремя.
Проект показал, что технология HPGR является хорошим вариантом и альтернативой для усовершенствования работы существующей обогатительной фабрики с качественной и количественной точки зрения.
В результате успешного внедрения HPGR в 2019 году СГОК принял решение установить еще две HPGR. В отличие от других восьми установок данные две установки будут расположены в конце технологического процесса подготовки сырья непосредственно перед окомкованием. С помощью этих двух HPGR будет увеличена удельная поверхность железорудного концентрата. Это должно улучшить качество производимых окатышей. Данные две установки HPGR также являются частью проекта увеличения производительности фабрики окомкования с 6 млн т до 8 млн т, который реализуется в настоящее время, а выполнение пусконаладочных работ запланировано на 2021 год.
Приглашаем вас посетить наш стенд A075 на выставке MiningMetal Central Asia / «Горное оборудование, добыча и обогащение руд и минералов» в г. Алматы, Казахстан. Выставка пройдет с 29 сентября по 1 октября 2021 года.
Список литературы
1. Бонд Ф. С. Третья теория измельчения. Проектирование в горной промышленности, 1952. Стр. 484–494.
2. Повей Б. C. Внедрение HPGR на обогатительной фабрике СГОК в России на магнетите. Тезисы, 2017. Стр. 1–19.
3. Михаелис Х. Реальные и потенциальные металлургические преимущества HPGR при переработке твердых типов руд. Конференция Рэндол, 2005. Стр. 1–9.
4. Хайнике Ф. Усовершенствование стандартной для СНГ схемы за счёт применения HPGR, 2019. Стр. 1–20.