Наталья Демшина
Цифровая трансформация в ЕВРАЗ ЗСМК стартовала еще в 2020 году. За это время передовые технологии стали неотъемлемой частью производственных процессов горнорудных предприятий и нашли свое применение в процедурах мониторинга оборудования, аналитики данных, предотвращении потерь и простоев. Об актуальных цифровых проектах, реализуемых компанией в сфере добычи и переработки сырья, журналу «Глобус» рассказал Владимир Мельниченко, директор сегмента «Горнорудные активы» ЕВРАЗ ЗСМК.
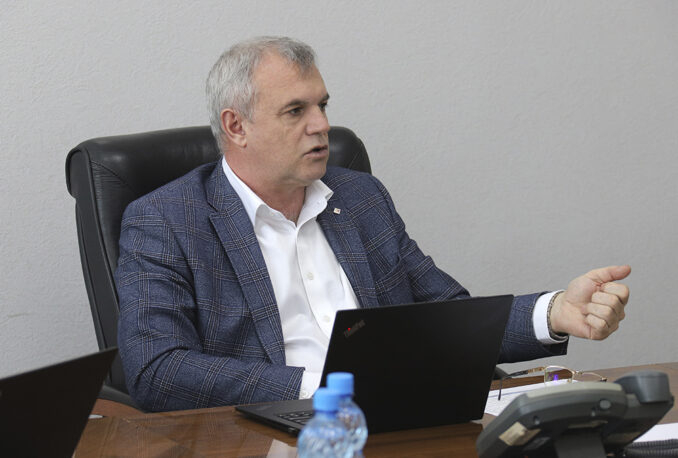
— Владимир Федорович, над внедрением каких проектов в области цифровизации сегодня работают горнорудные предприятия ЕВРАЗ ЗСМК?
— В настоящий момент идет реализация сразу нескольких проектов на всех горнорудных предприятиях компании — шахтах «Таштагольская», «Шерегешская» и «Казская». Самый крупный из них — на «Шерегешской»: мы завершили его реализацию в конце 2021 года. Сейчас идет обкатка внедренных инструментов и решений, и по полученным результатам уже можно сказать, что мы достигли поставленных целей.
В рамках этого проекта мы стали первыми среди горнорудных предприятий, кто применил связь на базе LTE, — в основном наши коллеги используют промышленный Wi-Fi. Благодаря этому решению мы получили устойчивую связь с поверхностью в режиме онлайн: персонал внутри шахты может в любое время связываться как с друг с другом, так и с коллегами на поверхности. Сети были проложены на двух горизонтах, для использования в шахтах были приобретены 40 смартфонов. На предприятии даже появилась новая должность — оператор, который всегда находится на связи с машинистами электровозов, самоходок, ВДПУ.
Были внедрены также инструменты для видеомониторинга: так, в точках максимальной концентрации работ, например при выполнении операций погрузки и выгрузки, оператор видит на мониторе, как идет работа. Такими же камерами оснастили камеру ремонта самоходных машин.
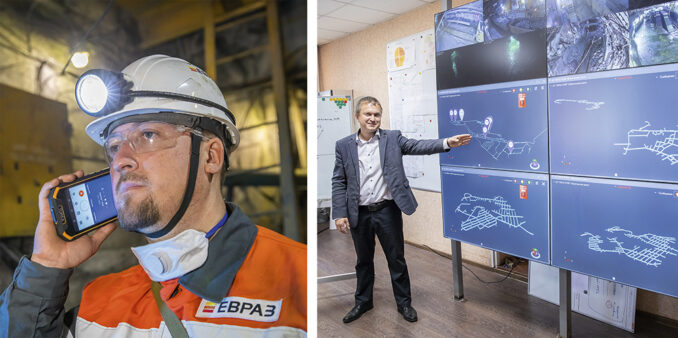
На самоходных машинах и электровозах установлены специальные датчики, которые позволяют видеть, где находится конкретная единица техники. Например, оператор видит, где в данный момент находится электровоз и по связи может подсказать машинисту, к какому рудоспуску лучше подъехать. Также система позволяет отслеживать вес груженых вагонов — это помогает работать более эффективно, не гонять составы впустую и не перевозить по шахте «воздух». Раньше горняки оценивали загруженность вагона на глаз, но, как понимаете, это было довольно субъективно. Теперь за этим следит специальная программа — цифровой помощник. Мы установили предельно допустимый минимальный порог, и, если вагон приходит недогруженным, система оповещает об этом. Это также дает нам возможности для проведения аналитики: в подобных случаях мы выясняем причину недогруза и устраняем ее.
«Умная» программа считает количество вагонов и фиксирует, сколько руды привезли за смену/сутки/неделю и так далее. Эти данные отображаются в мобильном кабинете руководителя — например, я могу посмотреть их в любой момент.
— Сколько времени и ресурсов вам потребовалось для подобных изменений?
— Реализация данного проекта заняла год, а инвестиции в него составили порядка 300 млн руб. Но результаты стоят всех усилий: проект позволил увеличить коэффициент использования оборудования на 5 %, а также повысил безопасность и производительность работ, сделал производственный процесс прозрачным, эффективным и, как следствие, позволил получить дополнительный объем сырья. Так, за 4-й квартал 2021 года благодаря цифровизации добыча на «Шерегешской» возросла на 50 тыс. т. В этом году планируем нарастить объем производства товарной продукции.
— Какие цифровые инструменты внедряются на других предприятиях?
— На Таштагольской шахте внедряем три цифровых проекта: мобильный 3D-сканер, программное обеспечение для построения электронных паспортов бурения, систему аэрогазового контроля.
Перед тем как добраться до руды, горняки отрабатывают первичную камеру, а затем закладывают ее специальной смесью. 3D-сканер помогает увидеть форму камеры как на ладони: все ее «закоулки», выступы, обвалившиеся горные массы, препятствия. В результате объем пустот вычисляется с высокой точностью, при этом часть расчетов производит само устройство. Также точное знание объема камеры позволяет рассчитать объем закладочной смеси для ее заполнения после отработки — это помогает прогнозировать параметры бурения вторичной камеры и не дает закладочной смеси попадать в руду. Качество руды остается высоким. Также данный инструмент позволят сэкономить время и силы наших сотрудников, которые раньше измеряли объем камеры стандартными способами.
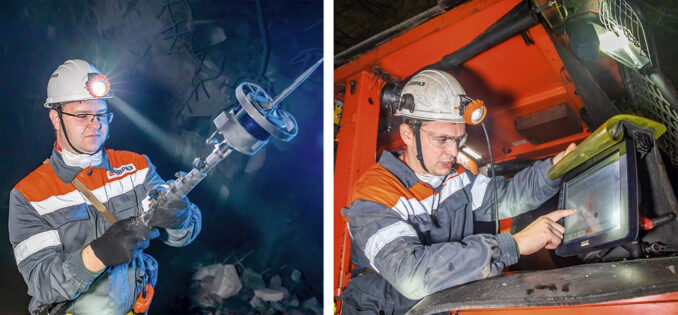
Электронные паспорта бурения загружаются на самоходные машины, чтобы оператор при бурении мог постоянно сверяться с нужными параметрами. Они не позволяют машине набурить лишнего. Даже если что-то пойдет не так, благодаря электронным паспортам можно вовремя скорректировать процесс.
Главный эффект от 3D-сканера и электронных паспортов — улучшение качества руды. Мы не забираем породу, не забираем закладочную смесь, что положительно влияет на качество руды. В 2022 году от двух этих инициатив мы также ожидаем прироста добычи.
Также на Таштагольской шахте сейчас внедряем систему аэрогазового контроля. Комплект датчиков отслеживает наличие в выработках двух газов — оксида углерода и двуокиси азота. Данные мониторинга поступают на пульт диспетчеру. Когда уровень концентрации газов после технологических взрывов снижается до допустимых значений, участок открывают для работы. По правилам допуск в место взрыва возможен только после замеров и разрешений горноспасателей. При этом электронная система оценивает состояние атмосферы в шахте раньше специалистов на несколько часов. Работы без опасений можно начинать в выработках, соседних со взрывом. Это увеличивает фонд рабочего времени и повышает общую производительность.
Также на всех рудных шахтах планируем запустить цифровой подсказчик обогащения. Он уже очень хорошо показал себя на Казском руднике, сейчас пробуем его на Шерегешском. В шахте мы берем руду от разных рудных тел, ведь в каждом из них отличается содержание железа. Но итоговый продукт мы должны выдавать стабильного качества с определенным содержанием железа. Цифровой подсказчик анализирует, с какого рудного тела взята руда, и советует оптимальное соотношение сырья, чтобы итоговое качество первичного концентрата было стабильным. Например, благодаря такому подсказчику на Казской шахте мы снизили потери железа в хвостах на 2,5 %.
— Цифровая трансформация затрагивает и обогатительное производство?
— Несомненно. На Абагурской обогатительной фабрике мы тоже внедряем цифровые подсказчики. Они подсказывают, какое количество времени должны работать мельницы и сепараторы, с какими напряженностями, чтобы снизить содержание железа в хвостах. Цифровой подсказчик по работе оборудования анализирует нагрузку на шаровые мельницы и заранее подает сигнал о необходимости их остановки для планового осмотра и ремонта. Цифровой подсказчик по шихтованию на рудных дворах позволит снижать потери железа в хвостах на 0,9–1 % и обеспечить стабильное качество вторичного концентрата, который поступает на ЕВРАЗ ЗСМК. Металлургам важна стабильность сырья, чтобы не перенастраивать оборудование каждый раз под новые параметры. Сейчас мы проводим донастройку подсказчика и уже в 4-м квартале этого года запустим его в работу.
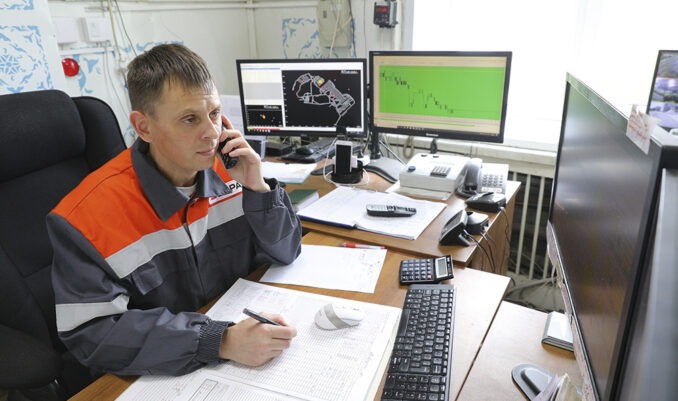
Также сейчас активно работаем над цифровым подсказчиком времени нахождения вагонов в гаражах размораживания. На скорость размораживания вагонов с первичным концентратом, который поступает с шахт в зимнее время, влияют три параметра: влага в первичных концентратах, время нахождения вагонов в пути и температура окружающей среды. С одной стороны, не хочется, чтобы вагон перестаивал в гараже и излишне нагревался, — это дополнительные затраты времени и тепла. С другой — гораздо хуже, когда вагон выходит из гаража недогретым — он приходит на выгрузку на опрокид, а концентрат смерзся и не выгружается. В итоге нужно снова везти вагон в гараж, а он снова остыл на морозе, и так по кругу… За зиму потери от этого могут достигать до 50 тыс. т вторичного концентрата. Наша команда создала программу, которая анализирует ключевые показатели и подсказывает, сколько необходимо греть каждый конкретный вагон в гараже размораживания. Сейчас наша цель — завершить программу до холодов, чтобы зимой опробовать ее в деле.
— Реализация цифровых проектов не приведет к сокращению сотрудников?
— Определенно нет. Сейчас мы закрываем около 2/3 от потребности во вторичном концентрате ЕВРАЗ ЗСМК, нам есть куда расти. Задача — производить еще больше. Наши горняки будут по-прежнему работать, а эффективная реализация цифровых проектов позволит нам не только гарантировать качество поставляемого сырья, но и существенно снижать его себестоимость и, соответственно, повышать нашу конкурентоспособность на рынке.