Вопреки вызовам 2020 года, «Металлоинвест» сохранил производственную программу на высоком уровне. Объем выпуска базового продукта компании — железной руды — составил 40,4 млн т, что на 0,5 % больше показателя прошлого года. Производство стали увеличилось почти до 5 млн т в результате завершения в 2019 году реконструкции и горячих испытаний электропечей по технологии FMF на «Уральской Стали». Доля продукции с высокой добавленной стоимостью в общем объёме отгрузки ЖРС сохранилась на уровне 72 %.
Знаковыми событиями 2020 года стали запуск на Михайловском ГОКе им. А. В. Варичева уникального дробильно-конвейерного комплекса и начало производства премиальных окатышей под металлизацию.
ОСКОЛЬСКИЙ ЭЛЕКТРОМЕТАЛЛУРГИЧЕСКИЙ КОМБИНАТ ИМЕНИ А. А. УГАРОВА
Единственное в России металлургическое предприятие полного цикла, где реализованы технология прямого восстановления железа и плавка в электропечах, позволяющих получать металл, практически свободный от вредных примесей и остаточных элементов.
Шары для мельниц
Оскольский электрометаллургический комбинат расширяет свою продуктовую линейку: предприятие запустило выпуск стальныx мелющих шаров для горнорудных предприятий «Металлоинвеста».
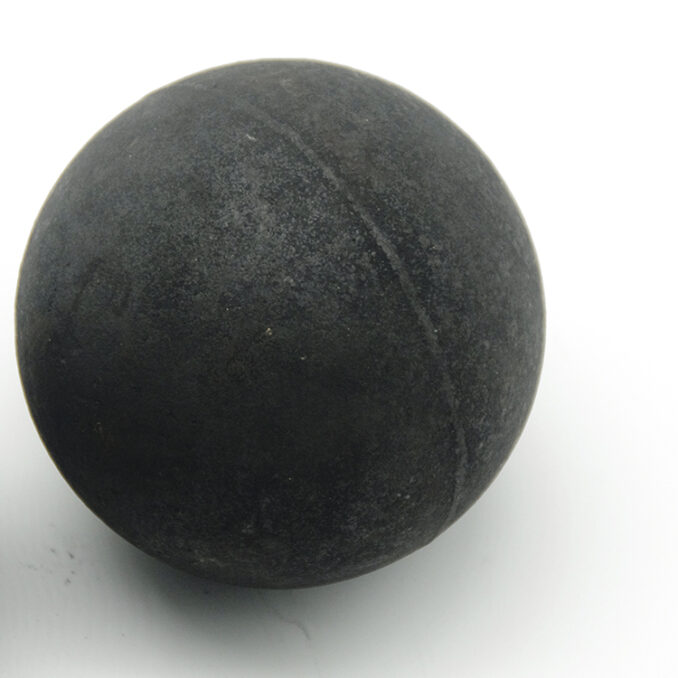
В середине августа на ОЭМК началось холодное опробование оборудования шаропрокатного стана, к строительству которого приступили в сентябре прошлого года. На Лебединском и Михайловском ГОКах мелющие шары используются для измельчения до порошкообразного состояния руды, идущей на производство железорудного концентрата. Шаропрокатный стан — один из важнейших инвестиционных проектов «Металлоинвеста», реализация которого позволила повысить эффективность деятельности горнорудных предприятий компании. Кроме того, ввод в эксплуатацию собственного производства мелющих шаров снизил зависимость компании от поставщиков этой продукции.
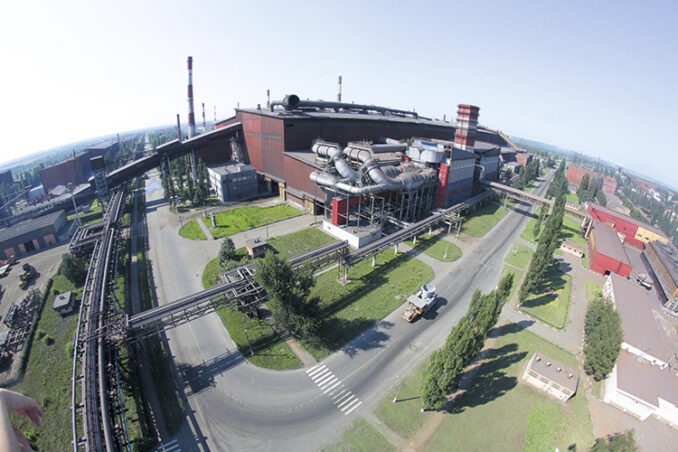
Проектная мощность стана — 43 тыс. т стальных мелющих шаров в год диаметром 100–120 мм, массой 4,6 и 8 кг и группой твердости 2–3 в соответствии c ГОСТ 7524-2015. Контракт на поставку оборудования был заключен с китайской компанией WISDRI, а инвестиции в реализацию масш-табного проекта составили около 1 млрд руб. Новое производство позволило создать на комбинате дополнительно 85 рабочих мест.
«Запуск шаропрокатного стана — важная веха в развитии компании, — заявил первый заместитель генерального директора — директор по производству УК «Металлоинвест» Андрей Угаров. — Новый стан исключит зависимость наших горнодобывающих предприятий от внешних поставщиков. В перспективе мы сможем предложить мелющие шары производства ОЭМК и другим горно-металлургическим предприятиям».
«Это важный проект с точки зрения синергетического эффекта для предприятий «Металлоинвеста», — отметил управляющий директор ОЭМК им. А. А. Угарова Сергей Шишковец. — Переход на мелющие шары производства ОЭМК снизит себестоимость железорудного сырья Лебединского и Михайловского комбинатов за счет оптимизации логистики поставок, снижения транспортных расходов и гарантированного качества продукции».
Следующим шагом для нас станет расширение сортамента с учетом потребностей рынка. Данный проект уникален тем, что для нагрева заготовки используется современная индукционная установка, требующая очень точной и жесткой настройки, ведь, проходя через нее в течение двух-трех минут, металл будет разогреваться до 1 250 градусов. Большое значение имеют качество и химический состав воды, используемой для охлаждения индуктора. Шаропрокатный стан включает в себя склад исходной заготовки, куда железнодорожным транспортом поступает металл из первого сортопрокатного цеха, автоматический загрузочный стенд с установкой плазменной резки, откуда заготовка поступает в индукционную установку нагрева. Проходя через валки рабочей клети стана, она прокатывается в шары заданного размера. Всего на пусковом объекте смонтировано более 300 т оборудования. Самая тяжелая часть — 46-тонная рабочая клеть шаропрокатного стана. Монтаж клети был одним из важнейших этапов работ, который позволил определить ось прокатки технологической линии стана. Это непременное условие правильной работы всего оборудования и получения качественной продукции.
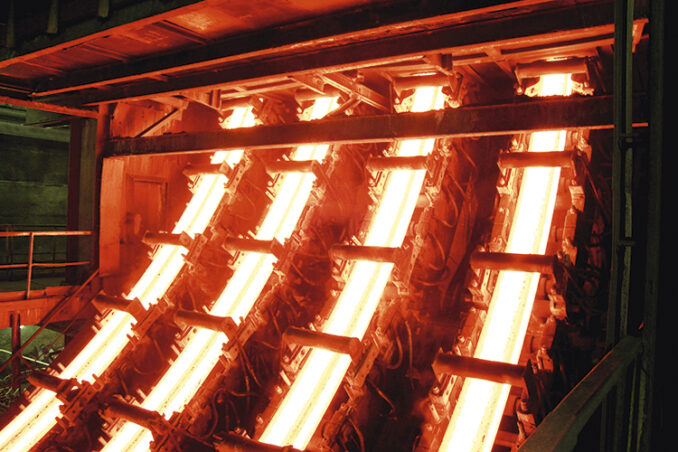
На шаг впереди
На рынке стального проката растёт конкуренция. Требования клиентов становятся более жёсткими. Чтобы выигрывать в конкурентной борьбе, «Металлоинвест» совершенствует технологии, разрабатывает новые марки стали.
Особое место в портфеле продукции компании занимает высококачественный сортовой прокат SBQ, производимый ОЭМК. На предприятии ежегодно разрабатываются десятки новых марок стали для российских предприятий и потребителей из Европы. Не менее важно предоставить заказчику те сервисы, в которых он нуждается. Так, ОЭМК обладает уникальными производственными мощностями по отделке проката. В цехе отделки проката (ЦОП) стальные прутки, произведенные на стане 350 в сортопрокатном цехе, обрабатываются в соответствии с точно заданными параметрами. В 2017 году на ОЭМК запущен редукционно-калибровочный блок (РКБ) в среднесортной линии прокатного стана 350, позволяющий производить стальной прокат высокой точности по геометрическим размерам (допуск по диаметру ±0,15–0,2 мм) без необходимости дополнительной отделки в ЦОП.
SBQ (Special Bar Quality) — в Европе такой продукт называют «инженерная сталь», а в Северной Америке — «сортовая сталь особого качества». Целый ряд изделий из инженерной стали подвергается дополнительной обработке, прежде чем обрести окончательный вид. К применяемым процессам относятся термообработка, механическая обработка и подготовка поверхности. В результате продукт приобретает необходимые эксплуатационные характеристики, такие как обрабатываемость, пластичность, прочность, твердость, способность противостоять деформационным и ударным нагрузкам. На производство высококачественного сортового проката SBQ приходится около четверти всей выпускаемой стальной продукции «Металлоинвеста». В 2017 году «Металлоинвест» запустил комплексную программу повышения клиентоориентированности и качества SBQ, в рамках которой проводятся модернизация мощностей ОЭМК, дальнейшее расширение сортамента SBQ и развитие системы продаж. В 2020 году компания завершила на ОЭМК строительство участка термообработки горячекатаного проката производительностью 70 тыс. т в год, инвестиции в проект составили около 3 млрд руб. Создание новых мощностей позволит «Металлоинвесту» увеличить объем продаж премиальной продукции и укрепить свои позиции на рынке SBQ. Новый участок позволит проводить различные виды термообработки в широком диапазоне температуры 400–980 °C для получения высококачественного проката с определенной микроструктурой. В основе качества SBQ ОЭМК лежит выплавляемая на предприятии сталь с узким диапазоном химического состава, низким содержанием газов, вредных примесей, повышенной прочностью и пластичностью, повышенной обрабатываемостью резанием. Такие показатели достигаются за счет использования чистой первородной шихты. ОЭМК — уникальный комбинат, единственный в России, на котором реализована цепочка прямого восстановления железа, то есть производство металлизованных окатышей из железорудного концентрата с последующей плавкой окатышей в электропечах. На предприятии нет стадии выплавки чугуна из железорудного концентрата в доменной печи с дальнейшей переплавкой в сталь. Контракт на поставку оборудования для участка термообработки был заключен с Danieli Centro Combustion, входящей в группу компаний Danieli, которая является ведущим итальянским производителем оборудования для металлургической промышленности. «Металлоинвест» успешно инвестировал в улучшение качества, продуктивность, эффективность и развитие мощностей по производству SBQ на ОЭМК.
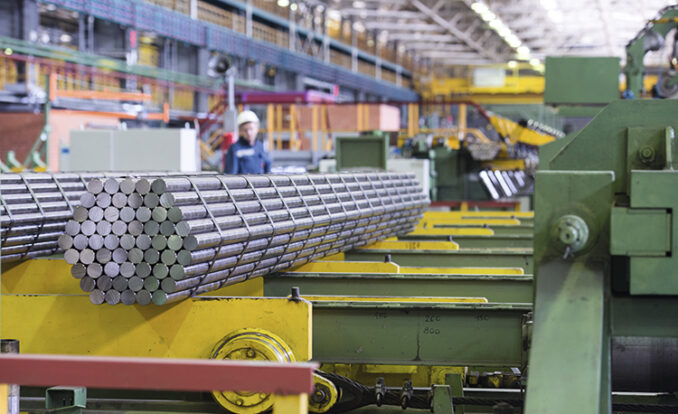
Повышая эффективность производства
В условиях жесткой рыночной конкуренции компания сосредоточена на улучшении качества стальной продукции, включая sbq и качественную катанку (QWR), на ОЭМК им. А. А. Угарова.
Один из ключевых инвестиционных проектов «Металлоинвеста», завершенных в 2020 году, — техническое перевооружение машины непрерывного литья заготовок № 3 (МНЛЗ № 3) на Оскольском электрометаллургическом комбинате — направлен на повышение качества проката. Инвестиции «Металлоинвеста» в техническое перевооружение МНЛЗ № 3 составили около 1 млрд руб. На сегодняшний день МНЛЗ № 3 является уникальной — на машине внедрены практически все инновационные решения в области разливки стали. Они позволили значительно улучшить внутреннюю структуру и качество поверхности производимой заготовки.
«Техническое перевооружение МНЛЗ № 3 — один из ключевых инвестиционных проектов программы повышения клиентоориентированности и качества SBQ, — прокомментировал первый заместитель генерального директора — директор по производству УК «Металлоинвест» Андрей Угаров. — Новая машина позволит повысить качество непрерывнолитой заготовки до уровня, необходимого для производства проката SBQ, используемого в автомобилестроении и подшипниковой промышленности.
В ходе технического перевооружения были заменены основные узлы и механизмы МНЛЗ № 3. Установлены системы электромагнитного перемешивания, удаления грата с заготовок, гидравлический механизм качания кристаллизатора и шиберные затворы промежуточных ковшей с подачей аргона, модернизирована зона вторичного охлаждения и система автоматизации. Но главное — это тянуще-правильная машина с семью модулями обжатия на каждом ручье, или так называемая система мягкого обжатия. Непрерывнолитая заготовка имеет неоднородную внутреннюю структуру, и исправить такие дефекты, как осевая пористость или осевая рыхлость, сделать структуру металла более однородной сможет новое оборудование, которым в ходе реконструкции была оснащена МНЛЗ № 3. Постепенное увеличение давления на каждом из семи модулей системы «мягкого обжатия» позволит обжимать заготовки до 24 мм от исходного размера, тем самым увеличивая плотность и однородность литой структуры. Поставщиком основного технологического оборудования выступила компания INTECO (Австрия). В ноябре-декабре 2019 года были проведены холодные и горячие испытания машины, а в январе-феврале прошлого года — испытания на подтверждение гарантийных показателей. В начале марта 2020 года машина была введена в эксплуатацию.
МИХАЙЛОВСКИЙ ГОРНО-ОБОГАТИТЕЛЬНЫЙ КОМБИНАТ ИМЕНИ А. В. ВАРИЧЕВА
Михайловский ГОК имени А. В. Варичева является одним из крупнейших в России и СНГ предприятий по добыче и обогащению железной руды. Предприятие ведёт открытым способом разработку железорудного месторождения.
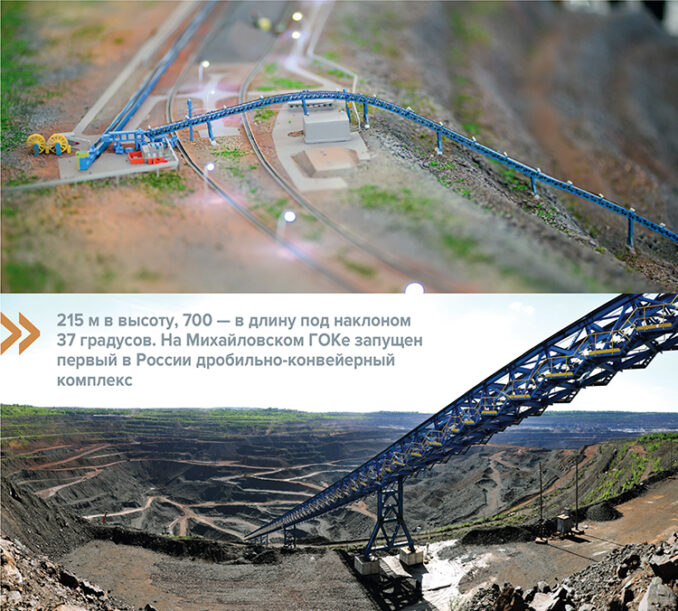
Производство, не отходя от карьера
«Металлоинвест» запустил дробильно-конвейерный комплекс на Михайловском гоке им. А. В. Варичева.
Компания «Металлоинвест» реализует уникальные для нашей страны проекты, выполняя задачи по повышению эффективности, объемов производства и качества продукции. Одним из них является дробильно-конвейерный комплекс (ДКК) производительностью 15 млн т руды в год, возведенный в юго-восточной части карьера Михайловского ГОКа. ДКК — самый важный и масштабный проект компании «Металлоинвест» сегодня. Он оптимизирует транспортную схему карьера и сокращает затраты на доставку горной массы.
Комплекс является частью масштабной программы, направленной на развитие производственных мощностей и радикальное повышение качества продукции Михайловского ГОКа им. А. В. Варичева. Ровная голубая лента, рассекающая борт карьера снизу-вверх по всей его высоте, — уникальный для нашей страны крутонаклонный конвейер. Этот «лифт для руды» перемещает свыше 72 тыс. т горной массы в сутки с нижних горизонтов на самый верх. Построить такое грандиозное сооружение на борту карьера — вызов возможностям человека: здесь нужны опыт, мастерство и смелость в принятии нестандартных решений. Судите сами: угол наклона конвейера — 37 градусов, высота подъема — 215 м. На склоне борта смонтированы не только опоры и секции, но и навесное оборудование, площадки и ограждения, кабельные трассы, системы водоснабжения и пожаротушения. Плюс принципиально новая для комбината канатная дорога для доставки на дробильно-перегрузочную установку технического персонала, ремонтных бригад и запасных частей. Она будет подниматься с нижних горизонтов на борт карьера и обратно за четыре минуты.
ДКК осуществляет дробление неокисленных железистых кварцитов на нижних горизонтах и транспортирование их на борт карьера. В состав комплекса входит более 40 объектов. Это дробильно-перегрузочная установка, бортовой крутонаклонный конвейер, промежуточный конвейер, погрузочно-складской комплекс, а также объекты инженерно-технического обеспечения. Дробильно-перегрузочная установка (ДПУ) расположена у подножия крутонаклонного конвейера. Она состоит из надземной части и пяти подземных технологических этажей.
«Дробильно-перегрузочную установку можно смело назвать уникальной: это капитальное здание с размером подземной части 45 м, полностью отсыпанное скальной массой. Высота надземной части — 30 м. Аналогов подобного сооружения нет ни в одном российском карьере, — рассказывает руководитель проекта Вадим Конюхов. — ДПУ — это примерно три пятиэтажки, поставленные друг на друга. Она предназначена для приемки руды, доставляемой большегрузными самосвалами, и измельчения ее в двух стадиях дробления: одной дробилкой крупного и двумя среднего дробления — до тех пор, пока исходные куски в 1 200 мм не уменьшатся до 150 мм».
При строительстве комплекса было уложено 35,5 тыс. куб. м бетона, смонтировано более 2 тыс. т металлоконструкций и более 4 тыс. т оборудования. Сегодня он вызывает неподдельный интерес у каждого, кто увидел его впервые, впечатляет своим масштабом, красотой и смелостью конструкторской и инженерной мысли. На необходимости возведения его в карьере МГОКа настоял безвременно ушедший из жизни генеральный директор УК «Металлоинвест» Андрей Варичев. Он твердо верил в осуществление этой смелой идеи. И своей уверенностью заряжал всех остальных.
«Андрей Владимирович никогда не боялся самых сложных задач и всегда добивался их эффективного решения, — говорит Вадим Конюхов. — Благодаря ему мы воплотили задуманное в жизнь и запустили комплекс в текущем году. В активной стадии реализация второго этапа проекта — строительство дробильно-конвейерного комплекса в центральной части карьера, производительность которого составит 35 млн т руды в год. Завершить его планируется в 2023 году».
Окатышей будет больше
В конструкции обжиговой машины № 3 (ОМ-3), запущенной в 2015 году на Михайловском ГОКе имени А. В. Варичева, были реализованы передовые технологические решения.
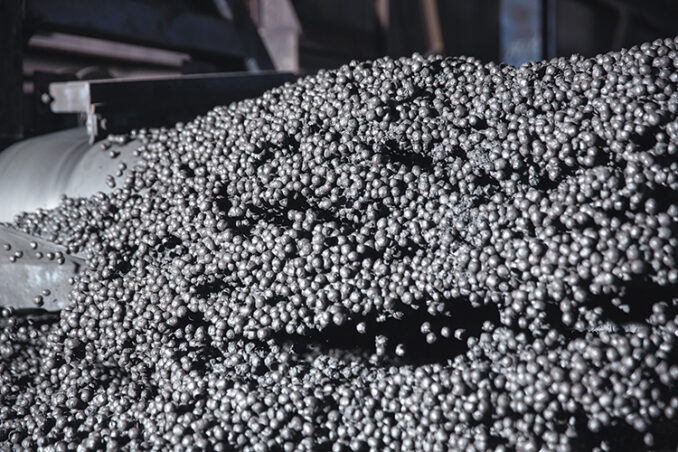
Обжиговую машину отличали самые современные параметры: высокая удельная производительность, гибкость в производстве различного вида окатышей, высокая степень газоочистки — до 98 %. Нормы потребления энергоресурсов, электроэнергии и газа — на уровне лучших мировых практик. Как показало время, даже такую современную и эффективную машину можно усовершенствовать. Реконструкция была продиктована необходимостью увеличения объёмов производства и повышения качества продукции.
«Модернизация ОМ-3 проводится в рамках комплексной программы развития Михайловского ГОКа, направленной на увеличение объемов выпуска и повышение качества продукции с высокой добавленной стоимостью, — отметил начальник ФОК Дмитрий Ващенко. — Спрос на качественные окатыши сегодня очень высок, кроме того, использование этого сырья позволяет металлургам сокращать выбросы в атмосферу. Увеличение производительности ОМ-3 даст нам возможность завоевания новых рынков сбыта. ОМ-3 модернизируется в несколько этапов».
В 2018 году «Металлоинвест» ввел в эксплуатацию на Михайловском ГОКе комплекс по приему концентрата Лебединского ГОКа. Использование в производстве дообогащенного сырья губкинского предприятия с содержанием железа 70 % позволяет повысить качество смеси и производить на МГОКе окатыши с содержанием железа 65–67 %. Чтобы наладить выпуск высококачественной продукции, нужно было увеличить производительность ОМ-3.
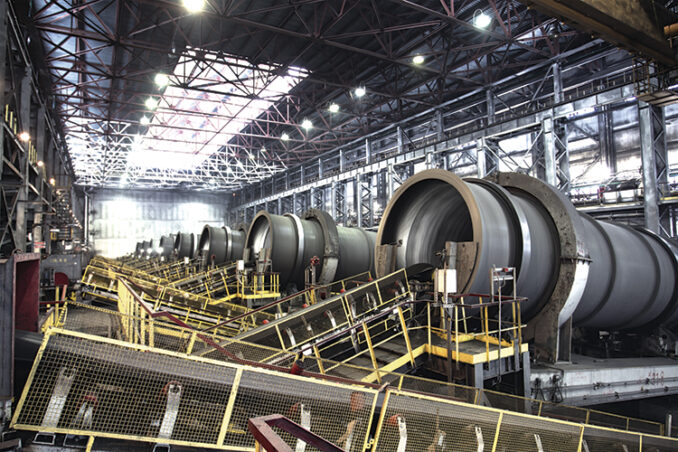
Для начала сотрудники ФОК МГОКа усовершенствовали технологическую схему машины. Модернизированы вакуум-фильтры: их оснастили специальными затворами, работающими в автоматическом режиме.
«Кроме того, установленные ранее тканевые компенсаторы заменили на более надежные — металлические. Тем самым уменьшили теп-лопотери и обеспечили стабильный температурный режим, необходимый для обжига окатышей», — пояснил начальник участка обжига ОМ-3 Сергей Покаленко.
Были проведены и другие мероприятия, направленные на повышение эффективности работы зон сушки и охлаждения обжиговой машины. Для совершенствования системы разгрузки электрофильтров и работы тягодутьевого оборудования между дымососами № 5 и № 6 специалисты фабрики установили специальную перемычку, обеспечивающую равномерное распределение тепловой нагрузки между ними. Внесены изменения в алгоритм работы схемы цепи аппаратов обжиговой машины для организации ее непрерывной работы при кратковременной остановке части оборудования.
Таким образом, на первом этапе реконструкции в 2018 году работники комбината успешно увеличили производительность обжиговой машины на 5 %, с проектной 600 т/ч до 630 т/ч. На втором этапе модернизации ОМ-3 была улучшена теплотехническая схема ОМ-3, и движение «вверх», к повышению качества и объемов, продолжается. Цель — повышение производительности еще на 5 %, до 664 т/ч.
«В настоящее время идут работы на двух участках — сгущения, фильтрации и сырого окомкования (СФиСО) и участке обжига, — объясняет Дмитрий Ващенко. — На первом из них мы устанавливаем роллер-пресс. Он предназначен для внедрения передовой в горнодобывающей промышленности технологии: измельчения концентрата на валках высокого давления».
Сегодня концентрат поступает на ОМ-3 в виде пульпы с обогатительной фабрики. Далее он проходит процессы сгущения, перемешивания, фильтрации и по конвейеру направляется на смешивание с измельченным известняком и бентоглиной. Из полученной смеси изготавливают железорудные окатыши. Удельная поверхность такого концентрата составляет 1 350–1 650 см2/г. Внедрение новой технологической схемы позволит повысить удельную поверхность концентрата не менее чем на 200–300 см2/г за счет дополнительного измельчения на роллер-прессе. Таким образом, концентрат получится более мелкой фракции, что улучшит свойства его окомкования и обжига. Чтобы обеспечить высокое качество обжига, планируется увеличить рабочую площадь самой обжиговой машины за счет удлинения технологических зон сушки и охлаждения.
«УРАЛЬСКАЯ СТАЛЬ»
Предприятие полного цикла, включающее аглококсодоменное, сталеплавильное и прокатное производства.
Новые котлы ТЭЦ «Уральской Стали»
На «Уральской Стали» запущены новые паровые котлы среднего давления теплоэлектроцентрали (ТЭЦ). Инвестиции компании в проект составили более 3 млрд руб.
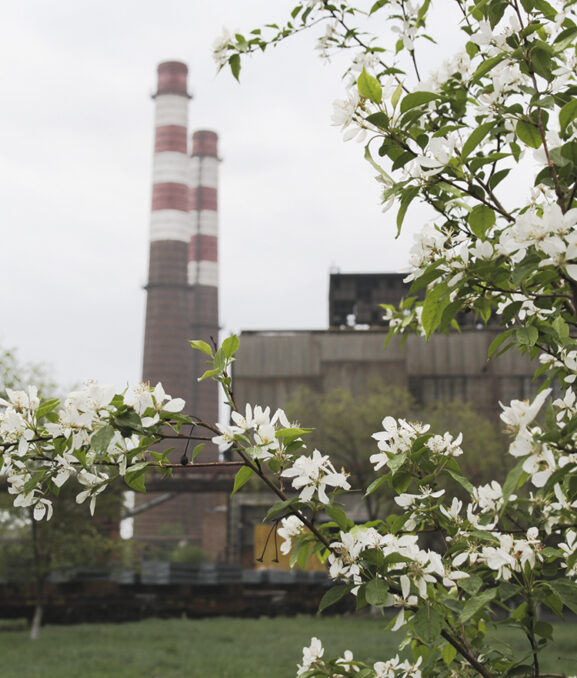
Модернизация ТЭЦ предприятия создает мощный энергетический комплекс суммарной производительностью 440 т пара в час. Котлы работают на природном, коксовом и доменном газе, вырабатывая каждый до 144 Гкал в час. Объем производства тепловой энергии вырос вдвое, обеспечены потребности подразделений комбината в паре необходимого качества. Современные агрегаты обладают высоким коэффициентом полезного действия, позволяют сократить затраты на обслуживание и повышают экологичность.
«Наши инвестиционные проекты нацелены на внедрение передовых технологических решений и снижение нагрузки на окружающую среду, — отметил генеральный директор «Металлоинвеста» Назим Эфендиев. — Запуск котлов среднего давления повышает энергоэффективность производства «Уральской Стали», снижает выбросы парниковых газов».
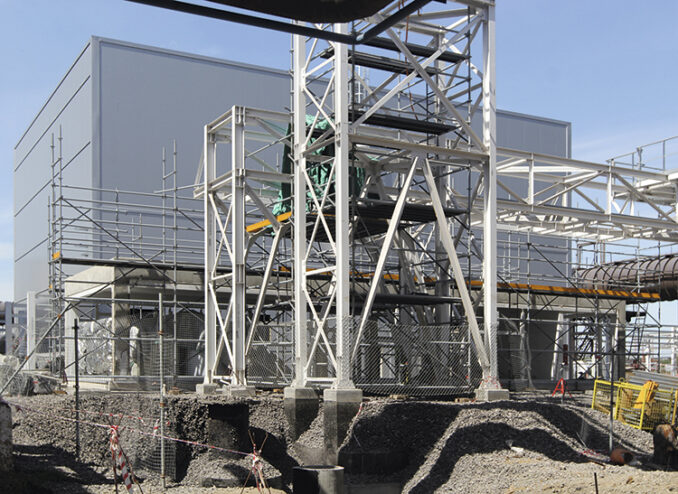
Проект новой котельной включил в себя запуск главного щита управления, химической лаборатории, электроучастка и участка автоматизированной системы управления технологическим процессом. Был произведен монтаж нового насосного оборудования, трубопроводов острого пара, питательной и очищенной воды, главных паропроводов и газопроводов. Реконструирована химводоочистка № 3, смонтирована уникальная автоматизированная установка производства очищенной воды. Заменено электрооборудование трансформатора связи № 2. Котлы полностью автоматизированы и управляются одним человеком при помощи компьютера. Работники ТЭЦ прошли дополнительное обучение по эффективной работе с новыми агрегатами.
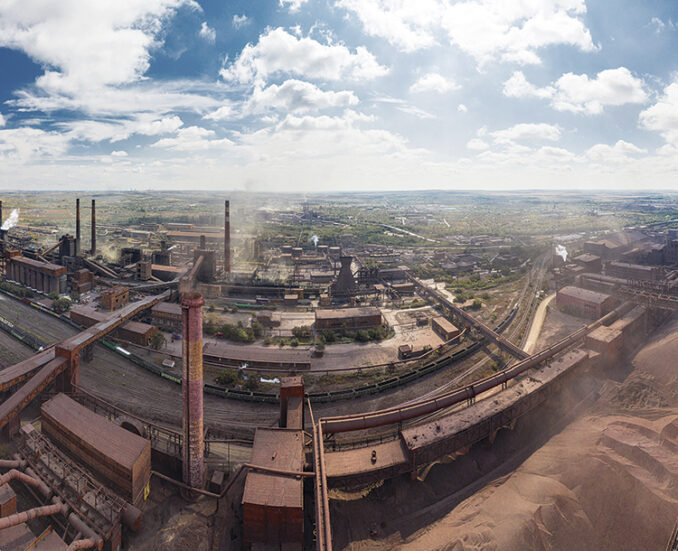
«В соответствии с инвестиционной программой компании «Металлоинвест» по модернизации производственных мощностей «Уральской Стали» реконструкция оборудования ТЭЦ началась в июле 2018 года, — рассказал управляющий директор «Уральской Стали» Ильдар Искаков. — Новейшие котлы с высоким КПД удалось смонтировать за рекордные два с небольшим года. С выводом котлов на проектную мощность не только повысится качество энерго- и теплоснабжения объектов комбината и города, также возрастет надежность энергетических мощностей предприятия».
На следующем этапе реновации ТЭЦ предстоит проектирование и строительство турбогенератора среднего давления мощностью до 60 мегаватт, который будет работать в связке с новыми котлами. В перспективе предполагается последовательная замена пяти котлов высокого давления, турбогенераторов и воздушных компрессоров.
Модернизируя производственные мощности
«Металлоинвест» запускает на «Уральской Стали» обновленную доменную печь № 2.
Компания «Металлоинвест» завершает техническое перевооружение доменной печи № 2 «Уральской Стали». Вместе с реконструируемой домной № 3 она образует современный производственный комплекс, отвечающий высоким экологическим стандартам. Стоимость проекта — более 7 млрд руб.
Для модернизации доменных печей № 2 и 3 «Уральской Стали» в октябре 2018 года «Металлоинвест» заключил контракт на поставку основного технологического оборудования с нидерландской компанией Danieli Corus. Полезный объем печи составляет 1 175 куб. м, проектная мощность — не менее 785 тыс. т чугуна в год. Печь оснащена экспертной системой анализа и регулирования технологического процесса, позволяющей определить оптимальный технологический режим и управлять доменной плавкой в автоматическом режиме, контролируя и анализируя множество параметров.
«Использование двух современных доменных печей на комбинате обеспечит сокращение издержек за счет снижения количества и продолжительности промежуточных ремонтов, сокращения расхода кокса, — рассказал руководитель проекта по модернизации доменных печей № 2 и 3 Андрей Дыга. — По сравнению с классическими печами преимуществом домны от Danieli Corus является возможность работы на шихте с приоритетным использованием железорудных окатышей. Производитель гарантирует работу с максимальной производительностью не менее 15 лет без проведения дорогостоящих капитальных ремонтов. Запатентованная технология футеровки и системы охлаждения позволяет в случае прогара медного горизонтального холодильника оперативно заменить его без остановки печи».
Масштабный инвестпроект «Металлоинвеста» реализуется в рамках стратегической комплексной программы развития производства «Уральской Стали». Ее мероприятия позволят значительно повысить эффективность предприятия и снизить нагрузку на окружающую среду.
Вклад в повышение производительности
«Металлоинвест» и компания Linde реализуют инвестиционный проект по строительству новой воздухоразделительной установки в кислороднокомпрессорном цехе на «Уральской Стали».
Запуск нового комплекса, управление которым будет производиться с применением самых современных ИТ-технологий, намечен на первый квартал 2021 года. Технологические параметры воздухоразделительной установки — 20 тыс. кубометров технического кислорода и 4 тыс. кубометров азота в час — позволят полностью покрыть потребности «Уральской Стали» в высококачественных жидких и газообразных продуктах разделения воздуха. В настоящее время продукты разделения воздуха (кислород, азот и аргон) для структурных подразделений комбината вырабатывают две воздухоразделительные установки (ВРУ).
Проект, инвестиции в который со стороны «Металлоинвеста» составляют порядка 800 млн руб., входит в комплексную программу развития «Уральской Стали», направленную на повышение операционной и управленческой эффективности предприятия. Компания Linde не только строит воздухоразделительную установку, но и в дальнейшем будет обеспечивать работу ВРУ № 6, проводя сервисное обслуживание установки и ее технических устройств.
Привлечение для реализации проекта компании Linde позволило оптимизировать затраты на строительство, а также обеспечить стабильную работу установки и высокий уровень ее технического обслуживания. Как отмечает начальник кислородно-компрессорного цеха «Уральской Стали» Анатолий Семенков, в новой установке, в отличие от ВРУ-4, кислород выходит из блока разделения под давлением, которое не предусматривает потребности в повышающих давление компрессорах.
Еще одним отличием является отсутствие на новой установке двух воздушных и одного дожимающего компрессора, стоящих перед блоком разделения, три функции на ВРУ-6 выполняет один агрегат. О высокой технологичности нового оборудования говорит следующий факт: если сегодня для обслуживания ВРУ нужны три аппаратчика, два машиниста и оператор насосной, то на новой установке будет работать один человек, а высвободившиеся люди будут переведены на другие участки производства. Параметрические данные о работе оборудования будут видны не только оператору, но и доступны в режиме реального времени другим инженерам Linde.
ЛЕБЕДИНСКИЙ ГОРНО-ОБОГАТИТЕЛЬНЫЙ КОМБИНАТ
Лебединский ГОК является крупнейшим в России и СНГ предприятием по добыче и обогащению железной руды, производству высококачественного железорудного сырья и металлоресурсов. Это единственный в России и СНГ производитель ГБЖ. Предприятие ведет открытым способом разработку железорудного месторождения. Карьер занесен в Книгу рекордов Гиннесса как крупнейший в мире по добыче негорючих полезных ископаемых.
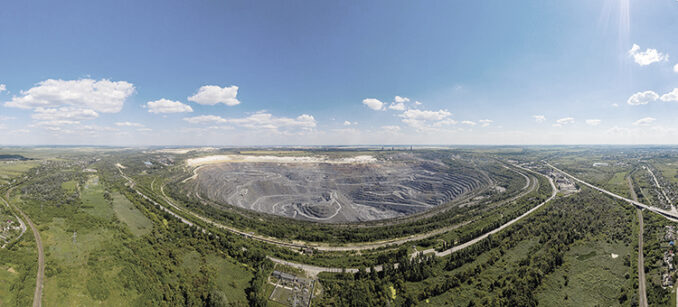
Экономить на энергоресурсах
В 2018 году на Лебединском ГОКе была успешно завершена реализация первого этапа проекта внешнего электроснабжения (ВЭС).
Это обеспечило предприятию около 600 млн руб. ежегодной экономии. В настоящее время на Лебединском ГОКе завершается реализация следующих этапов этого масштабного инвестиционного проекта компании «Металлоинвест»: второго и третьего пускового комплекса подстанции 330 киловольт (кВ) «Лебеди». Проект обусловлен ростом электрических нагрузок комбината, связанных с перспективным развитием подразделений, а также необходимостью экономически более выгодного перераспределения потоков электрической энергии.
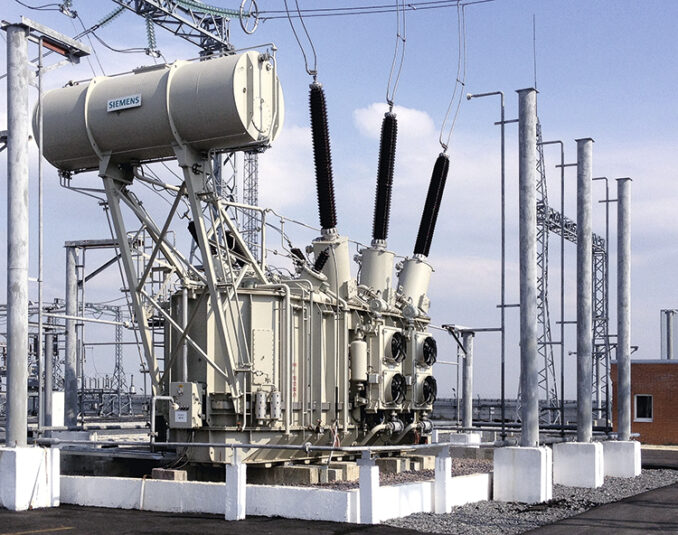
Для запуска 2-го пускового комплекса был выполнен комплекс работ по установке и монтажу оборудования. Для его надежной и бесперебойной работы производится расширение и модернизация системы релейной защиты и автоматики на базе современных микропроцессорных устройств. Ведется строительство современной системы цифровой связи.
Ввод в работу второго пускового комплекса подготавливает к замыканию транзита в сети 330 кВ между подстанциями 750 кВ «Металлургическая» и 330 кВ «Белгород». А главное — обеспечивает подготовку к реализации третьего пускового комплекса. Для этого уже выполнены работы по монтажу двух секций шин 110 кВ на 16 ячеек с выключателями, что позволит перевести часть воздушных линий 110 кВ со старой площадки на новую, сформировать резервные присоединения для будущих распределительных устройств. Система релейной защиты и автоматики расширена аналогично второму комплексу. На новой площадке подстанции 330 установлен автотрансформатор мощностью 200 МВА (АТ-2) и оборудование, обеспечивающее его работу. Также построен новый участок двухцепной воздушной линии протяженностью 7,5 км, переустроен заход одной ВЛ 330 кВ и шести ВЛ-110. Комплекс этих мероприятий позволяет передавать дополнительный объем электроэнергии из сетей РАО «ЕЭС» в сеть комбината. Для эффективного контроля за потреблением электроэнергии расширена система, действующая с реализации первого пускового комплекса проекта.
«В настоящее время завершены все основные строительно-монтажные работы, производится пусконаладка и предпусковая ревизия основного технологического оборудования, — сообщил руководитель проекта по развитию системы внешнего электроснабжения Лебединского ГОКа Евгений Евдаков. — Ввод в эксплуатацию 2-го и 3-го пускового комплекса подстанции «Лебеди» 330 кВ запланирован на декабрь 2020 года».
Проект стратегической важности
На Лебединском ГОКе ведется строительство комплекса циклично-поточной технологии (ЦПТ). Компания «Металлоинвест» инвестировала в его реализацию почти 12 млрд руб.
Реализация масштабного инвестиционного проекта компании позволит повысить эффективность производства и снизить себестоимость готовой продукции. Внушительный и высокотехнологичный проект вступил в стадию активного развития весной 2020 года. Гигантская лента магистрального конвейера длиной более 3 км соединит ярусы Лебединского карьера с участками № 1 и 2 цеха крупного дробления обогатительной фабрики, заменив тем самым транспортировку руды железнодорожными составами. Таким образом, путь транспортировки руды станет значительно короче и дешевле.
Строительство ведется в несколько этапов, близится к завершению первый. Смонтированы металлоконструкции каркаса одного из самых важных объектов комплекса — здания приводных и натяжных станций. Подрядчики готовы приступить к его обшивке, а затем и монтажу основного технологического оборудования внутри. Одновременно продолжается возведение буферного склада, предназначенного для хранения запаса руды (до 260 тыс. т) на случай плановых остановок на ремонт дробильных установок и магистрального конвейера. Постоянный запас сырья обеспечит непрерывный процесс производства продукции.
За пополнение склада и передачу дополнительной руды на обогатительную фабрику будет отвечать уникальное оборудование — стакер-реклаймер. Этот промышленный роторный экскаватор удивляет своими габаритами — 44-метровой стрелой (длина всего агрегата — 66 м) и 15-метровой высотой (выше пятиэтажного дома).
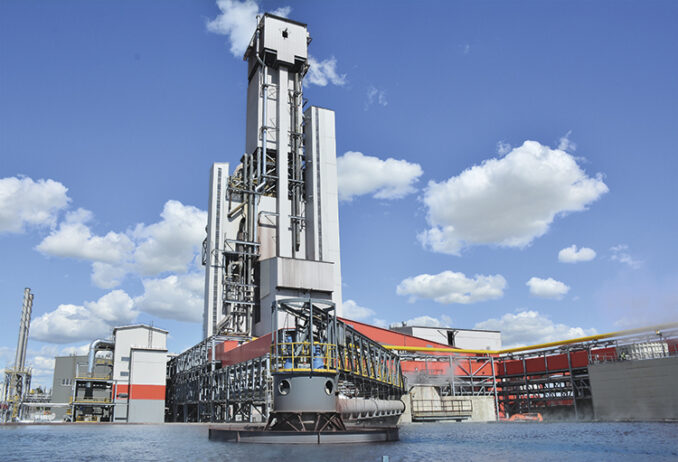
«В карьере идет подготовка основания под строительство конвейера и дробильных установок. Самое важное на данный момент — завершить все фундаментные работы до наступления холодов и укрыть основные объекты от осадков, чтобы в дальнейшем спокойно устанавливать оборудование, — отметил руководитель проекта ЦПТ на Лебединском ГОКе Вадим Барышев. — Следующим этапом станет реконструкция железнодорожных путей в районе участков № 1 и № 2 ЦКД и возведение еще нескольких необходимых объектов, затем — монтаж двух дробильных установок в карьере на отметке минус 60, а весной-летом 2021 года начнем укладку конвейерной ленты. Специально рассчитываем на теплое и сухое время года».
На стройплощадке сегодня трудятся около 170 специалистов. «Мы постоянно поддерживаем со специалистами по шефнадзору связь и держим их в курсе всего, что происходит на объектах строительства. На время пандемии удалось найти решение, как они могут наблюдать за нашими успехами дистанционно: в районе участков № 1 и 2 цеха крупного дробления обогатительной фабрики, а также диспетчерской рудоуправления установили три видеокамеры с высоким разрешением. Так что в режиме онлайн иностранные коллеги могут следить за ходом строительства», — прокомментировал Вадим Барышев.
В целом ситуация с COVID-19 на развитие событий не повлияла: на объектах ежесменно ведутся работы. Естественно, с соблюдением всех профилактических норм. Строительство движется согласно графику. Завершить его планируется к концу сентября 2021 года.
Высокая степень ответственности
В 2020 году завершились работы по двум объектам инфраструктуры комплекса ГБЖ-3.
Вопросы снижения воздействия производственных факторов на окружающую среду для «Металлоинвеста» в приоритете. В 2019 году утверждена экологическая программа, предусматривающая инвестиции в размере более 21 млрд руб. При этом 70 % бюджета программы составит проект «Чистый воздух».
Проекты модернизации производства в целях снижения выбросов в атмосферу реализуются на предприятиях компании на протяжении нескольких
лет. Один из них — модернизация системы газоочистки на фабрике окомкования Лебединского ГОКа. Техническое перевооружение обжиговой машины № 4 предусматривало замену двух аппаратов «мокрой» и «сухой» газоочисток на более производительные и эффективные электрофильтры. Строительство установки очистки отходящих технологических газов из зон сушки и нагрева обжиговой машины № 4 началось в марте 2017 года. При этом реализация проекта происходила в условиях действующего производства.
Сегодня проводятся пусконаладочные работы на установке электрофильтрации участка шихтоподготовки. Здесь принимают и перерабатывают связующие и флюсоупрочняющие добавки: бентонит, известняк, боксит, которые смешивают с основным компонентом — железорудным концентратом для получения окатышей с необходимым химическим составом и физическими свойствами. Но перед этим вспомогательные вещества дробят.
«При производстве измельченного продукта образуется большое количество пыли, которую необходимо уловить, не допустить ее попадания в атмосферу. Установка высокоэффективных электрофильтров на нашем участке способствует более качественной очистке воздуха», — комментирует начальник участка шихтоподготовки фабрики окомкования Лебединского ГОКа Роман Быков.
В электрофильтре пыль в виде заряженных частиц оседает на электродах внутри установки, а затем стряхивается в осадительные бункеры. Ежечасно фильтр пропускает через себя 211 тыс. куб. м воздуха. Количество вредных примесей в газовой смеси, поступающей на пылеочистку, составляет порядка 9 мг/м3. На выходе из электрофильтра показатель уже равен 0,4 нанограмма: фактически выходит очищенный воздух. Помимо существенного снижения нагрузки на окружающую среду, новая система фильтрации помогает предотвратить производственные потери. «При установке электрофильтров снижаются потери технологических материалов. Если при «мокрой» системе газоочистки некоторую часть технологической пыли мы были вынуждены смывать в промстоки, то с появлением электрофильтров уловленную пыль пускаем обратно в производство», — отмечает начальник участка.
По окончании пусконаладочных работ свой вердикт вынесут экологи и представители управления технического контроля комбината, которые инструментально подтвердят эффективность работы установки фильтрации. После чего она будет запущена в промышленную эксплуатацию.
Строительство современного пожарного депо, включающего собственно депо на шесть спецавтомашин, здание газодымозащитной службы и учебно-тренировочную башню, — еще один инвестиционный проект «Металлоинвеста», реализованный в инфраструктуре комплекса ГБЖ-3.
Бойцы отряда пожарной части № 57 ведут круглосуточную охрану объектов Лебединского ГОКа и близлежащих населенных пунктов. Ранее подразделение базировалось на промплощадке комбината, здание было не таким просторным, а депо могло вместить лишь три машины.
Переезд на новую базу предоставил массу преимуществ: улучшились не только бытовые условия, но и техническое оснащение. Закупили новые компрессоры для закачки кислорода в дыхательные аппараты, насосные станции. Появилась возможность на месте ремонтировать технику.
«Не в каждой области есть такое депо и учебно-тренировочная база, где будет проходить подготовку личный состав. С помощью дымокамер, дымогенераторов и различных тренажеров сотрудники могут оттачивать навыки в условиях, приближенных к реальным при тушении пожара: задымление, нулевая видимость и так далее. Это способствует слаженной работе команды в экстремальных условиях», — отмечает Руслан Казаев, начальник 3-го отряда Федеральной противопожарной службы по Белгородской области.
Еще одно преимущество нового депо — удобное расположение. Теперь в оперативной доступности пожарных еще больше объектов Лебединского ГОКа. А значит, работа по обеспечению безопасности сотрудников поднялась на более высокий уровень.
Справка:
«Металлоинвест» — мировой лидер в производстве товарного горячебрикетированного железа (ГБЖ), ведущий производитель и поставщик железорудной и металлизованной продукции, один из региональных производителей высококачественной стали.
Компания обладает вторыми по величине в мире разведанными запасами железной руды — около 13,9 млрд т по международной классификации JORС (IMC Montan), что гарантирует около 137 лет эксплуатационного периода при текущем уровне добычи.