Владимир Фурс, vpfurs@mail.ru
В России в XVIII, XIX и XX веках в тайге можно было встретить группы людей, которые обследовали берега горных рек. Наряду с обычной поклажей, принятой в дальних походах охотников за пушниной и золотоискателей, такой как еда, оружие, одежда, лопата, они таскали огромные стальные котлы объёмом 300–500 л.
Вопрос: для чего? В тайге в те давние времена, да и сейчас, нет общепринятых дорог, есть только направления. Идти напрямую через тайгу очень тяжело. Передвигаться можно только вдоль русел рек. Да и то пробираться приходится через завалы из камней и стволов деревьев. Здесь лишний груз таскать с собой очень тяжело, хотя сибиряки сильны и выносливы. Так для чего им огромные тяжёлые котлы в тайге? Приготовить вареную пищу можно и в маленьких котелках, в таких огромных это сделать невозможно.
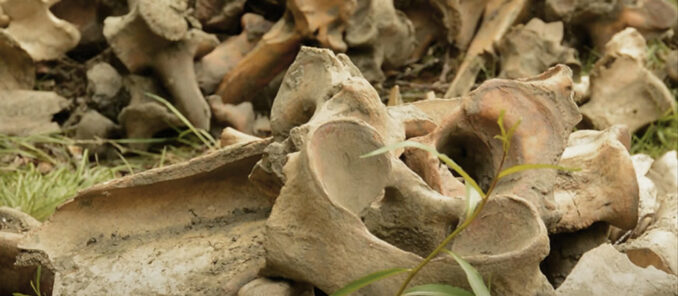
Ответ неочевиден и парадоксален одновременно. В тех котлах они пережигали на кострах огромные кости доисторических животных, которые жили в здешних краях 100 000–10 000 лет тому назад. Тогда вместо густой лесной тайги в тех местах были мамонтовые степи (тундростепи). Шерстистые носороги, мамонты, гигантские олени, древние бизоны и другие травоядные питались в тех местах. Больше всего травы росло в поймах и вдоль русел рек. Весенние разливы, летние и осенние дожди вымывали из почвы мельчайшие частицы золота и других тяжелых металлов. Вместе с песком и илом они накапливались в низинах и вдоль русел рек. На той плодородной почве хорошо произрастали тогда такие известные ныне гипераккумуляторы тяжелых металлов, как хвощи, полыни, злаки и некоторые другие растения. Мамонтовые тундростепи в те далекие времена были в десятки раз более биологически продуктивны, чем сейчас лесотундра и тайга.
На просторах тундростепей проживало огромное количество крупных травоядных животных. Средний мамонт или шерстистый носорог съедал за одни сутки более 100 кг растительности. Тяжелые металлы, в основном золото и другие платиноиды, откладывались в костях и мягких тканях этих животных. Поскольку самая питательная трава росла в поймах рек и озер, то необходимости в дальней миграции этих животных не было. Они рождались, жили и умирали в одном регионе. Обычно в теплой почве кости крупных животных разлагаются за 10–15 лет. А вот в условиях холода и вечной мерзлоты кости прекрасно сохранились до наших времен. Значит, если найти кости крупных травоядных доисторических животных, разбить их на куски, а потом пережечь их в стальном котле (нужно создать температуру свыше 1 100 градусов), то на дне котла под действием гравитации Земли осядет некоторое количество золотосодержащего металла. По соотношению объема пережженных костей и веса выплавившегося золота определяли, насколько данная местность богата на золото. Из рассказов поисковиков выходило, что из костей одного или двух взрослых мамонтов иногда на дне котла выплавлялось до фунта (400 г) золотосодержащего металла. Добыча таким способом золота не являлась основной целью этих людей. Важнее всего было найти богатое и крупное месторождение золота, пригодного для добычи.
Древних травоядных животных уже нет более 10 000 лет, а вот некоторые растения, которыми они питались в те времена, растут и сейчас. Хвощи, полыни, мхи и лишайники пережили природные катаклизмы и благополучно произрастают и в настоящее время. Опытный старатель знает, что в той местности, где обильно растет хвощ, всегда будет золото. В настоящее время науке известно более 400 видов растений, которые интенсивно впитывают в себя тяжелые металлы. Такие растения называются гипераккумуляторами тяжелых металлов. Они накапливают до 5 % тяжелых металлов в пересчете на сухой вес.
Итак, в Сибири 100–200 лет тому назад поисковики-старатели, используя древнюю технологию пережигания костей древних животных, могли не только определить наличие драгоценных металлов в данной местности, но и добыть их некоторое количество. А что же сейчас?
Новые источники и технологии
В настоящее время большинство легкодоступных и высокорентабельных мест золотодобычи истощилось или почти выработано. Поэтому золотодобывающие компании вынуждены осваивать все более неудобные и труднодоступные места добычи, применять все более сложные и дорогостоящие технологии, которые наносят серьезный ущерб окружающей среде. Так, отходы золотодобычи по некоторым технологиям по вредности для окружающей среды сопоставимы с отходами в атомной промышленности.
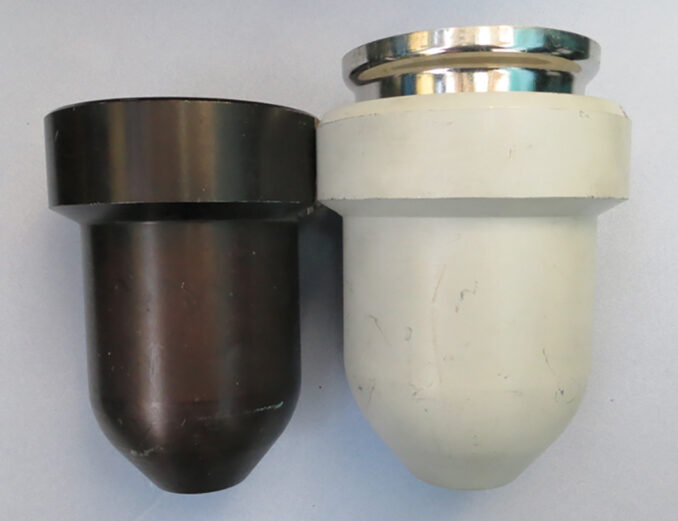
Истощение разведанных запасов полезных ископаемых, снижение темпов и количества вновь открываемых месторождений — все вместе это приводит к развитию альтернативных способов промышленного извлечения ценных компонентов из вторичного сырья, техногенных и нерентабельных для освоения месторождений. Развиваются новые технологии и совершенно новые направления, в частности метод фитодобычи (phytomining) и фиторазведки.
Сущнось фитодобычи заключается в использовании растений-гипераккумуляторов для извлечения ценных элементов из отработанных месторождений или месторождений с низким их содержанием. Эти виды растений способны накапливать металлические компоненты в исключительно больших количествах. Фитодобыча предполагает выращивание растений определенного вида на месте расположения отходов добычи или переработки, например на отвалах хвостов, а также на нерентабельных для освоения месторождениях. В процессе своей жизнедеятельности растения извлекают из почвы частицы ценных компонентов, постепенно накапливая их в стеблях или листьях. Наибольшее количество видов известных сейчас растений-гипераккумуляторов лучше, чем любой другой элемент, поглощают никель. Исследования, проведенные в 1990-х годах, показали, что некоторые виды растений могут дать от 200 до 400 кг никеля с гектара.
Первые работы по гипераккумуляции золота появились в конце 1990-х годов. Согласно им, концентрация золота в горчице сарептской (Brassica juncea), произрастающей на руде с низким содержанием, достигала 39 г/т (по сухому весу). По сравнению с обычной концентрацией золота в растениях (менее 0,1 г/т) полученные результаты исследователей удивили. В природе существуют некоторые виды борщевиков (зонтичные), которые могут дать до 20 т материала в сухом весе с гектара. Корни этих растений проникают в грунт на глубину до 5 м, что позволяет очищать не только почву, но и воду.
В перспективе фитодобыча может быть полезна для тех районов, где ведется интенсивная промышленная и мелкомасштабная золотодобыча. Она может стать основой для возникновения нового привлекательного для кустарных добытчиков направления — добычи с помощью растений.
Фитодобыча имеет перспективы там, где почва недостаточно богата для выращивания сельскохозяйственных продуктов, но фактически может рассматриваться в качестве альтернативы, возможно даже более прибыльной, чем фермерство.
Тем не менее, несмотря на большой и еще нереализованный потенциал, прогресс в фитодобыче на сегодняшний день достаточно ограничен. Нишей «агродобычи» будет разработка низкокачественных, неудобных и расположенных у поверхности месторождений редких металлов.
Автор этих строк участвовал в программе по рекультивации земель, подвергшихся загрязнению в результате аварии на Чернобыльской АЭС. Задача состояла в том, чтобы посмотреть, насколько снизится уровень загрязнения различных видов почв в результате посева там определенных видов растений. Технология получилась простой и эффективной с неожиданным положительным побочным эффектом. На некоторых земельных участках весной были посеяны определенные виды растений. После того как растения (травы) выросли и созрели, их скосили и высушили на солнце. После высыхания растения (сено) скрутили в рулоны и сожгли в огромных бочках. На дне бочек осталась зола. Золу развели водой и центрифугировали в бакет-стаканах с коническим дном на центрифуге.
Под действием центробежного поля металлы и их окислы первыми оседали на дно стакана бакет-ротора. После центрифугирования раствора верхняя часть жидкости в виде золы сливалась и использовалась как сельскохозяйственное удобрение. Осадок из нижней части конического стакана бакет-ротора извлекался, сушился, прессовался и отправлялся на исследования. Содержимое осадка из нижней части бакет-стаканов некоторых исследуемых участков, помимо радионуклидов, содержало такое количество платиноидов и редкоземельных металлов среднетяжелой группы, что позволило говорить об их коммерчески выгодной добыче. Возможно, такая добыча рассеянных и редких металлов в скором времени станет основным способом их добычи.
Редкоземельные, рассеянные и редкие металлы
Одна из особенностей редкоземельных, рассеянных и редких металлов — они не являются относительно редкими, они более распространены, чем золото, уран, свинец, молибден, вольфрам и т. д. Однако крупных месторождений с концентрацией, пригодной для их промышленной разработки, очень немного. Они примерно равномерно распределены по поверхности Земли.
Главным поставщиком редкоземельных элементов на мировой рынок сейчас является Китай. Основным месторождением, откуда поставляются редкоземельные элементы, является гигантское железорудное месторождение Баян-Обо. Подавляющая часть редкоземельных руд Китая — это по сути глины. Содержание целевого сырья в них очень мало, в среднем 3–5 %, а сами глины рассредоточены по обширной территории. Промышленная переработка таких глин нерентабельна. И вот что придумали китайские товарищи: в многочисленные крестьянские дворы завозилась глина и необходимые реактивы. Крестьяне помещали глину в бочки, разводили водой и, размешивая палкой или мотором, добавляли в раствор сульфат натрия, затем фильтровали раствор. В конце засыпали в него щавелевую кислоту и собирали осадок солей редкоземельных элементов. Затем этот осадок за деньги сдавали на перерабатывающие фабрики. Там концентрат солей очищали от примесей и получали редкоземельные концентраты оксидов редкоземельных металлов. Продукт продают исключительно государству. На государственных предприятиях производится обработка концентрата на элементы уже на более высоком технологическом уровне. В настоящее время контроль за производством редкоземельных металлов, их распределением и продажей находится исключительно под контролем правительства Китая. Средняя цена концентрата редкоземельных металлов равна сегодня 45 долл/кг, а уже разделенные редкоземельные элементы стоят от 30 долл/кг для самария до 10 000 долл/кг для лютеция. В настоящее время добыча и получение редкоземельных металлов — процесс не только дорогой, но экологически очень грязный. При такой технологии получаются колоссальные объемы токсичных отходов. В Китае до настоящего времени за экологией не очень смотрели. Если раньше можно было отработанный раствор глины просто слить в канаву, то теперь это сделать достаточно трудно. Местность вокруг первичной «дворовой» переработки стала сильно токсичной. Китай превратился в почти полного монополиста по добыче, обогащению, первичной обработке, сепарации с получением индивидуальных редкоземельных элементов и конечных соединений. А в последние годы страна сама ощутимо увеличила использование редких металлов в собственных высокотехнологичных производствах.
КНР планирует ограничить или полностью прекратить вывоз редкоземельных металлов (РЗМ) за рубеж, объясняя свои намерения истощением ресурсов, нарушением экологии и возрастанием внутренних потребностей.
Редкие металлы — это стратегическое сырье для любой крупной экономики. Например, выделение плутония происходит с помощью фторида лантана. Гадолиний, эрбий, диспрозий и европий благодаря уникальной способности поглощать нейтроны добавляют в регулирующие стержни и в топливо для ядерных реакторов. Например, доли процента эрбия могут продлить срок службы топливных элементов на АЭС на несколько лет.
РЗМ незаменимы в металлургии. В результате микродобавок редкоземельных элементов многие сорта стали становятся хладостойкими, жаропрочными, гибкими, улучшается их устойчивость к коррозии. Без редкоземельных магнитов сегодня немыслимо почти ни одно электронное устройство.
Редкоземельные металлы (РЗМ) востребованы как катализаторы для оптимизации выделения из нефти светлых нефтепродуктов.
Установлена закономерность: чем «выше» технология, тем больше для ее применения нужно РЗМ. В общем, современное мировое сообщество все более и более нуждается в редкоземельных металлах. А где их взять, где и как добывать? Отказываться от достижений современной науки — солнечных батарей, мобильных телефонов и компьютеров — никто не собирается. Так что практически выход один: организовать добычу и производство РЗМ во всем мире на новом технологическом уровне, используя новое оборудование и технологии. Нужно найти новые экологически безопасные источники и способы добычи редкоземельных элементов.
Оборудование для новых технологий
Устройство человеческого глаза таково, что он не видит частицы размером менее одного микрометра. Поэтому вода с находящимися в ней микроскопическими или пылевидными частицами менее одного микрометра кажется для него абсолютно прозрачной (рис. 3).
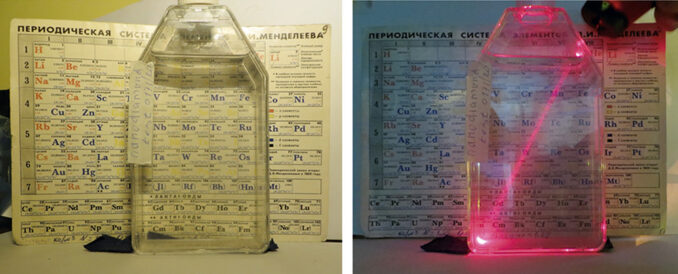
Начиная с древних времен люди (вспомним путешествие Одиссея за золотым руном на Кавказ) замечали, что весной, когда начинается таяние ледников и с гор начинают течь ручьи, при промывке овечьих шкур в этих ручьях шерсть покрывается тончайшими частицами золота. Как попадает золото в воду? Осенью в горах идут дожди, вода просачивается в золотоносные жилы. Зимой вода замерзает и, расширяясь, выдавливает на поверхность микроскопические частицы золота. Весной, когда начинают таять снег и лед, это золото вместе с талой водой стекает и попадает в горные ручьи. Зная этот факт, в более поздние времена люди пытались уловить частицы золота, используя мох, сухую траву, уголь и т. д. Однако эффективность этого метода оставляла желать лучшего.
Существующие ныне рудные отвалы, хвостохранилища обогатительных фабрик, зольношлаковые отвалы тепловых электростанций — это потенциальное сырье для добычи драгоценных и редкоземельных металлов. Вытекающая из этих техногенных отходов вода несет в себе то добро, что не получилось извлечь по технологиям прошлых веков.
Какое же оборудование нужно, чтобы эффективно и недорого добывать из воды эти мельчайшие частицы? Какой способ применить? Как обычно, помощь пришла из научных лабораторий.
В последнее время для нужд науки, медицины и промышленности понадобились наночастицы синтетических алмазов и углеродные нанотрубки определенных размеров. Перед разработчиками встала достаточно серьезная техническая задача по классификации этих частиц. Ведь создать сито для просеивания и разделения на фракции очень мелких и абразивных частиц практически невозможно. Тогда ученые и исследователи обратились к способу сепарации частиц, который называется жидкостной седиментацией. Что происходит с различными частицами металлов, когда они попадают в жидкость? Дело в том, что под действием искусственной гравитации во вращающихся жидких средах первыми на дно или стенку ротора осядут наиболее крупные частицы и частицы, имеющие высокую удельную плотность. Золото, платина, палладий и другие благородные и редкоземельные металлы, имеющие высокую удельную плотность, первыми осядут на стенку ротора или дно стакана, то есть идеально подходят для этого метода.
На одном из минских предприятий в рамках выполнения проекта по созданию центробежного оборудования для жидкостной седиментации природных и синтетических наноалмазов создано подобное оборудование. В общем виде установка
работает так: во вращающийся вертикальный цилиндрический проточный ротор сверху самотеком подается жидкость (центрифугат). Попадая во вращающуюся жидкостную среду, частицы металлов, минералов или окислов под действием центробежного поля (искусственной гравитации) устремляются на периферию и первыми оседают на вертикальную стенку ротора. Зная удельную плотность и размер нужных нам частиц, по формуле Стокса рассчитываем необходимое время для осаждения их на стенку ротора. Меняя переменные составляющие, а именно частоту вращения ротора (перегрузку) и объем подачи жидкости в ротор (центрифугат), можно добиться того, что на стенку ротора будут осаждаться частицы нужной плотности и размеров, а все остальное с потоком воды будет выводиться через нижние патрубки. По прошествии определенного времени, а это зависит от концентрации подаваемого в ротор центрифугата, установка останавливается, со стенок ротора снимается осадок, и центрифуга снова включается в работу. В конструкции установки принципиально отсутствует соединительная муфта, подающая центрифугат в ротор, поэтому на установке можно длительное время центрифугировать любые абразивные, металлосодержащие и химически активные жидкости. Техническое обслуживание установки сводится к минимуму (рис. 4).
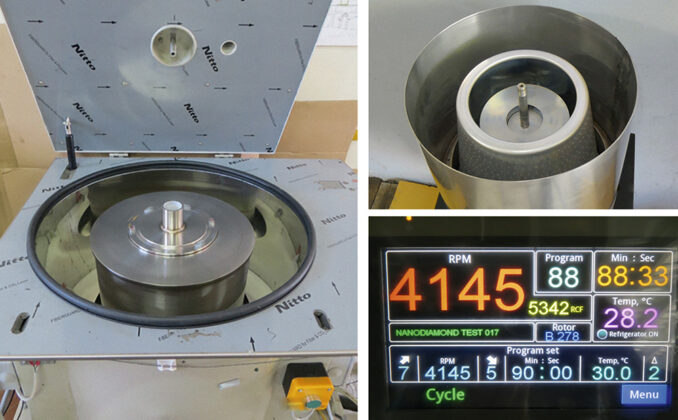
Созданием подобного оборудования и отработкой соответствующих технологий в настоящее время в мире занимаются только те промышленно развитые страны, в которых существуют инженерные школы соответствующего профиля и уровня компетентности.
Микролегирование металлов
Несколько десятилетий тому назад, в середине 80-х годов, автор этих строк учился на машиностроительном факультете одного из ленинградских, ныне санкт-петербургских, вузов. Преподаватель кафедры материаловедения Юрий Михайлович Аносов задал нам, студентам, казалось бы, простой вопрос: почему не ржавеют и не превращаются в окислы железа кованые решетки и ограды известных исторических памятников, крыши старинных зданий, построенные в XVIII и XIX веках? Ведь климат Санкт-Петербурга сырой, в городе огромное количество автомобилей и промышленных предприятий. Современные общепромышленные сорта стали не обладают такими антикоррозионными свойствами и без специального защитного покрытия быстро ржавеют. Но, по рассказам жестянщиков, ремонтирующих жестяные кровли, в Санкт-Петербурге есть еще много старинных зданий, крыши которых не ремонтировались с момента их постройки, а это XVIII и XIX века. Почему? Ведь первые коррозионностойкие нержавеющие стали были запатентованы и начали широко применяться только после 1913 года. Сталь, чтобы сопротивляться коррозии, должна содержать не менее 13 % хрома для обычных условий и не менее 18 % хрома для условий агрессивных сред. Так почему обычные кровельные крыши, железные кованые решетки и ограды зданий, мосты, путепроводы и другие старинные элементы стальных конструкций не ржавеют в сыром климате и сохранились в первозданном виде до настоящего времени (рис. 5)?
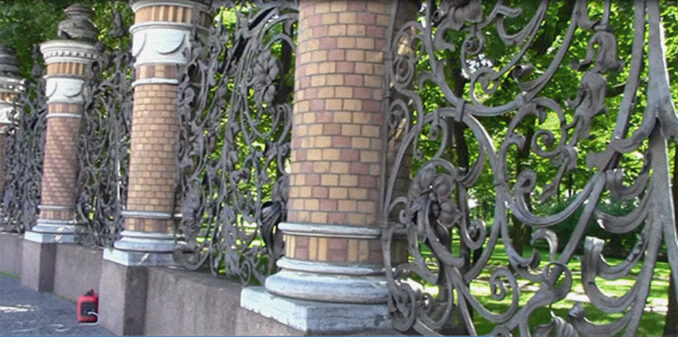
Все дело в том, что все вышеперечисленные и сохранившиеся до наших дней металлические артефакты выполнены в основном из сорта металла, который называется «Старый соболь» [10]. Данный сорт железа выпускался на уральских заводах, высоко ценился и хорошо продавался в европейских странах. В качестве топлива для выплавки и последующей механической обработки использовался древесный уголь. Древесный уголь, применявшийся для выплавки данного сорта железа, производился из твердых пород древесины сибирских лесов. Поскольку производство древесного угля (возгонка древесины без доступа кислорода) производилась в закрытых каменных печах, то какие-то микроэлементы металлов, которые деревья впитали из сибирских почв и сохранили в своих стволах, не испарились, а остались в древесном угле. Сибирская земля богата многими редкоземельными элементами, и поэтому пихты, лиственницы, сосны и кедры, произрастающие в определенных местах, накапливали эти элементы в своей древесине. В процессе выплавки и особенно в процессе ковки металла некоторое количество редкоземельных элементов естественным механическим способом перемещалось в железо. Это только сейчас, на основе последних открытий в области материаловедения, стало известно, что присутствие одной тысячной доли процента таких элементов, как технеций, рений, рутений, и некоторых других редкоземельных металлов в стали делает ее коррозионноустойчивой на долгие десятилетия. В те давние времена металлурги, кузнецы и ремесленники не знали этого, но замечали, что у одного поставщика железо не ржавеет, не растрескивается при нагрузке, хорошо куется, не ломается на морозе, а у другого точно такое по виду, но не имеет таких замечательных качеств. Поэтому предпочтение при строительстве особо значимых городских объектов, дворцов, соборов, государственных зданий и домов состоятельных граждан отдавалось хорошо зарекомендовавшим себя сортам металла.
Вот, к примеру, Смольный институт благородных девиц построен в конце XVIII века. Крыша, как и полагается зданиям такого назначения, была покрыта кровельным железом марки «Старый соболь». Крыша здания без каких-либо ремонтных работ успешно простояла до осени 1941 года. В результате бомбежек города самолетами немецко-фашистской авиации было повреждено около 40 % всей площади крыши. Надо напомнить, что в здании Смольного института в то время, да и сейчас находится городское управление Санкт-Петербурга. Поскольку город находился в блокаде более 900 дней, то крышу здания ремонтировали любыми подходящими кусками жести. После войны предпринимались попытки придать крыше аутентичный вид. Но найти кровельное железо, изготовленное по старинным технологиям, не удалось. Тогда было принято решение покрыть крышу здания обычным кровельным железом с последующими периодическими покрасками.
Или вот еще один яркий пример применения древних знаний и технологий. Шпиль Петропавловского собора в Санкт-Петербурге в настоящем виде был установлен в 1858 году. Сейчас это самое высокое сооружение города высотой 122 м. Внутренний силовой каркас шпиля выполнен из кованого железа. Простояв свыше 130 лет в сыром приморском климате безо всякого ремонта, он только в 1995 году из-за заклинивания флюгера подвергся осмотру. Внутренние железные конструкции каркаса шпиля оказались в достаточно хорошем состоянии. При этом надо учитывать, что ни покраска, ни какая-либо другая антикоррозионная обработка металлических конструкций каркаса шпиля никогда не производилась (рис. 6).
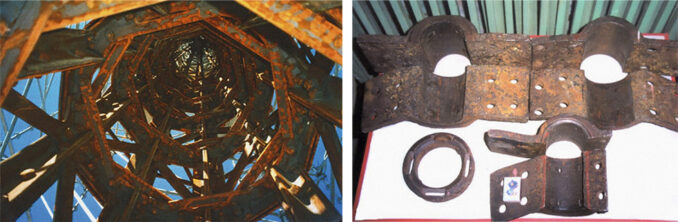
По сохранившимся оригинальным чертежам опорно-поворотного механизма флюгера из современных конструкционных сталей был изготовлен упорно-поворотный механизм. Однако, простояв всего семь лет и не выдержав нагрузок, в 2002 году механизм заклинил. Осмотр заклинившего механизма показал, что некоторые детали упорно-поворотного механизма флюгера, изготовленные из современных сталей, не выдержали нагрузок и растрескались. Почему? Анализ проблемы очевиден: все дело в качестве металла.
В настоящее время в мире выплавляется около 2 млрд т стали в год. Ежегодные мировые потери от коррозии металла оцениваются около 2 трлн долл. Промышленно развитые страны теряют в год от 2 до 3 % валового внутреннего продукта из-за потерь, связанных с коррозией. В США среднегодовые потери из-за проблем, связанных с коррозией металлов, составляют более 400 млрд долл. Примерно четверть этих потерь можно было избежать, если использовать более коррозионностойкие материалы. Мировая цена одной тонны общепромышленной стали составляет сейчас около 500 долл/т, а цена хрома сейчас — более 20 000 долл/т. Напомню, что концентрация хрома в стали, чтобы сталь сопротивлялась коррозии, должна быть в пределах 13–18 %. Следовательно, цена только хрома в одной тонне нержавеющей стали должна составлять более трех четвертей стоимости. А что если рассмотреть возможность использования современных технологий по микролегированию сталей и сплавов? Известно, что добавление всего от 0,001 до 0,003 % некоторых редких металлов делает сталь коррозионноустойчивой, холодоустойчивой с улучшенными физико-химическими свойствами. Во многих технологически развитых странах сейчас ведутся обширные исследования по созданию специальных сортов сталей и других современных материалов с использованием технологий микролегирования редкоземельными и редкими металлами. Определяется, какие элементы, в каком количестве, на какой стадии производства и каким способом нужно ввести в основной металл, чтобы повысить его жаропрочность, пластичность, конструкционную долговечность, износостойкость и другие необходимые свойства.
Редкоземельные элементы вследствие своей высокой химической активности, попав в основной металл, нейтрализуют вредное воздействие кислорода, серы, фосфора, кремния и прочих нежелательных элементов. Редкоземельные металлы, как поверхностно-активные элементы, располагаются на поверхностях раздела фаз (границах зерен металлов), упрочняют их поверхность и задерживают развитие в них диффузионных процессов. Редкоземельные элементы оказывают весьма положительное влияние на структурную стабильность как стальных сплавов, так и сплавов из цветных металлов. Так, добавка всего двух-трех десятых процента скандия в алюминиевые термонеупрочняемые сплавы повышает предел прочности и текучести сплавов более чем на треть (рис. 7).
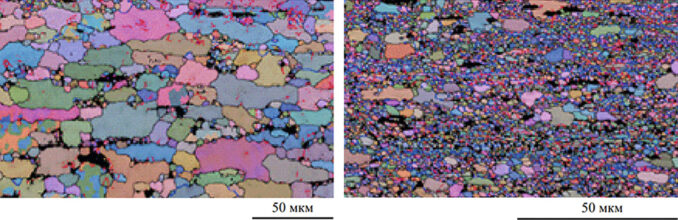
Введение в стальные жаропрочные стали микродобавок церия, рения, рутения, лантана, неодима повышает их конструкционную долговечность в 3–4 раза. При выплавке высококачественных конструкционных и авиационных сталей добавки редкоземельных металлов измельчают зерно стали, связывают серу, фосфор, кремний и другие вредные примеси, придавая сталям необходимую твердость, вязкость, упругость, износостойкость. При производстве труб больших диаметров для перекачки нефти и газа используется технология микролегирования стали. В России для улучшения физико-химических показателей трубопроводной стали добавляется около 8 г ниобия на 1 т. В странах ЕС и Японии эта добавка составляет около 40 г/т.
Булатная сталь
Из истории известно несколько сортов сталей, которые имеют технические характеристики, сопоставимые с современными сортами и даже превосходящие их. Дамасская сталь и булат — одна из самых интересных и загадочных страниц в истории металлургии. Впервые европейцы познакомились с булатом (булат — индо-иранское «пулат» — литая сталь) при столкновении армии Александра Македонского с войсками индийского царя Пора. Особенно поразил македонцев панцирь захваченного в плен царя. Он был сделан из необыкновенно прочного белого металла — булата. Из булата были изготовлены и широкие индийские мечи, которые легко рассекали пополам македонское железо. Мечи могли иметь узор, напоминающий рисунок ткани. А свойствами клинки обладали действительно удивительными. Будучи твердыми и прочными, они одновременно обладали большой упругостью и вязкостью. Клинки перерубали железные гвозди и в то же время свободно сгибались в дугу. Лезвие булатного клинка можно было заточить до почти неправдоподобной остроты. Такое возможно лишь тогда, когда сталь обладает одновременно высокой твердостью, вязкостью и упругостью. Булатная сабля легко сгибалась на 90–120 градусов, не ломаясь. Есть сведения, будто настоящий булатный клинок носили вместо пояса, обматывая им талию.
Слитки индийского литого булата wootz привозились в Сирию, где в городе Дамаске из них выковывали клинки. Знаменитая дамасская сталь с узорами получалась путем многократных проковок пучка из стальных прутков разной твердости. Качество клинков из сварной дамасской стали было по тем временам тоже очень высокое, но такого сочетания прочности и упругости и остроты, как в оружии из литого индийского булата, сирийским кузнецам добиться не удавалось.
Со временем секрет выплавки индийского железа был утерян. Уже в конце XII века клинки из литого булата высшего качества не могли делать ни в Индии, ни в Сирии, ни в Персии. Производство холодного оружия высшего качества везде пришло в упадок, и секрет производства литого булата был окончательно потерян (возможно, из-за отсутствия определенного качества древесных углей и заготовок из индийского железа).
Не одно столетие металлурги всех стран и народов пытались выплавить булатную сталь. Но получить литой булат, не уступающий по свойствам индийскому, однажды удалось только начальнику уральских златоустовских заводов П. П. Аносову в 40-х годах XIX века. Сохранившийся до наших дней старинный аносовский булатный клинок легко перерубает кованые гвозди, гнется в дугу и на лету рассекает газовый платок. Секрет древних индийских мастеров открыт? Скорее нет, чем да. После смерти П. П. Аносова, несмотря на оставленную им подробную технологию, воспроизвести литой булат такого качества не удается никому!
Современные специальные качественные легированные стали превосходят булат по отдельным показателям прочности, упругости, режущим свойствам, но добиться таких выдающихся свойств в одном образце пока не удается. Тайна индийского литого булата ждет своей разгадки! Возможно, в старинных сортах сталей присутствуют микродобавки каких-то легирующих элементов, о которых современная наука пока не знает? Но где их взять, как добыть в достаточных количествах, сколько они будут стоить, какие инновационные технологии применить? Население планеты растет, и потребность в металлах увеличивается, а известные ныне места их добычи во многом исчерпаны.
Источники пополнения и способы добычи
Известно, что в морях и океанах в растворенном виде находится около 10 млрд т золота и других благородных и редких металлов. Примерно такое же количество содержится в речных и подземных водах.
При добыче так называемой тяжелой и сверхтяжелой нефти плотностью более 1 000 кг/м3 в попутной пластовой воде содержится более 50 различных металлов, таких как рений, скандий, европий, серебро, золото, платина, палладий и т. д. Эти пластовые воды можно использовать в качестве технологического сырья. По оценкам независимых экспертов, стоимость металлов в этих водах сопоставима, а иногда и превышает стоимость самой нефти. Важным преимуществом подземных вод как сырьевого источника редких элементов является низкая себестоимость их добычи и постоянство химического состава. Организация добычи редкоземельных и благородных металлов из подземных пластовых вод не требует больших капиталовложений. Ведь не нужно производить вскрытие залежей, организовывать транспортировку, измельчение, промывку и т. д. Достаточно иметь оборудование, которое могло бы осаждать из воды мельчайшие, невидимые глазу частицы нужных металлов или окислов.
Какой способ и какую технологию нужно использовать, чтобы экономически эффективно извлечь из этих вод необходимые нам металлы? Существует несколько способов и технологий. Рассмотрим только два из них: мембранный и центробежный способы выделения как наиболее подходящие для данной задачи. Наиболее эффективным и экономически перспективным видится центробежный способ жидкостной седиментации. Если вспомнить историю создания подобного оборудования для разделения изотопов урана 235 и 238 и сравнить производственные и экономические показатели, то центробежная технология окажется более предпочтительной. В США для разделения изотопов урана использовался газодиффузионный способ разделения, а в СССР — центробежный.
Газодиффузионный способ — это продавливание газа (гексафторида урана) через мембраны с очень мелкими отверстиями. Советский Союз вначале тоже использовал этот способ, но затем отказался в пользу центробежной технологии разделения как наиболее рентабельной. При участии германских инженеров М. Штейнбека и Г. Циппе с 1946 по 1954 год была создана промышленная центробежная технология по разделению изотопов урана. Центробежный способ осаждения и выделения из газовых и жидких сред микро-, субмикро- и наночастиц в настоящее время является наиболее простым и экономически целесообразным. Если для этих целей удастся использовать простые, недорогие и надежные проточные центрифуги, то задача по разделению и выделению из водных сред определенных групп металлов и их окислов будет решена. Ведь удельное потребление электроэнергии при центробежном способе разделения примерно в 20 раз меньше, чем при диффузионном. При газодиффузионной технологии более 80 % стоимости конечного продукта составляет стоимость электроэнергии.
В настоящее время в России проводятся некоторые опыты по извлечению редкоземельных и драгоценных металлов при помощи ионообменных смол, но этот способ достаточно дорогой и малоэффективный.
Возможно, данная информация заинтересует людей, проживающих в местах, где они ходят буквально по несметным богатствам природы и нет способа и оборудования для того, чтобы взять это богатство.
Список литературы
1. Украинцева В. В. 2002. Растительность и климат Сибири эпохи мамонта // Труды Государственного биосферного заповедника «Таймырский». Вып. 4. Красноярск, http://ashipunov.info/shipunov/school/books/ukraintseva2002_rastit_klimat_sibiri_epokhi_mamonta.djvu
2. Chytrý M. et al. 2019. A modern analogue of the Pleistocene steppe-tundra ecosystem in southern Siberia // Boreas. Vol. 48. P. 36–56 https://onlinelibrary.wiley.com/doi/pdf/10.1111/bor.12338.
3. Морель Жан Луи, Симонно Мари-Одиль, Эчеваррия Гийом, Энтони ван дер Энт Бейкер, Алан Дж. М. Выводы и перспективы на добычу полезных ископаемых. Агрохимия: сельское хозяйство для металлов: извлечение нетрадиционных ресурсов из растений // Под ред. Энтони ван дер Энта, Алана Дж. М. Бейкера, Гийома Эчеваррии, Мари-Одиль Симонно и Жана Луи Мореля. Швейцария: Springer International Publishing. 2020. С. 485–489.
4. Нкрума Филип Н., Эчеваррия Гийом, Эрскин Питер Д. и ван дер Энт Антоний. Фитодобыча: использование растений для извлечения ценных металлов из минерализованных отходов и нерентабельных ресурсов // Под ред. Мартина Дж. Клиффорда, Роберта К. Перронса, Салима Х. Али и Тима А. Грайса. Бока-Ратон. Флорида, США: CRC Press Taylor & Francis Group. 2018. С. 313–324.
5. Крюков В. А., Яценко В. А., Крюков Я. В. Горная промышленность № 5 / 2020. С. 68–84. Источник: https://mining-media.ru/ru/article/newtech/16121-redkozemel-naya-promyshlennost-realizovat
6. Goodenough K. M., Wall F., Merriman D. The Rare Earth Elements: Demand, Global Resources, and Challenges for Resourcing Future Generations. Natural Resources Research. 2018. 27(2): 201–216. DOI: 10.1007/s11053-017-9336-5.
7. Wübbeke Jt. Rare earth elements in China: Policies and narratives of reinventing an industry. Resources Policy. 2013.38(3): 384–394. DOI: 10.1016/j.resourpol.2013.05.005.
8. Schulz K. J., DeYoung J. H. Jr., Seal R. R. II, Bradley D. C. (eds) Critical mineral resources of the United States – Economic and environmental geology and prospects for future supply. U.S. Geological Survey. Reston (VA); 2017. DOI: 10.3133/pp1802.
9. Венецкий С. И. О редких и рассеянных. Рассказы о металлах. Металлургия, 1981. 184 с.
10. Мезенин Н. А. Занимательно о железе. М., Металлургия, 1972. С. 58–61.
11. Боровков А. И., Пальмов В. А. Прикладная механика и реконструкция шпиля Петропавловского собора. Часть 1. История Петропавловского собора. Конструкция шпиля и ангела // Научно-технические ведомости СПбГПУ. СПб.: Изд. СПбГПУ. 2003. № 1. 19–47. WWW.FEA.RU.
12. Гуревич Ю. Г. Загадка булатного узора. — Знание, 1982.
13. Аносов П. П. Собрание сочинений. — М.: Изд-во АН СССР. 1954.
14. Антеин А. К. Дамасская сталь в странах бассейна Балтийского моря. — Рига: Зинатне, 1973.
15. Вах Е. А., Вах А. С., Харитонова H. A. Редкоземельные элементы в породах и водах Березитивого месторождения / Материалы 24-й Всероссийской конференции «Строение литосферы и геодинамика». — Иркутск, 2011. С. 133–134.
16. Научно-экспериментальная база атомной промышленности зарубежных стран. Справочник. Под ред. Круглова А. К., Смирнова Ю. В. — М.: Энергоиздат, 1987.
17. Zippe Gernot. «Historical review on the development of gas centrifuges for uranium enrichment», in «Sixth workshop proceedings» of Conf. «Separation Phenomena in Liquids and Gases». Nagoya University, Japan, 1998.