В 2019 году на обогатительной фабрике самого северного в России производителя железорудного сырья было внедрено несколько автоматизированных систем управления производством и запущен тестовый проект по вибродиагностике сушильного комплекса. В 2020 году Оленегорский ГОК (АО «Олкон»), входящий в состав «Северстали», планирует вводить новые системы автоматизации, покупать современное оборудование для лабораторий и создавать сеть Wi-Fi на своих карьерах.
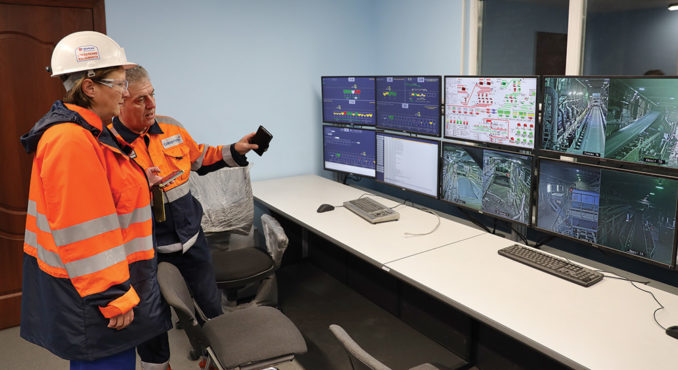
АО «Олкон» не раз становилось первопроходцем в отечественной переработке железной руды. Предприятие в числе первых в России освоило технологию обогащения бедных железистых кварцитов в промышленных масштабах. Сегодня компания продолжает активно внедрять новые технологии, чтобы повысить эффективность и безопасность добычи и переработки железных руд.
Автоматизация дробления
На участке дробления руды и породы дробильно-обогатительной фабрики «Олкона» введена в эксплуатацию автоматизированная система управления разгрузочными тележками. Пять разгрузочных тележек пяти конвейеров участка дробления руды и породы работают в автоматическом режиме. Рабочее место оператора конвейеров автоматизировано.
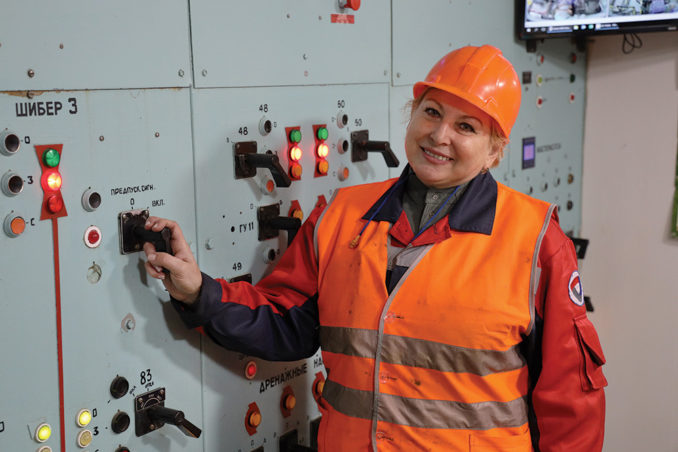
Благодаря внедрению нового оборудования необходимые уровни загрузки бункеров поддерживаются автоматически. Система сама «решает», какой бункер наполнять, где снимать нагрузку, а где увеличивать.
Видеокамеры, установленные в голове и хвосте каждого конвейера, «следят» за материалом на ленте и заполнением бункеров. Система видеонаблюдения передает информацию на пять мониторов. На четырех визуализируются данные о текущем состоянии, что позволяет быстро менять режимы работы при необходимости. Пятый монитор входит в систему диспетчеризации фабрики.

У оператора есть возможность получать все сведения в реальном времени и быстро вносить коррективы, после чего система выбирает решения, куда направить тележку, до какого уровня загружать бункер и так далее.
Система максимально помогает оператору, выдавая предупреждения, например об аварийных ситуациях. Кроме того, на сервере сохраняется весь архив событий и действий оператора.
В результате ввода автоматизированной системы управлением тележками теперь занимается один сотрудник, а не четыре, как раньше. Улучшились условия и безопасность труда, поскольку человеку больше не требуется находиться рядом с конвейером. Высвободившиеся работники направлены на переобучение, чтобы подготовить специалистов для участка обогащения, где внедряются магнитно-гравитационные и винтовые сепараторы.
Плавный запуск насосов
Управление землесосами на предприятии тоже автоматизировано. В 2019 году в пульпонасосной 1А установлена автоматизированная система.
Инвестиционный проект помог решить сразу несколько проблем, многие годы осложнявших работу участка хвостового хозяйства. Снижен расход электроэнергии.
Главное преимущество новой системы — насосы могут запускаться плавно, передача на сеть стала безударной, выполняются подхват от сети, остановка и регулировка скорости семи землесосов в пульпонасосной, которые транспортируют хвосты (отходы производства железорудного концентрата) в хвостохранилище.
Ранее из-за значительного сечения труб на трубопроводах (700–1 000 мм) и больших расстояний, на которые прокачивается пульпа, при запуске и остановке оборудования возникали гидроудары. Это приводило к порывам трубопроводов, выходу из строя оборудования, износу деталей и узлов. Высокое содержание твердой составляющей в хвостах не позволяло всегда запускать насосы с первого раза.
Внедрение системы автоматизации было технически сложным. Во-первых, насосы, перекачивающие хвосты на 5—7 км, непросто запускать и останавливать, управлять ими было невозможно. Во-вторых, насосы располагаются последовательно без задвижек и запоров, а участок всаса погружен в зумпф и имеет п-образную форму.
В рамках проекта на «Олконе» впервые в России установлено инновационное оборудование — комплектные распределительные устройства с элегазовой изоляцией. В отличие от прежних ячеек, они компактны, в них нет выкатных элементов и доступных токоведущих частей. В течение всего срока эксплуатации (30–50 лет) не предполагается никакого дополнительного обслуживания.
Также в проекте использован современный силовой кабель с изоляцией из сшитого полиэтилена. Он безопаснее, чем кабели других марок, обладает высокой пропускной способностью, более устойчив к воздействию окружающей среды.
Управление стихией
Автоматизация коснулась нескольких направлений работы компании, в том числе буровзрывных работ. Сейчас взрывники «Олкона» осваивают новую компьютерную программу автоматизированного проектирования буровзрывных работ I-Blast.
Программный продукт дорабатывается под условия предприятия, что объясняется наличием у комбината шести карьеров. Каждый обладает своими особенностями. Свойства породы и руд отличаются по составу, твердости и другим характеристикам.
По словам разработчиков, программа способна обеспечить эффективность и точность работы, автоматизировать трудоемкие процессы расчета различных данных. Создание цифровой модели блока на взрывание позволяет рассчитать размер сетки, расход взрывчатых веществ, развал горной массы, ее разлет и фрагментацию, сейсмически опасные зоны.
Также программа позволяет более рационально просчитывать параметры сетки скважин, что сделает более рациональным расход взрывчатых веществ, повысит качество взрывов.
Новое ПО даст возможность симулировать буровзрывные работы: современный промышленный взрыв уже давно стал управляемой стихией. За счет определенной последовательности соединения скважин системой Exsel с различным временем замедления взрывники получают заданный порядок инициирования зарядов. Поскважинное замедленное взрывание зарядов взрывчатых веществ на массовом взрыве обеспечивает требуемую направленность его действия. В программе I-Blast можно просчитать последовательность взрывания каждой скважины, распределить энергию взрыва с учетом твердости массива.
С ее внедрением проектировщики буровзрывных работ смогут подбирать параметры сетки скважин, зарядов, способов инициирования. Это приведет к получению требуемой кусковатости и оптимальным удельным показателям.
Профилактика внеплановых остановок
В октябре 2019-го в «Олконе» запущено тестирование системы вибродиагностики SPM Instrument на сушильном комплексе дробильно-обогатительной фабрики. Система предназначена для ведения постоянного мониторинга технического состояния оборудования сушильного барабана в режиме онлайн.
Установлены датчики на два двигателя, подшипниковые опоры, редукторы. Часть датчиков контролирует смещение барабана, чтобы свести к минимуму риски отказа оборудования, обеспечить надежность его работы. Более 50 датчиков контролируют состояние узлов и агрегатов сушильного барабана. В случае выявления отклонений измеряемых параметров от установленных пороговых значений система вибродиагностики оповещает технологический и ремонтный персонал.
С начала сезона система зафиксировала более шести потенциальных отказов оборудования. В каждом случае ремонтники фабрики имели возможность подготовиться и устранить выявленные дефекты в плановые остановки. Например, осенью заменен один из электродвигателей привода сушильного барабана, дважды произведена обтяжка анкерных болтов крепления опоры подвенцовой шестерни. Своевременная диагностика позволила избежать серьезных поломок и длительных простоев оборудования.
Система разработки компании SPM Instrument выбрана для тестирования не случайно, поскольку одной из особенностей сушильного комплекса на «Олконе» является низкая скорость вращения барабана. Не каждая система может работать на таком небольшом количестве оборотов.
Применяемые в системе алгоритмы и инструменты анализа вибрационных параметров фиксируют малейшие изменения в состоянии контролируемого оборудования. Так, в январе 2020 года система диагностики зафиксировала превышение порогового значения по общему уровню вибрации электродвигателя левого привода сушильного барабана. Этот параметр взят под особый контроль. Анализируя тренды вибрации, специалисты выявили положительную динамику в развитии неисправности. Поэтому было принято решение заменить электродвигатель во время планового ремонта.
Эксперты ЧерМК ежеквартально проводят дополнительные виброобследования оборудования сушильного барабана с помощью переносных приборов. Это требуется в связи с недостаточным количеством статистических данных для точной настройки системы.
В 2020 году специалисты компании просчитают, какое оборудование необходимо снабдить подобными системами. Рассматривается вопрос об установке датчиков на дробильном комплексе с крутонаклонным конвейером в Оленегорском карьере.
Выявление опасных очагов
Чтобы сделать работу на предприятии более безопасной для людей, в начале октября 2019 года на «Олконе» запущен проект «Безопасная среда». Его участники, рабочие предприятия, за три месяца выявили 321 опасный очаг на территориях подразделений.
Преимущество проекта в том, что сотрудники сами замечают опасные условия, способные привести к травме или ЧП. Информация сразу передается руководителю участка. Он в свою очередь обязан разработать корректирующие мероприятия, назначить ответственного за устранение опасностей и определить сроки реализации мероприятий. В большинстве случаев опасности устраняются сразу.
Сообщить об очаге можно, оформив бумажный бланк или отправив СМС на выделенный номер телефона. Главное — указать характер опасности, табельный номер и подразделение. За каждую выявленную опасность сотруднику начисляется 0,1 балла, стоимость которого составляет 100 рублей. Накопленные баллы можно обменять на сертификат.
Работать полярной ночью стало безопаснее
Еще один важный шаг к созданию безопасной производственной среды в компании — установка пробной системы Red Kill Zone на три новых экскаватора (два ЭКГ-15 и один ЭКГ-12). Комплекс специальных прожекторов, размещенных по периметру машины, выделяет красным светом допустимую границу приближения к нему работающих в связке большегрузных автосамосвалов и автомобилей ремонтных служб.
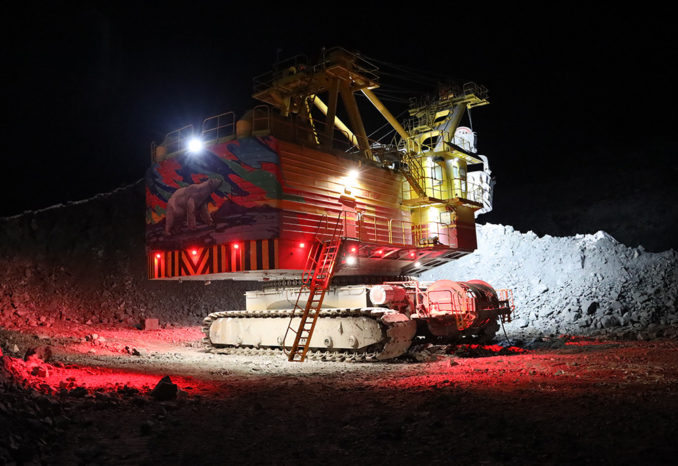
Систему используют на экскаваторах, которые грузят машины на два подъезда, то есть слева и справа. Водитель из кабины машины хорошо видит зону, куда заезжать уже опасно.
Современная визуальная система безопасности в темное время суток обозначает территорию в 30 м вокруг работающего экскаватора, а также обеспечивает безопасное размещение техники в зоне погрузки. Это значительно повышает уровень безопасности работы в забоях во время полярной ночи.
В 2020 году на «Олконе» продолжится работа по внедрению цифровых технологий на всех этапах производства.
На дробильно-обогатительной фабрике будет расширен парк измерительного оборудования за счет автоматизированной системы управления технологическими процессами. С ее помощью планируется повысить эффективность благодаря снижению потерь в процессах обогащения концентрата, уменьшения потребления мазута на сушильном комплексе, оптимизации затрат на переделах дробления и обогащения. Пока не хватает информации по химическому составу руды, ее фракциям, по химическому составу концентрата и его гранулометрическому составу и другим параметрам. Система обеспечения данными в режиме on-line позволит решить эти и другие вопросы.
Сейчас ведутся расчеты, какие приборы необходимы для получения более детального анализа продукции. Рассматривается возможность приобретения современного оборудования для лабораторий службы контроля качества на всех переделах производства концентрата.
В планах компании модернизация сети передачи данных ГТК «Карьер», для чего будет внедряться сеть Wi-Fi на карьерах Оленегорский, Кировогорский, Восточный.
Для исключения попадания недробимых предметов в дробилки планируется использовать технологию «компьютерного зрения». В качестве эксперимента над конвейером установят инфракрасные камеры, которые будут определять недробимые предметы, что исключит остановки оборудования из-за срабатывания металлоискателя на руду.