Прокопьев Сергей Амперович, к. т. н., Институт земной коры СО РАН, ООО НПК «Спирит» (г. Иркутск)
Гладкочуб Дмитрий Петрович, д. г-м. н., Институт земной коры СО РАН, член-корреспондент РАН
Основные направления совершенствования схем обогащения железорудного сырья сфокусированы на повышении качества концентратов, снижении удельных затрат на обогащение и повышении комплексности использования сырья [1].
Анализ работы большинства крупных железорудных предприятий России и ближнего зарубежья позволил выделить следующие проблемы, с которыми сталкиваются недропользователи при переработке железосодержащего сырья:
1. Потери немагнитного железа с отвальными хвостами.
На большинстве месторождений, отрабатываемых в настоящее время, в значительном количестве присутствуют немагнитные минералы железа, в частности гематит. Однако ввиду того, что в основном железоперерабатывающие предприятия работают с применением технологии мокрой магнитной сепарации (ММС), практически все слабомагнитные железосодержащие минералы уходят в хвосты.
По этой же причине не перерабатываются окисленные железные руды, основными ценными компонентами которых являются гидроксиды железа (также слабомагнитные), — они складируются в огромных объемах в отвалы.
2. Большие циркулирующие нагрузки в циклах измельчения и классификации.
Классическая схема обогащения железных руд включает в себя 2–3-стадиальное измельчение материала (нередко до крупности 90–95 % класса -0,044 мм) и одну-две операции магнитной сепарации после каждой стадии измельчения. Задача магнитной сепарации сводится к максимальному извлечению в магнитный продукт железосодержащих минералов и получению отвальных хвостов. Конечный концентрат получают лишь в последней стадии магнитной сепарации.
Такое построение схемы обогащения приводит к тому, что огромное количество фактически готового концентрата в форме полностью раскрытых зерен магнетита перетекает из одной стадии обогащения в другую [2], а циркуляция в циклах измельчения и классификации нередко превышает 300 %.
Значительные циркулирующие нагрузки и отсутствие возможности вывода готового концентрата на ранних стадиях обогащения, с одной стороны, являются причиной образования значительного количества железосодержащих шламов, которые практически в полном объеме попадают в хвосты обогащения, т. к. известно, что при измельчении магнетита до крупности менее 0,02 мм магнитная восприимчивость частиц резко снижается. С другой стороны, высокие циркулирующие нагрузки приводят к снижению производительности мельниц по исходному питанию и к существенному возрастанию затрат электроэнергии.
Основной причиной такого положения является неудовлетворительная работа классифицирующего оборудования — спиральных классификаторов и гидроциклонов в замкнутых циклах измельчения. Проблема заключается в том, что и классификаторы, и гидроциклоны не обеспечивают эффективного разделения материала по крупности, т. к. они одновременно делят его и по плотности. Например, частицы кварца крупностью 0,3 мм двигаются в гидроциклоне с той же скоростью и по тем же траекториям, что и частицы магнетита крупностью 0,06 мм. Вследствие этого легкие и более крупные сростки уходят в слив и остаются в магнетитовом концентрате, а свободные тяжелые зерна магнетита попадают в пески и возвращаются на повторное измельчение («эффект удельного веса») в эту же стадию. То же самое происходит при классификации в спиральных классификаторах: раскрытый магнетит осаждается на дно ванны классификатора и возвращается в мельницу.
3. Рядовые по качеству концентраты.
Качество концентрата, поступающего на металлургический передел, в значительной мере определяет технико-экономические показатели металлургического производства и, соответственно, конкурентоспособность производителя на рынке сбыта продукции, поэтому повышение качества концентратов является весьма актуальной задачей.
Повышение качества железорудных концентратов имеет также экологический аспект. Увеличение массовой доли железа в концентрате приводит к снижению отходов металлургического производства (шлаков, пылей, шламов). Снижаются объем вредных выбросов в атмосферу и площадь земли, выделяемой под техногенные отходы (шлаковые отвалы, шламохранилища) [1].
В настоящее время железосодержащие концентраты, получаемые при переработке руды практически всех месторождений РФ и ближнего зарубежья, в основном содержат порядка 64–68 % железа общего, что не является максимально возможным показателем.
На протяжении многих десятилетий научные организации и производственные предприятия проводят работы по исследованию возможности улучшения показателей обогащения железорудного сырья: извлечению гематита, повышению качества концентрата, оптимизации схем обогащения и пр. Проведено огромное количество работ с использованием методов флотации, высокоинтенсивной магнитной сепарации, тонкого грохочения, магнитно-гравитационной сепарации и пр., однако в каждом из указанных методов недропользователи отмечают и негативные для производства аспекты: высокие эксплуатационные затраты и применение вредных для окружающей среды реагентов (флотация), низкая эффективность грохочения по мелким классам крупности (тонкое грохочение), сложность подготовительных процессов и эксплуатации (магнитно-гравитационная сепарация) и пр.
Суммируя вышесказанное, можно заключить, что на территории РФ и ближнего зарубежья на сегодняшний день отсутствует оптимальная технология, эффективно решающая вопросы совершенствования схем обогащения железосодержащих руд. Об этом свидетельствует и практика переработки руд, т. к. единичные случаи внедрения отдельных видов оборудования не решают поставленных задач.
Эффективное и экологически чистое решение проблем
Одним из наиболее экономичных, экологичных и перспективных методов усовершенствования традиционных схем переработки железорудного сырья является винтовая сепарация, которая применяется самостоятельно или в комбинированных схемах в сочетании с магнитной сепарацией, флотацией или другими методами обогащения [3, 4, 5].
У магнетита и гематита имеется один общий признак разделения — плотность, у магнетита она составляет — 4,9–5,2 г/см3, у гематита — 4,0–5,3 г/см3 (рис. 1). У минералов пустой породы, обычно представленных силикатами, кварцем, карбонатами, плотность составляет 2,5–2,8 г/см3. Разница в плотностях магнетита и гематита, с одной стороны, и вмещающих минералов, с другой стороны, в среднем составляет 2,2–2,5 г/см3. Этот фактор является определяющим при решении вопроса использования гравитационных методов обогащения, в т. ч. винтовой сепарации при обогащении железорудного сырья.
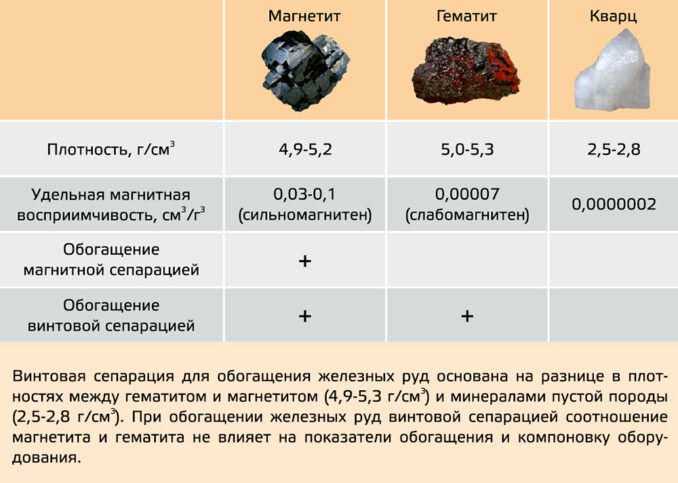
Винтовые сепараторы представляют собой устройства, реализующие принцип разделения материала в наклонном безнапорном водном потоке малой глубины. Основным их рабочим органом является неподвижный наклонный желоб, имеющий форму спирали, закрученной вокруг вертикальной оси. Подготовленный к обогащению материал (по крупности, производительности и плотности пульпы) подается в верхнюю часть желоба винтового сепаратора. При прохождении пульпы по аппарату происходит распределение материала по поверхности желоба: тяжелые минералы сосредотачиваются у внутреннего борта, сростки двигаются в средней части желоба, а легкие — у внешнего борта (рис. 2), т. е., установив соответствующим образом отсекатели продуктов обогащения, можно получать концентраты с содержанием железа общего до 71 %. Разгрузка продуктов обогащения производится в конце желоба.
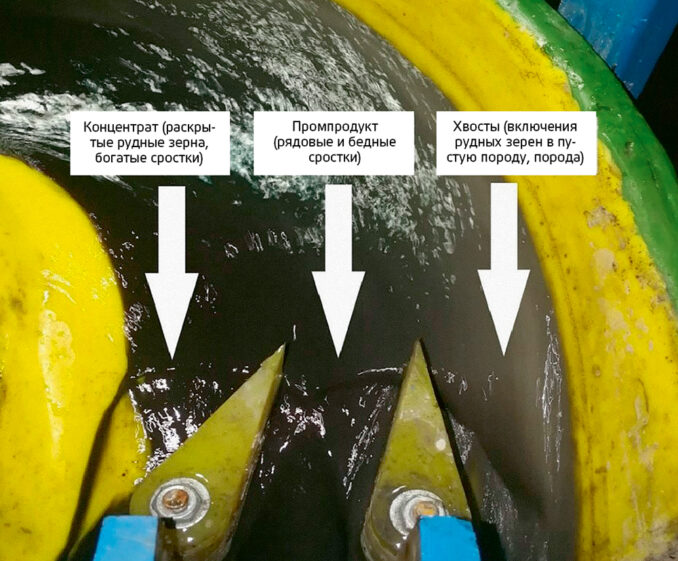
В конструкции винтовых сепараторов отсутствуют движущиеся и вращающиеся части, им не требуется подача электроэнергии. Данные аппараты стабильно работают на оборотной воде. Процесс обогащения на винтовых сепараторах наблюдается визуально и поэтому легко поддается регулированию.
Винтовая сепарация характеризуется эффективным обогащением материала шламовой крупности до 0,02 мм, возможностью обогащать сырье (рудное, россыпное, техногенное) как на предварительных стадиях обогащения с получением коллективных концентратов, так и в перечистных и доводочных операциях [6].
Включение винтовой сепарации в схему обогащения железных руд обеспечит решение одновременно несколько задач:
1. Извлечение гематита совместно с магнетитом в концентрат, т. е. комплексное использование минерального сырья.
2. Получение высококачественного концентрата.
3. Снижение эксплуатационных затрат на обогащение.
Для получения максимального эффекта от винтовой сепарации необходимо решить принципиальные вопросы.
Во-первых, признать, что винтовая сепарация является основным методом обогащения при переработке железных руд, а не вспомогательным, для решения локальных вопросов. Магнитную сепарацию следует рассматривать как контрольную операцию на конечных стадиях технологических схем.
Во-вторых, применить стадиальный вывод готового концентрата начиная с первой стадии измельчения.
Схемы обогащения железорудного сырья, разработанные десятки лет назад, основанные на магнитном методе обогащения и построенные по принципу стадиального выделения отвальных хвостов с получением готового концентрата только в последней операции, не отвечают современным вызовам, с которыми сталкивается недропользователь XXI века. Данные схемы обогащения были применимы и успешно работали на богатом сырье и были спроектированы исходя из необходимости унификации оборудования. Фактически на данный момент необходимо пересмотреть всю концепцию обогащения железных руд РФ и ближнего зарубежья. Реализация проектов модернизации действующих производств возможна с максимальным использованием имеющегося оборудования путем строительства цехов винтовой сепарации.
Применение винтовых сепараторов за рубежом
Винтовая сепарация широко применяется при обогащении железных руд за рубежом. Всемирно известная фирма Roche Mining — производитель обогатительного оборудования и в том числе винтовых сепараторов — за всю историю своего существования изготовила и продала более 25 тысяч винтовых аппаратов, и из этого количества более 22 % — для предприятий по обогащению железных руд Канады, Австралии, Бразилии.
За рубежом наиболее распространены схемы, в которых предусмотрена одна основная винтовая сепарация с одной-двумя стадиями перечистки концентрата. Хвосты винтовой сепарации после измельчения направляют на магнитную сепарацию.
В ближнем зарубежье также отмечены факты включения винтовой сепарации в схему обогащения железорудного сырья в качестве одной из основных операций обогащения. Так, на АО «Южный ГОК» (г. Кривой Рог, Украина) внедрены винтовые сепараторы производства ООО НПК «Спирит» (рис. 3, 4) для выделения высококачественного железорудного концентрата из межцикловых операций. Содержание железа общего в концентрате винтовых сепараторов составляет не менее 69 %. Немаловажным фактором является снижение циркулирующих нагрузок и переошламования магнетита.

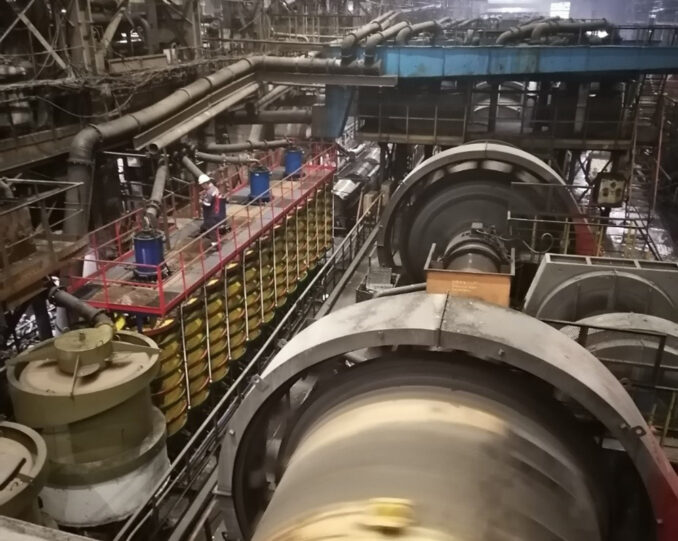
Пример возможного применения винтовой сепарации
В ходе многолетних исследований, проведенных ООО НПК «Спирит» совместно с ИЗК СО РАН, выявлено, что оптимальной точкой внедрения винтовой сепарации является слив мельницы I стадии измельчения.
Надо вспомнить классическое правило, сформулированное Г. О. Чечоттом, — «не дробить ничего лишнего», т. е. в данном случае необходимо выводить из процесса зерна железосодержащих минералов по мере их раскрытия для исключения переизмельчения.
Работы, проведенные ООО НПК «Спирит» на таких крупнейших железоперерабатывающих предприятиях, как Стойленский [7], Михайловский [2], Оленегорский ГОКи и др., показывают возможность доизвлечения к основному объему магнетитового концентрата от 5 до 10 % гематитового концентрата.
Рассмотрим вариант узла первой стадии измельчения (рис. 5). На мельницу поступает исходное питание производительностью 1 100 т/час. Со сливом классификатора выходит 1 100 т/час. В мельницу возвращается 1 000 т/час, т. е. циркуляция составляет около 90 %. Загрузка мельницы составляет 2 100 т/час.
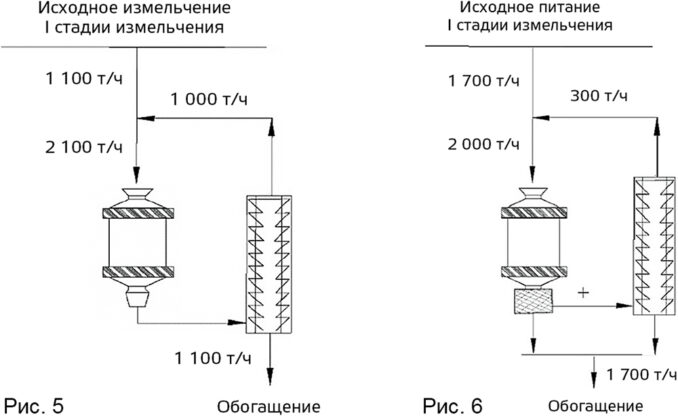
В процессе многочисленных исследований выявлено, что в сливе мельницы присутствуют раскрытые зерна магнетита и гематита. Соответственно, логично их вывести в готовый концентрат. С учетом того, что в сливе мельницы присутствует крупный материал, необходимо произвести рассев по классу крупности 1,25 (1,5) мм. Применение барабанного грохота, установленного на корпусе мельницы, или дуговых грохотов, расположенных в цехе винтовой сепарации, обеспечит минимизацию затрат на данный процесс.
Материал крупностью менее 1,25 мм после грохочения поступает на винтовую сепарацию, а надрешетный продукт возвращается на доизмельчение. В этом случае циркулирующая нагрузка снижается на 700 т/час — с 1 000 т/час до 300 т/час (рис. 6).
Предлагаемый вариант модернизации производства позволит:
1. Повысить производительность обогатительной фабрики не менее чем на 25 % без ввода дополнительного оборудования.
2. Улучшить качество помола.
3. При сохранении производительности: значительно сократить эксплуатационные затраты производства.
Испытания винтовой сепарации на Стойленском ГОКе показали возможность получения качественного железорудного концентрата уже после I стадии измельчения — 66,1 %. Совместно с магнетитом в концентрат выделялся гематит (около 5 % к объему магнетита, рис. 7). Необходимо отметить, что при обогащении слива мельницы I стадии измельчения материал не был раскрыт в полной мере — основная часть магнетита и гематита осталась в сростках. В связи с чем можно прогнозировать значительное увеличение количества гематита при обогащении материала методом винтовой сепарации после следующих стадий измельчения.
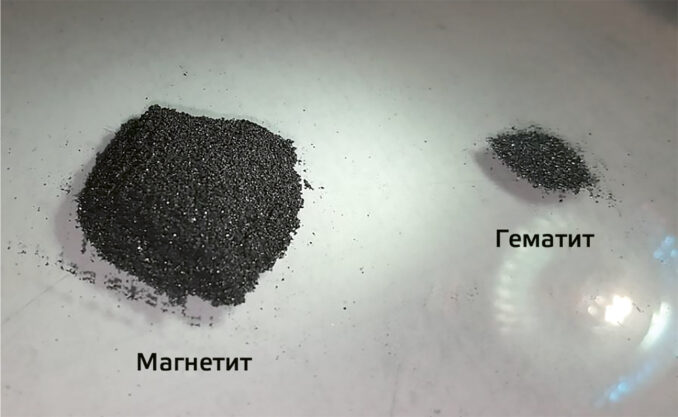
При проведении испытаний винтовой сепарации на продуктах второй и третьей стадий обогащения была показана возможность получения высококачественного концентрата с содержанием железа общего 70 %.
Обогащение окисленных железистых кварцитов
Вовлечение в переработку окисленных кварцитов является актуальной задачей: огромные массы окисленных руд не перерабатываются и складируются в отвалах. Проведенные испытания по применению винтовой сепарации для обогащения окисленных железистых кварцитов Стойленского месторождения показали возможность получения высококачественного концентрата с содержанием железа общего 69 % (рис. 8, 9).
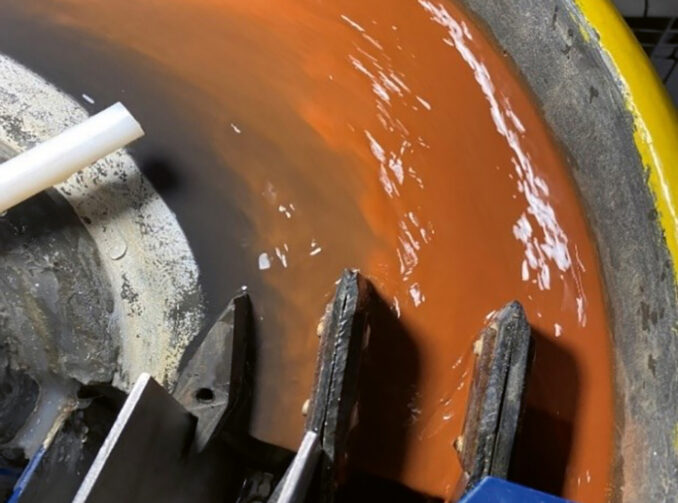
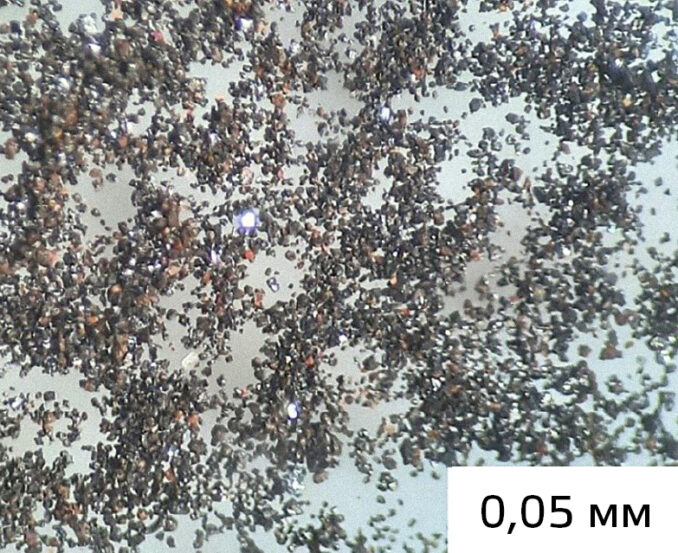
Переработка текущих хвостов
На протяжении 2006–2008 гг. ООО НПК «Спирит» проводило исследования возможности извлечения гематита из текущих хвостов
Михайловского ГОКа, ООО УК «Металлоинвест» (рис. 10). Гематит в отвальных хвостах данного предприятия характеризуется очень тонкой вкрапленностью, полное раскрытие происходит в классе крупности менее 0,04 мм.
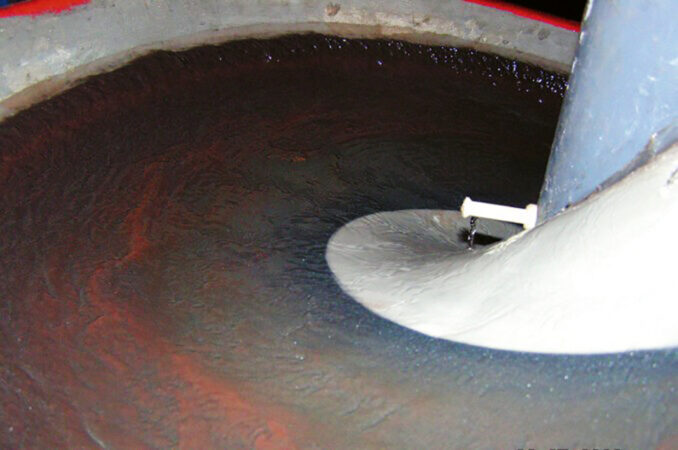
Лабораторные и промышленные испытания технологии винтовой сепарации показали возможность получения гематитсодержащего концентрата с содержанием железа общего 63,6 %, с выходом 10,9 % от исходных хвостов ММС при извлечении 27 %.
Реализация проекта по извлечению гематита из текущих хвостов методом винтовой сепарации позволит получить дополнительную продукцию в объеме около 10 % к основному объему товарной продукции Михайловского ГОКа, при этом себестоимость гематитового концентрата ожидается минимальной.
Извлечение железа из гидроотвалов углеобогатительных фабрик
Весьма актуальным вопросом на сегодняшний день для угледобывающей промышленности является переработка гидроотвалов углеобогатительных фабрик, которые относятся к I группе техногенных месторождений углесодержащего сырья. Объемы гидроотвалов составляют сотни миллионов тонн. Вовлечение в переработку шламов из гидроотвала поможет решить проблему ресурсосбережения, охраны недр, рационального использования недр и защиты окружающей среды [8]. Существующие методы переработки шламов гидроотвалов основываются на флотационном обогащении, однако данный метод является энергозатратным и оказывает негативное воздействие на окружающую среду ввиду значительного потребления реагентов. Для успешной и рентабельной переработки гидроотвалов углеобогатительных фабрик необходимы специальные технологии, основанные на экологически чистых способах обогащения техногенного сырья.
Лабораторные исследования по обогащению шламов гидроотвала одной из углеобогатительных фабрик Сибирского федерального округа РФ методом винтовой сепарации, проведенные ИЗК СО РАН и выполненные в рамках комплексного научно-технического проекта Министерства науки и высшего образования Российской Федерации, № 075-15-2022-1192 «Переработка хвостов угольных обогатительных фабрик с целью получения товарного угольного концентрата» при поддержке комплексной научно-технической программы полного инновационного цикла «Разработка и внедрение комплекса технологий в областях разведки и добычи твердых полезных ископаемых, обеспечения промышленной безопасности, биоремедиации, создания новых продуктов глубокой переработки угольного сырья при последовательном снижении экологической нагрузки на окружающую среду и рис-ков для жизни населения», утвержденной распоряжением Правительства Российской Федерации № 1144-р от 11 мая 2022 г., показали возможность получения железосодержащего концентрата, пригодного для применения в металлургической промышленности или использования в тяжелосредной сепарации для обогащения угля [9].
В настоящее время ООО НПК «Спирит» отработана технология выделения железа из текущих хвостов ТЭЦ, на рис. 11 представлен общий вид установки, успешно работающей на одной из ТЭЦ Иркутской области; на данный момент совместно с ИЗК СО РАН проводятся подготовительные работы к промышленным испытаниям возможности извлечения железа из гидроотвалов углеобогатительных фабрик.
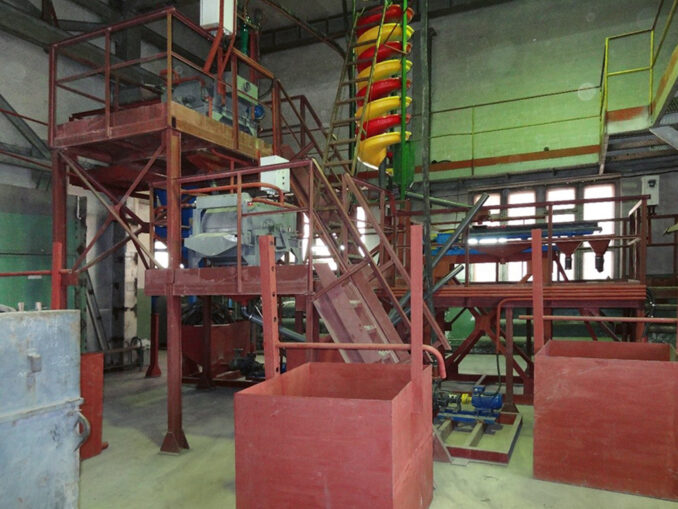
Заключение
Настало время изменить веками устоявшуюся в России и ближнем зарубежье ассоциацию «железо — магнит» и сильные традиции, сложившиеся в железодобывающей отрасли. Модернизация схем обогащения с использованием винтовой сепарации в качестве одного из основных методов обогащения существенно повысит технико-экономические показатели металлургического производства и, соответственно, конкурентоспособность производителей на отечественном и международном рынках сбыта продукции.
Источники:
1. Пелевин А. Е. Пути повышения эффективности технологии обогащения железорудного сырья // Бюллетень «Черная металлургия», 2019. — Том 75. — С. 137–146.
2. Прокопьев С. А. Технология стадиального выделения магнетитового концентрата с помощью винтовой сепарации: дис. на соиск. уч. степ. канд. техн. наук: 25.00.13: защищена 30.05.2019 / Прокопьев Сергей Амперович. — Екатеринбург. — 2019. — 161 с.
3. Емельянова К. К., Турецкая Н. Ю., Прокопьев С. А., Прокопьев Е. С., Чикишева Т. А. Перспективы применения винтовой сепарации на Абагурской обогатительно-агломерационной фабрике с целью получения качественных концентратов после первой стадии измельчения // Материалы международной конференции «Современные проблемы комплексной и глубокой переработки минерального сырья природного и техногенного происхождения» (Плаксинские чтения — 2022, ДВФУ. — Владивосток, 2022. — С. 269–271.
4. Иванов В. Д., Прокопьев С. А. Винтовые аппараты для обогащения руд и песков в России: Монография. — М: — Дакси. — 2000. — 239 с.
5. Берт Р. О. Технология гравитационного обогащения / Р. О. Берт — М.: Недра. — 1974. — 572 с.
6. Прокопьев С. А. Особенности массопереноса на винтовых сепараторах / С. А. Прокопьев, А. Е. Пелевин, Ю. П. Морозов // Известия вузов. Горный журнал. — 2018. — № 7. — С. 67–74.
7. Прокопьев С. А., Прокопьев Е. С., Емельянова К. К., Напольских С. А. Получение высококачественного магнетит-гематитового железорудного концентрата методом винтовой сепарации // Горный журнал. — 2021. — № 6. — С. 86–90. DOI: 10.17580 / gzh.2021.06.07.
8. Петров Е. И., Тетенькин Д. Д. Государственный доклад о состоянии и использовании минерально-сырьевых ресурсов Российской Федерации в 2020 году // М., 2021. — С. 69–91.
9. Турецкая Н. Ю., Чикишева Т. А. Обогащение шламов угольных гидроотвалов методом винтовой сепарации. Науки о Земле и недропользование. 2022. — № 45(4). — С. 436–445. https://doi.org/10.21285/2686-9993-2022-45-4-436-445