Сергей Николаев, Станислав Поплавский, Михаил Гусев
Использование нейросетей для решения задач промышленности последнее десятилетие имеет широкое применение, и одним из актуальных направлений является разработка цифровых двойников производственных процессов, где используются нейросетевые модели технологических процессов. Цифровые двойники, или советчики (также популярное название среди эксплуатантов), позволяют снижать затраты и себестоимость производства, повышать эффективность и производительность процесса, а также улучшать качество производимой продукции.
На российском рынке данная технология стала доступна благодаря разработанной непосредственно инженерами по оборудованию программной платформе, сочетающей в себе возможность разработки нейросетевых моделей технологических процессов и инновационные подходы трансферного обучения.
Как осуществляется разработка цифрового двойника технологического процесса?
В основе лежит подход real time оптимизации. Оптимизация происходит путем выдачи рекомендаций операторам по изменению управляющих параметров технологического процесса таким образом, чтобы набор выбранных параметров находился в оптимальном диапазоне значений внутри техрегламента (рис. 1).
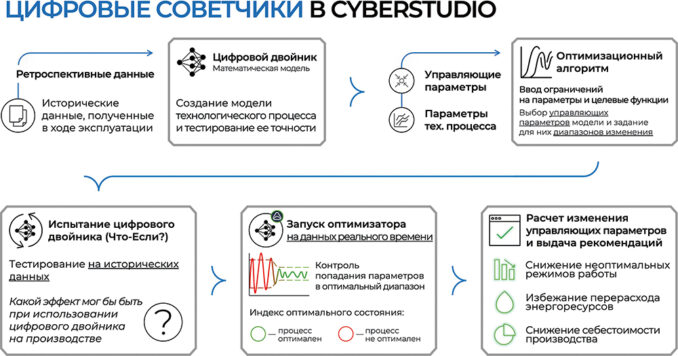
Путь пользователя
Пользовательский путь при настройке процесса оптимизации включает в себя создание модели процесса на основе нейросетей или физико-математической модели (цифрового советчика) и тестирование ее точности, настройку оптимизационного алгоритма и испытание математической модели (цифрового советчика) на исторических данных в режиме «Что если», и запуск модели (цифрового советчика) на данных реального времени.
При конфигурации оптимизационного алгоритма пользователь выбирает из числа входных параметров модели управляющие параметры и задает для них возможные диапазоны изменения. Также настраивается оптимальный диапазон для целевых функций.
Испытание цифрового двойника технологического процесса осуществляется путем виртуального эксперимента на исторических данных (прогонка). Результат показывает эффективность оптимизации. Какой эффект мог бы быть, если бы оптимизацию применяли ранее (на исторических данных).
Для общей оценки оптимальности процесса используется интегральный показатель — индекс оптимального состояния, изменяющийся от нуля (процесс не оптимален) до единицы (процесс оптимален).
При запуске цифрового советчика на данных реального времени ПО автоматически контролирует попадание целевых параметров в оптимальный диапазон и на основе внутренних алгоритмов рекомендует оператору изменения управляющих параметров.
Приведем несколько интересных примеров.
Пример № 1
Одним из кейсов разработки цифрового двойника технологического процесса на предприятии является пример оптимизации режимов работы агрегата нанесения покрытий. Данный проект выполняется для предприятия металлургической отрасли.
Целью проекта является минимизация расхода покрытия на технологическом агрегате.
Решение данного проекта подразумевает создание рекомендательной системы по выдаче параметров работы агрегата для попадания в минимальный допустимый диапазон толщины. Такая система была создана в виде цифрового советчика в специализированном ПО.
Для решения задачи в ПО была создана нейросетевая модель процесса на основе физико-математической модели. Модель включает в себя более 10 параметров, учет которых необходим для корректного вывода рекомендаций для улучшения технологического процесса. Результат работы модели и оптимизатора показывает возможность улучшения режимов и достижение до 5 % по снижению расхода покрытий.
Пример № 2
Другим кейсом применения цифровых советчиков является применение ПО для снижения содержания целевого компонента в отходах производства, где ПО было применено для оптимизации работы технологических печей.
Решаемой проблемой является высокое содержание целевого компонента в отходах, что ведет к потенциальной упущенной выгоде от снижения производительности процесса.
Решением данной проблемы является использование цифрового советчика для подбора оптимальных параметров технологического процесса для снижения содержания целевого компонента в отходах.
Для разработки цифрового двойника используется та же платформа, в которой создаются модели режимов печи и конфигурируется оптимизатор.
Результатом виртуальной симуляции моделей технологического процесса в режиме «Что если» и работы оптимизатора стало выявление режимов, которые можно улучшить, и получение рекомендаций для достижения пониженного содержания целевого компонента в отходах. Таким образом, потенциальный эффект от применения цифрового советчика, разработанного в ПО, составляет до 0,2 % снижения целевого компонента в час.
В настоящее время проект проходит стадию подготовки к внедрению на предприятие.
Пример № 3
Помимо технологии цифровых советчиков, с помощью этой платформы также могут решаться задачи предиктивной аналитики. Более подробное описание технологии предиктивной аналитики изображено на рис. 2. Одним из эффективных примеров является успешное внедрение системы предиктивной аналитики на горно-обогатительном комбинате, где она применяется на валковых прессах.
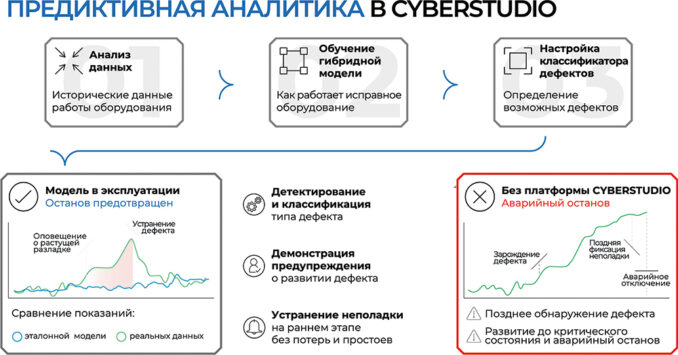
Общее количество охваченных системой агрегатов: 3 пресса. В системе одновременно для каждого пресса работает 162 математических предиктивных модели. С помощью ПО решаются задачи мониторинга состояния подшипников, зубчатых передач редуктора и т. д.
Системой было диагностировано несколько развивающихся дефектов. В том числе использование ПО предотвратило аварийную остановку пресса и потерю 3 600 т готового продукта. Совокупный экономический эффект составил более 70 млн руб. Горизонт прогнозирования неисправностей — 5–17 дней.
На текущий момент происходит масштабирование ПО на цех вакуум-кристаллизации, где сочетается применение системы предиктивной аналитики и технологии создания цифровых советчиков (оптимизации). Цех вакуум-кристаллизации включает в себя порядка 120 единиц оборудования, на каждую из которых в среднем приходится 5–6 моделей. Среди единиц оборудования представлены: насосы, насосы-мешалки, центрифуги и конвейеры.
Модели строятся для анализа работоспособности оборудования на основе показаний различных датчиков из штатной системы АСУТП заказчика.
Среди ожидаемых эффектов можно перечислить:
— минимизацию потерь производства от внеплановых технических простоев;
— автоматическое выявление момента возникновения условий для появления дефектов и их развития;
— автоматический расчет индекса технического состояния оборудования и систем и другие.
Помимо предиктивных моделей оборудования для задач данного цеха строятся оптимизационные модели производственного процесса. Оптимизационные модели строятся на основании показаний датчиков, контролирующих основной производственный процесс в вакуум-кристаллизационных установках. Основной ожидаемый эффект на производстве — поддержание требуемого качества готовой продукции и снижение потребления ресурсов (электроэнергия, вода).
Станислав Поплавский, директор по стратегическим партнерам, руководитель направления MineTech:
— Рынок цифровых советчиков и решений предиктивной аналитики растет ежегодно на более чем 15 %. Внедрение таких систем позволяет решить множество задач: сбор и обработка критических данных, прогнозирование отказов в работе оборудования, оптимизация режимов работы и повышение эффективности всего производственного цикла.
Совершенствование методов предиктивной аналитики в сторону развития цифрового двойника — это безусловный тренд в промышленной отрасли. Накопление данных об уязвимых частях оборудования, параметрах его работы и статистики поломок в математической модели позволяет корпорациям имитировать различные сценарии работы оборудования. Это особенно выгодно в части сокращения времени простоев, что подтверждает опыт лучших резидентов Фонда «Сколково», увеличивая срок службы отдельных единиц оборудования от 20 % и более. Как следствие решения, основанные на предиктивной аналитике, снижают и операционные расходы на поддержку оборудования.
Вопросы можно задать здесь: SPoplavskiy@sk.ru